Coreform Case Study
Market: CAE, FEA
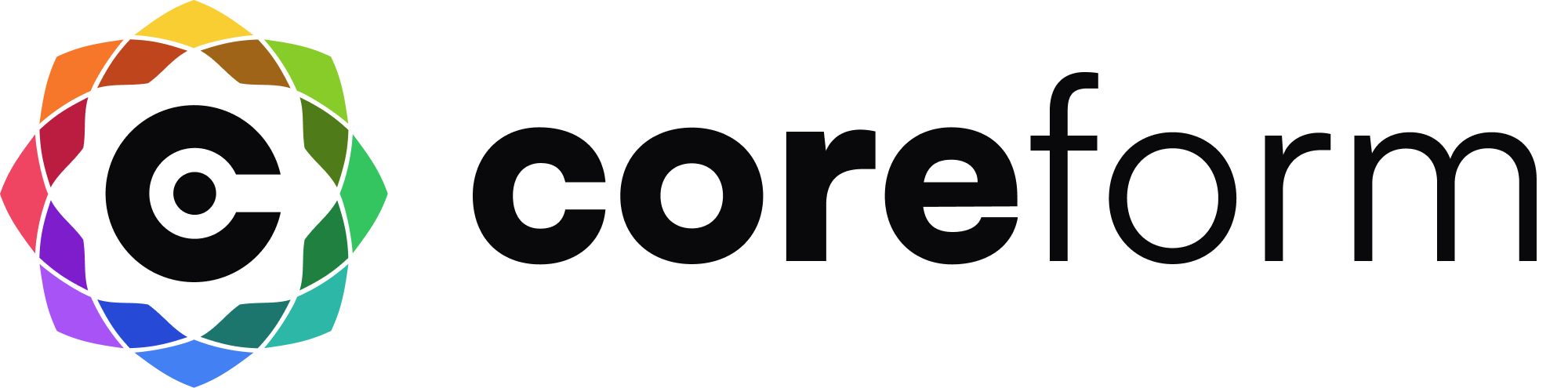
-1.png)
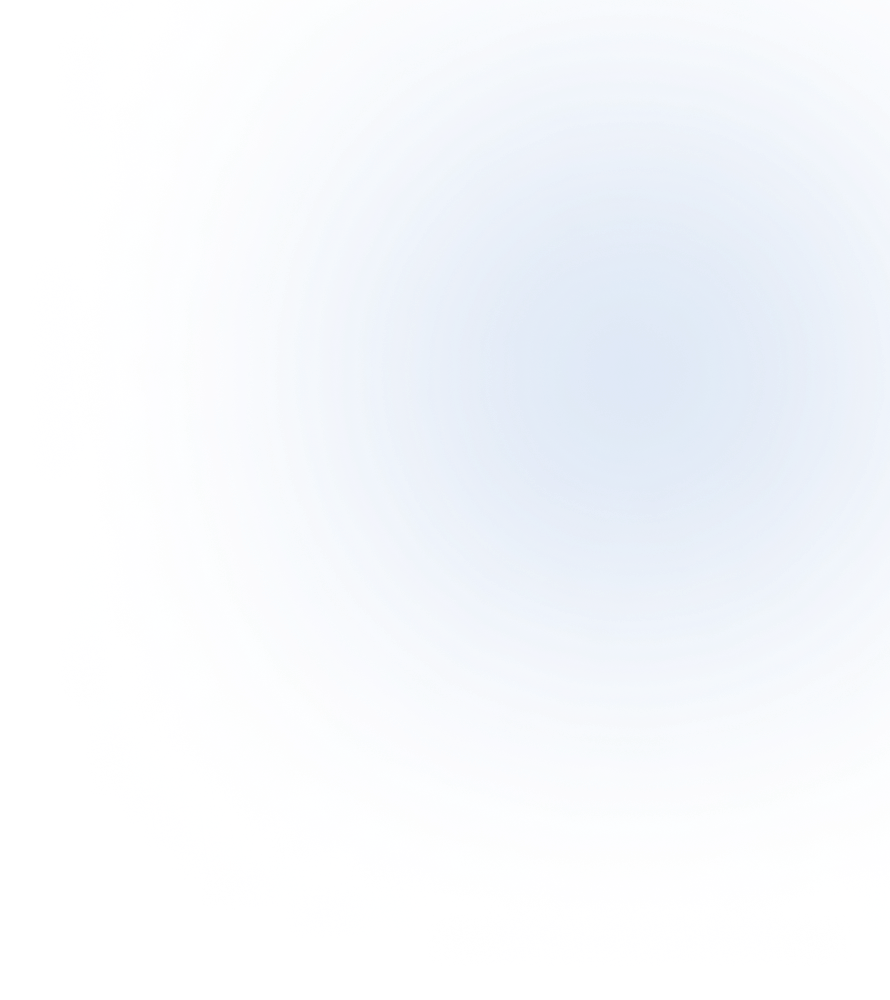
Summary
With the motto “simulation without compromise”, Coreform aims to accelerate engineering design through easier and more powerful FEA. They leverage cutting-edge techniques from FEA and computational geometry to streamline the process of setting up FEA models while providing simulation results that are more accurate and robust than traditional low-order FEA across linear, nonlinear, static, and dynamic simulation regimes. Since their software handles CAD parts, they needed the ability to run simulation data
with the most precise geometrical data possible and required geometry import and Boolean preprocessing for their solver.
They relied on their long-standing relationship with Spatial to integratebindustry-leading components into their software, enabling them to fully address the challenges of simulation software.
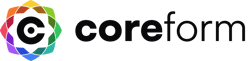
We were able to achieve better results with ACIS than we could have on our own, and their willingness to engage with us to meet our specific needs resulted in a product we are confident about delivering to customers.
The Company
Since 2014, Coreform has provided innovative isogeometric analysis software to the CAE industry. Coreform delivers reliable results to accelerate design processes, leveraging cutting-edge techniques in Finite Element Analysis (FEA) and computational geometry. With Coreform’s isogeometric analysis (IGA) technology, it will be possible to eliminate the meshing process while offering simulation results that are more accurate and robust than traditional low[1]order FEA across linear, nonlinear, static, and dynamic simulation regimes.
Coreform was founded around solving a common problem in the CAE space: how time is spent and lost in simulation. The vast majority of simulation time is spent on non-value-added activities. While these preparatory activities are necessary for the simulation, they are still peripheral to the primary goal of having the simulation provide you with insight into your engineering design. The tension between model-building speed and engineering simulation accuracy and robustness is a long-standing, seemingly intractable paradox in commercial FEA. Many products have been developed that optimize one at the expense of the other, often within a limited range of physics. Coreform is addressing this problem by developing advancements to the finite element method that allow users to reduce model-building time with greater accuracy and robustness, across a range of applicability.
They are seeking to build simulation technology capable of handling linear-type phenomena all the way up through sophisticated non-linear time-dependent phenomena. As a result, Coreform software allows its customers to produce accurate simulation results in far less time than with traditional methods. What used to take weeks or even months can now be built in days or a week, depending on the size of the assembly.
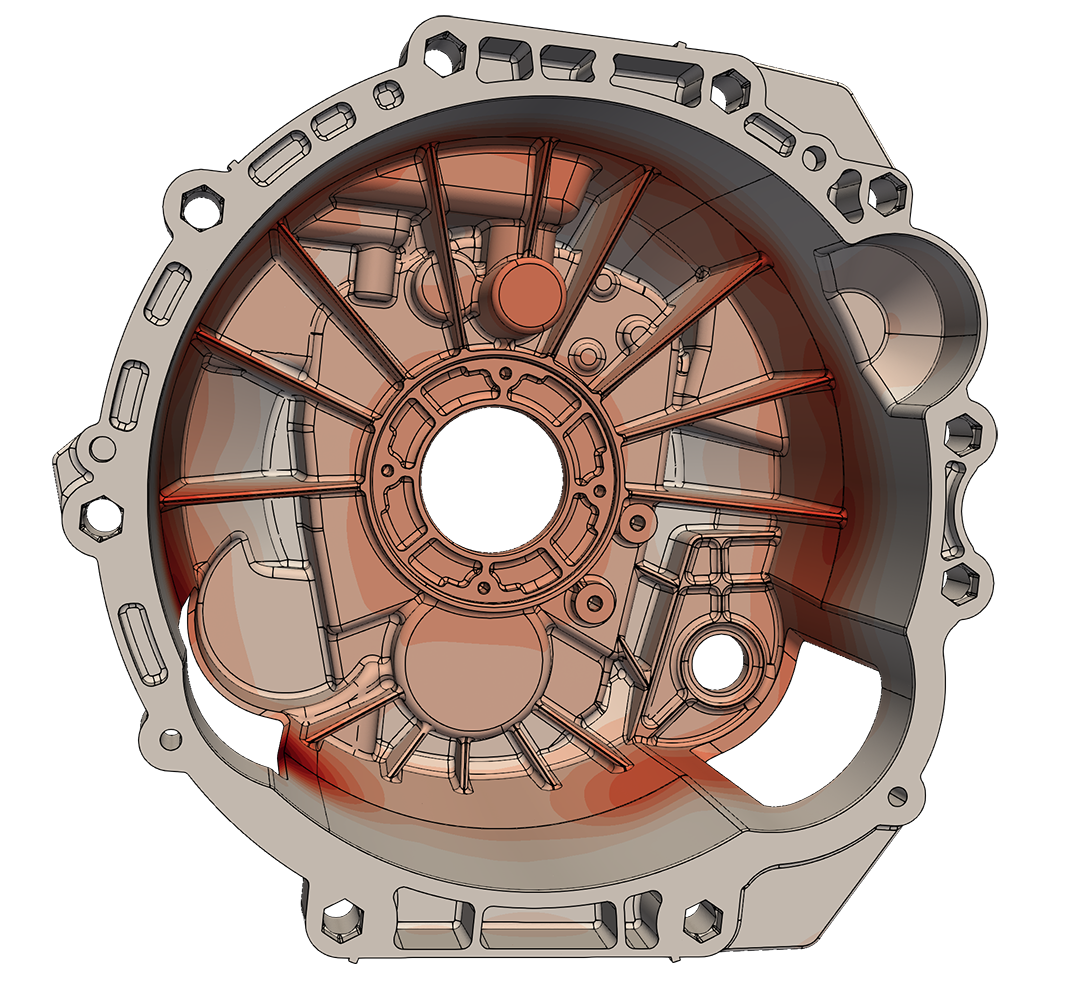
The Challenge
Precise Geometry Import and Boolean Preprocessing
Coreform wanted to dramatically reduce the cost of doing advanced engineering simulation without any additional burden on their customers regarding their CAD system.
Coreform’s solution would have to read native CAD data file as well as exchange formats like STEP, thus they needed high quality CAD geometry import capabilities. The reality was that traditional meshing capabilities needed massive engineering time and were simply a means to an end. By utilizing their innovative IGA solver technology, their simulation method sidesteps the need for traditional meshing and pre-processing. They knew they needed a robust and precise 3D geometry kernel capable of special Boolean preprocessing for this methodology.
This 3D modeler would need to perform millions of
face/face intersections and up to millions of edge/face
intersections. The ideal right 3D modeler would allow
Coreform to close the loop on time spent on non-valueadded activities during the simulation and deliver on its
promise to save its customers valuable time.
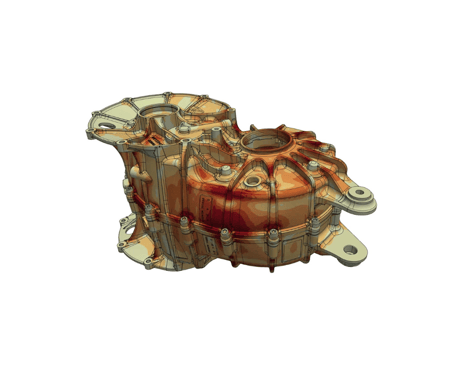
.png?width=450&name=Copy%20of%20Copy%20of%20Untitled%20Design%20(2).png)
.png?width=450&name=Copy%20of%20Copy%20of%20Untitled%20Design%20(1).png)
The Solution
Customized 3D Modeler, Interoperability, and Meshing Solutions
Coreform had a long history with Spatial as a trusted partner since 2019. They saw Spatial as a leader in the CAD and CAE domain. Coreform’s development team was already familiar with and capable of developing on top of Spatial Software Development Kits (SDKs) from their utilization in the Coreform Cubit software. Coreform integrated Spatial SDKs to support all the pre-processing parts of the Coreform Flex workflow. For their meshing software, Coreform Cubit, Coreform was already licensing Spatial’s 3D ACIS Modeler and 3D InterOp, and the legacy version of Meshgems. The preprocessor in their new IGA solver, Coreform Flex, uses 3D ACIS Modeler and 3D InterOp.
Coreform Flex directly uses CAD models in the simulation without defeaturing or conformal meshing, enabling real-time analysis.
Innovative Use of 3D ACIS Modeler
The advantage of 3D ACIS Modeler in Coreform Flex is that it has low-level API (Intersectors) access that Coreform was able to capitalize on and implement in extremely high-performance intersections. IGA technology is innovative and, therefore, requires the innovative use of the ACIS modeling kernel to enable the direct geometric processing deployed in the IGA solver. ACIS is the Spatial solution on which Coreform is most focused; it is used at a deep level and interacts with the core kernel representation for CAD data.
Spatial and Coreform collaborated on the exact needs of the software and adapted 3D ACIS Modeler to meet Coreform’s expectations regarding Boolean operations.
Bringing the Action Plan to Life
From the beginning of the project, Spatial provided Coreform developers with comprehensive support from Spatial technical sales managers and the ACIS R&D team. Spatial support was there to answer advanced questions and implement complex Boolean operations within ACIS. Spatial provided an internal ACIS developer with whom Coreform developers met daily to ensure support every step of the way.
Coreform also contracted with Spatial for an extra service package to continue complex software developments.
.png)
.png)
.png)
Key Insights
After implementing Spatial SDKs, Coreform entered into a new paradigm for generating computation models and simulated models. They anticipate this outcome being adopted by customers in a wide range of industries.
As a result of the fully built-out software, Coreform found that their customers’ simulation engineers could save 80-90% of the time that they traditionality spent on meshing. This makes simulation a more reliable tool from a business perspective, and frees engineers to do more with their valuable time.
Spatial enabled Coreform to obtain the required information early enough in the process that they were able to launch the product earlier than expected. Spatial’s support team was engaged and willing to co-build with the Coreform developers and improve the software and evolutions.
By complementing their innovative technology with Spatial’s cutting-edge solutions, Coreform’s simulation technology dramatically reduces the investment in model building (i.e., mesh generation, CAD defeaturing, etc.), with no compromise on the results and precision. As a consequence, Spatial’s SDKs help improve simulation accuracy and robustness for linear, nonlinear, static, and dynamic problems.
Download the Full Case Study
Want to see a more detailed breakdown of how Coreform utilized Spatial’s powerful components in their application? Download the full case study by clicking below.
Read More Spatial Case Studies
See how our industry-leading SDKs have helped countless businesses across several verticals. Browse
some of our other case studies below.
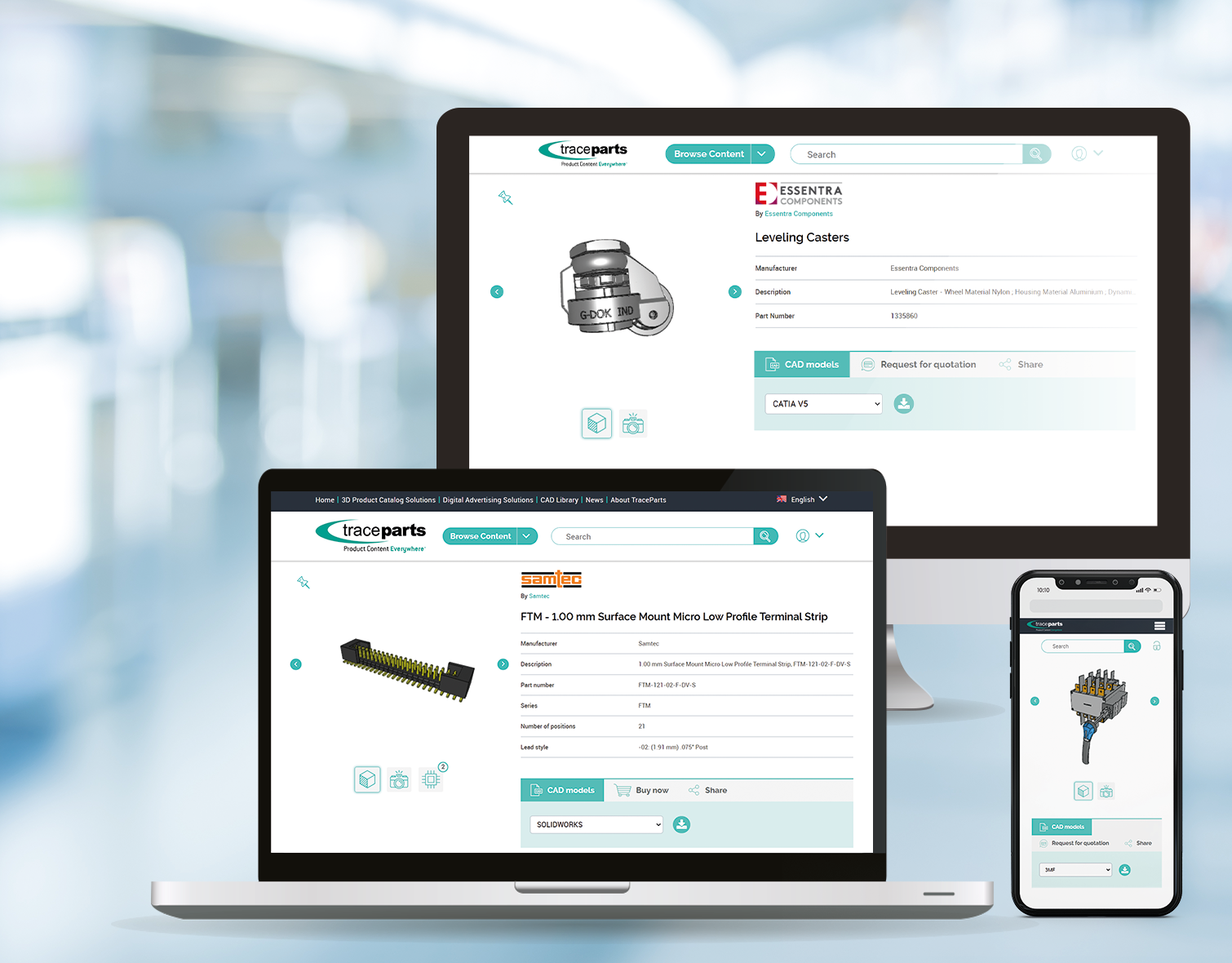
TraceParts enhances 3D Web Viewer Capabilities
TraceParts, a well-known CAD content supplier, integrates robust 3D visualization into their online 3D part viewer to enhance customer ordering experience.
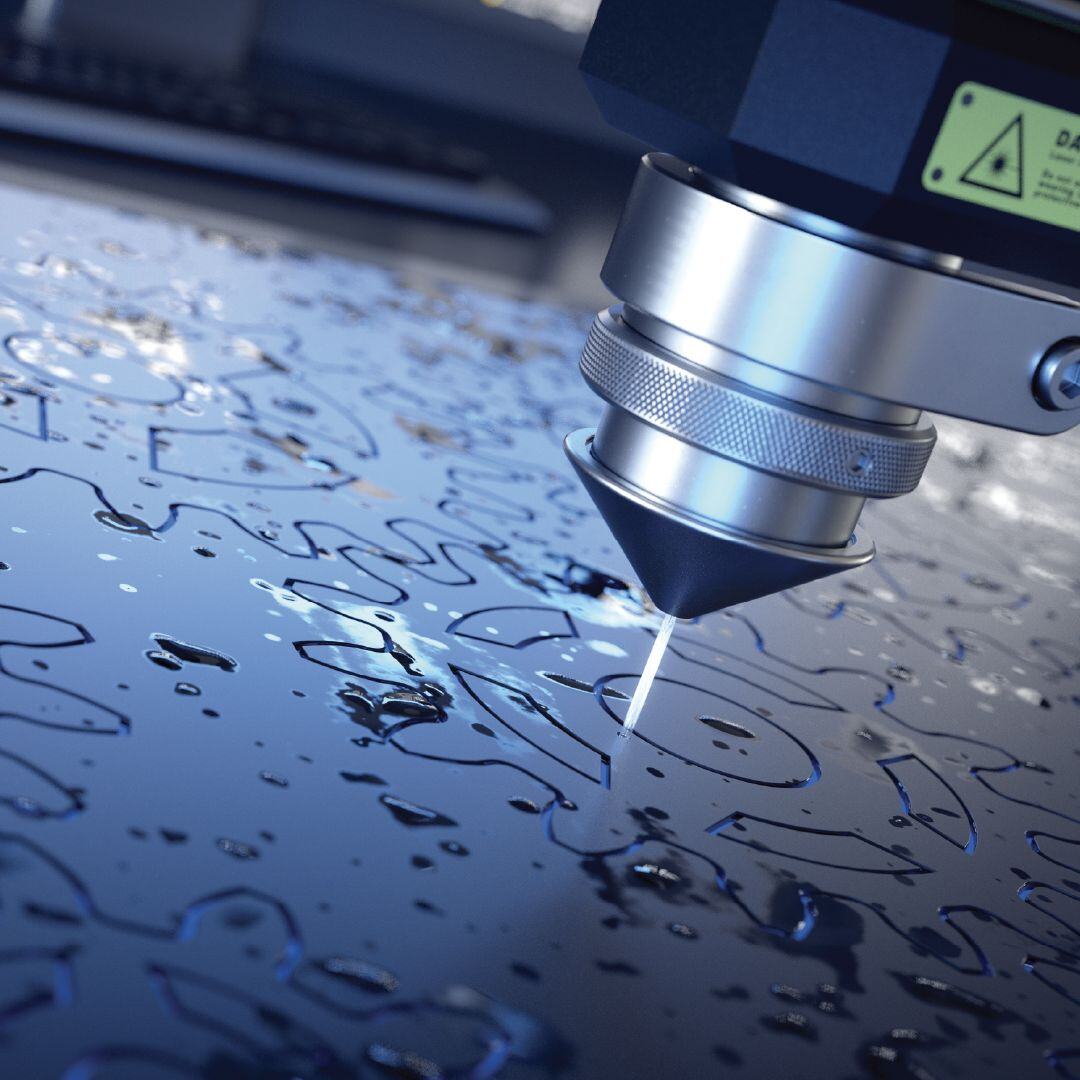

Prototek Released Advanced Digital Manufacturing Quoting
Prototek IQ, empowered by Spatial components allow instant quoting for 3D models. It saves customers’ time, alleviates administrative tasks, and opens new opportunities in digital manufacturing.
-1.png)
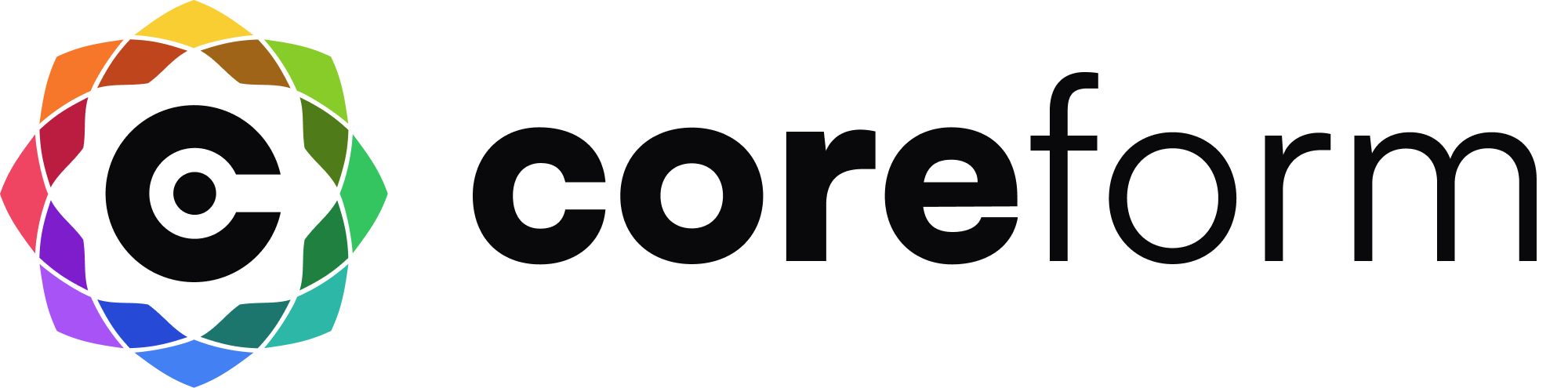
Coreform Brings Game-Changing Simulation Software To Life
Coreform was poised to make a real impact on the CAE world. By integrating specific Spatial SDKs customized to their needs, Coreform closed the circle on its revolutionary software.
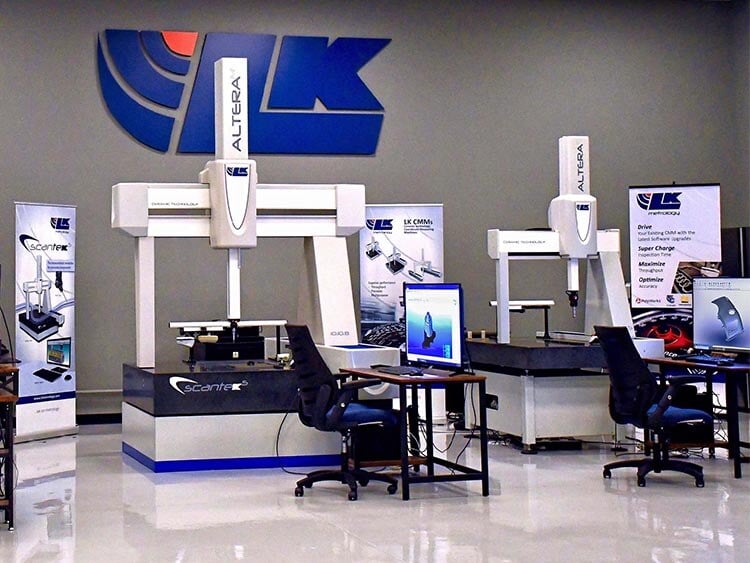
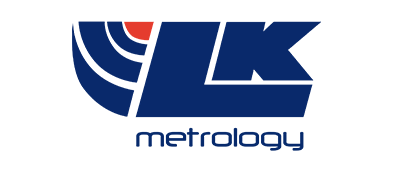
LK Metrology Future Proofed their Application
LK Metrology was on a quest to maintain precision for their Coordinate Measuring Machines. They improved core application functionality through a development partnership with Spatial.
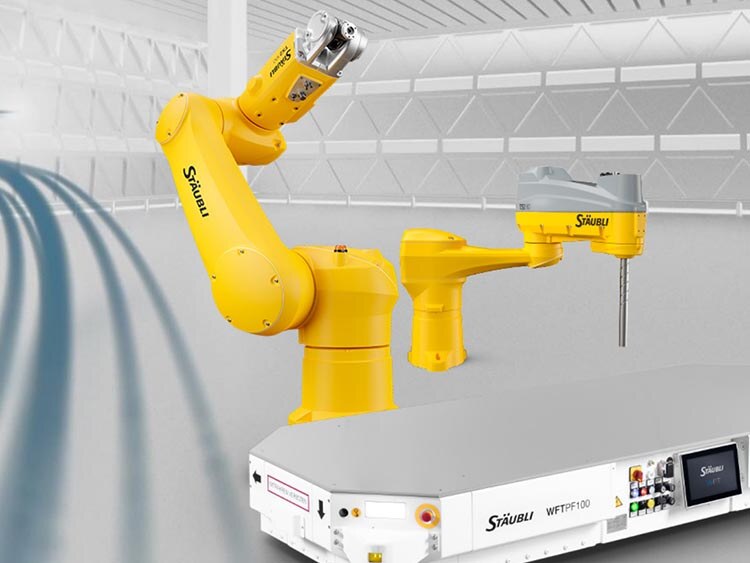
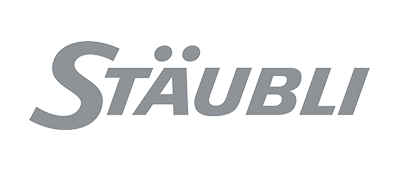
Stäubli Elevated Their Offerings and Capabilities with Spatial's SDKs
Stäubli Robotics Suite 2022 offered optimized features for complex automation scenarios, enabled by Spatial’s CGM Modeler.
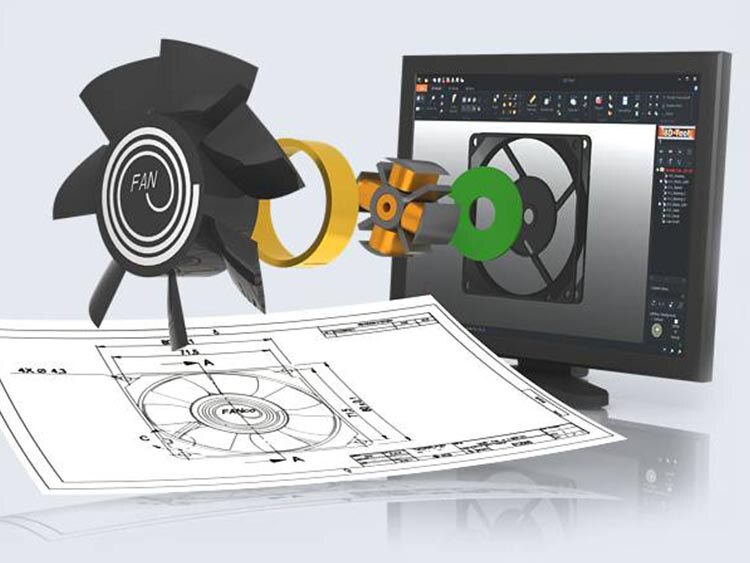
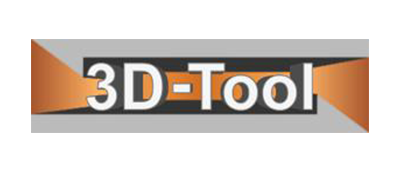
3D-Tool Maximized Customer License Upgrades
3D-Tool expanded Viewer functionality to native CAD formats like CATIA V5 and Pro/E, enabling users to view and translate native CAD files without costly conversion.
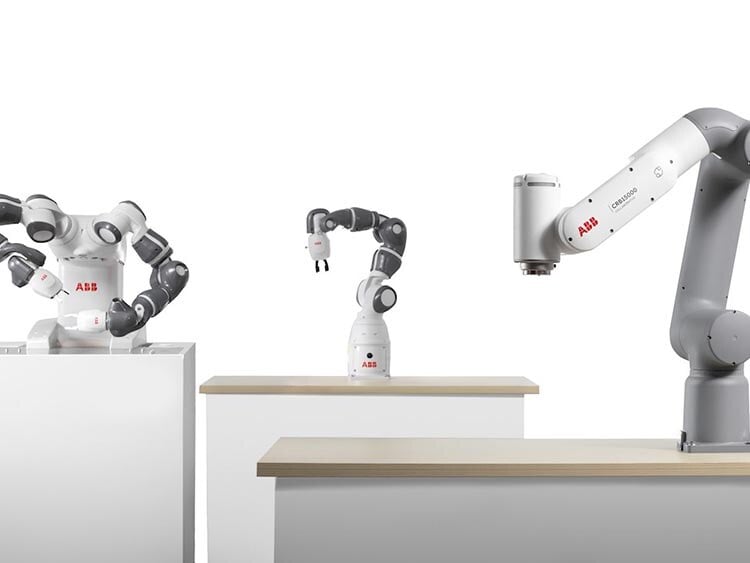
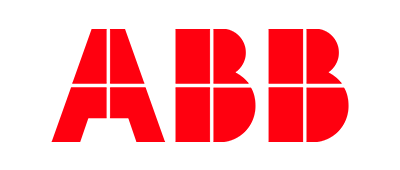
ABB's Programming Without Shutting Down Production
ABB’s Robotics Division used RobotStudio software for PC-based robot programming, boosting productivity without production shutdowns.
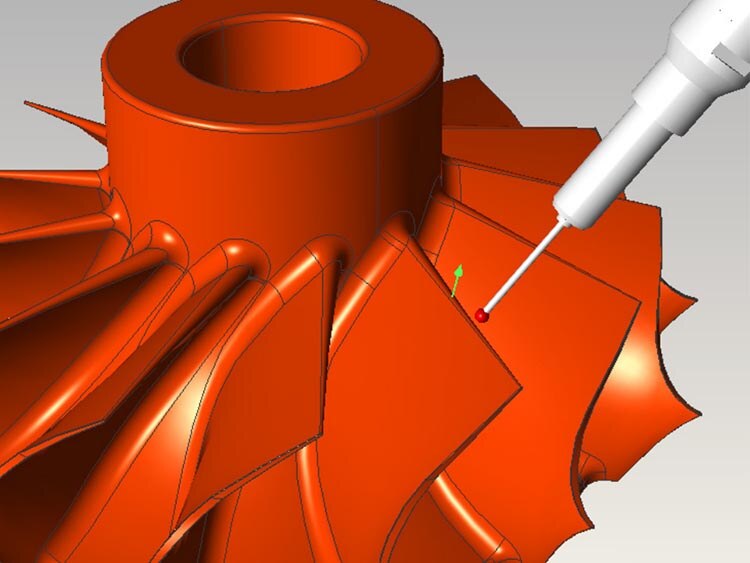
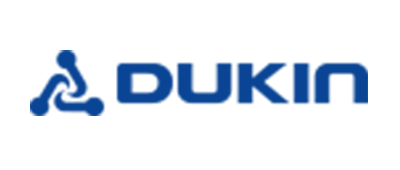
Dukin Co Slashed Development Costs by 50%
Dukin used 3D ACIS Modeler to focus on core technology, reducing time spent on solid modeling and accelerating new product development.
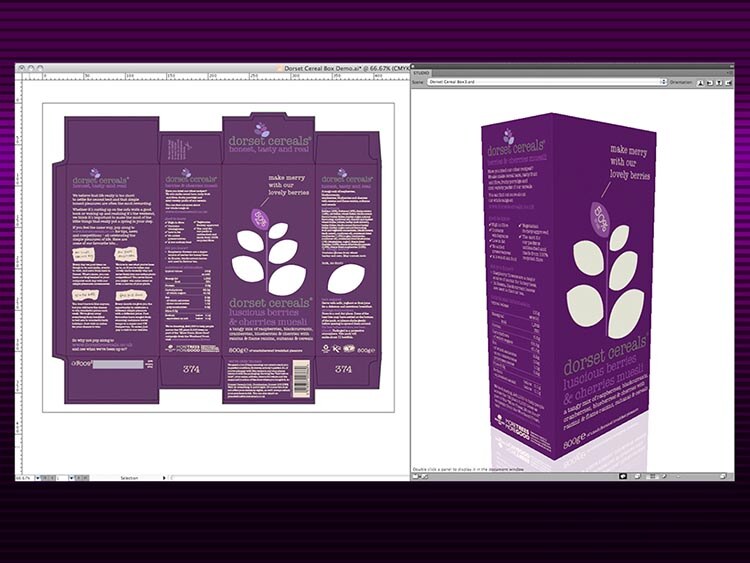
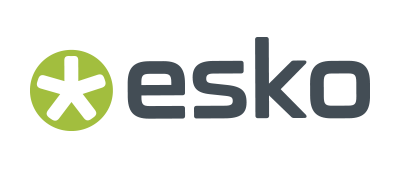
EskoArtwork Drastically Reduced Preparation of CAD Models for Downstream Use
EskoArtwork's ArtiosCAD gained 3D CAD model import functionality, maintaining competitive edge without straining in-house resources.
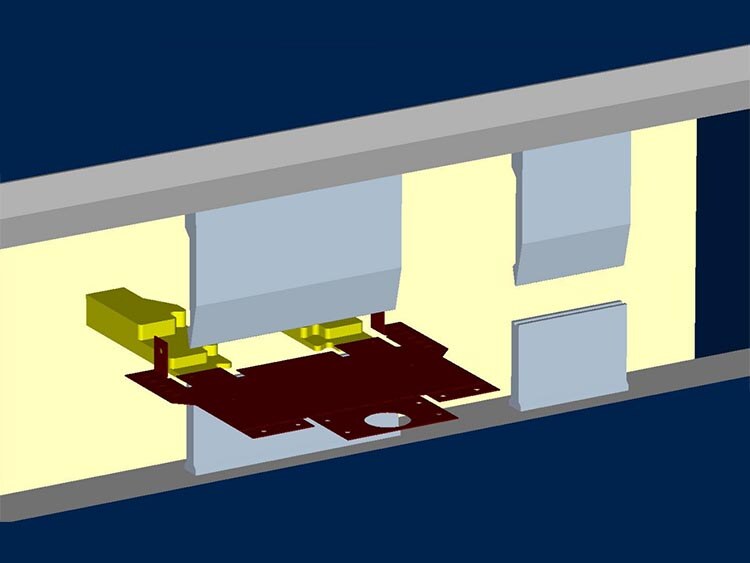
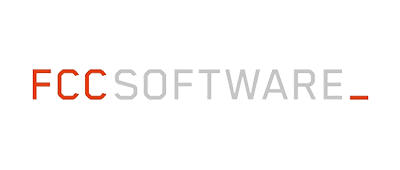
FCC Increased Production Time by 20x
A leading CAM software provider for sheet metal manufacturing used 3D ACIS Modeler for robust 3D modeling and simulation.
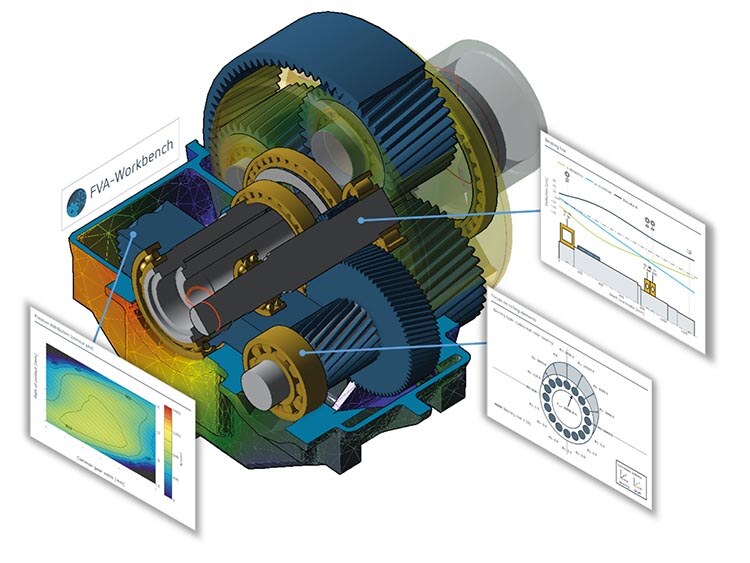
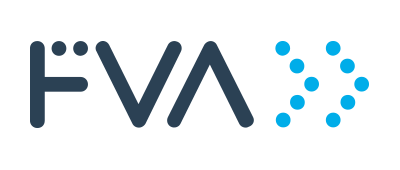
FVA Accelerated Support for New and Updated CAD Formats
FVA's solutions served the driveline industry with software capable of sophisticated simulations and detailed analyses of gearbox components.
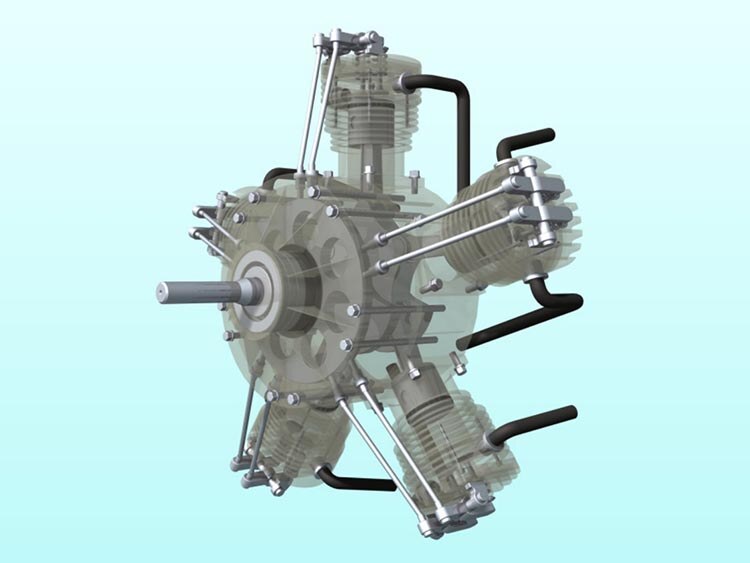
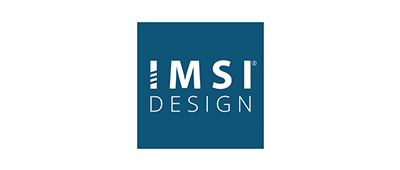
IMSI Accelerated Time-to-Market for New Features
IMSI/Design integrated new versions of ACIS quickly, bringing a new version of TurboCAD to market every 12-15 months.
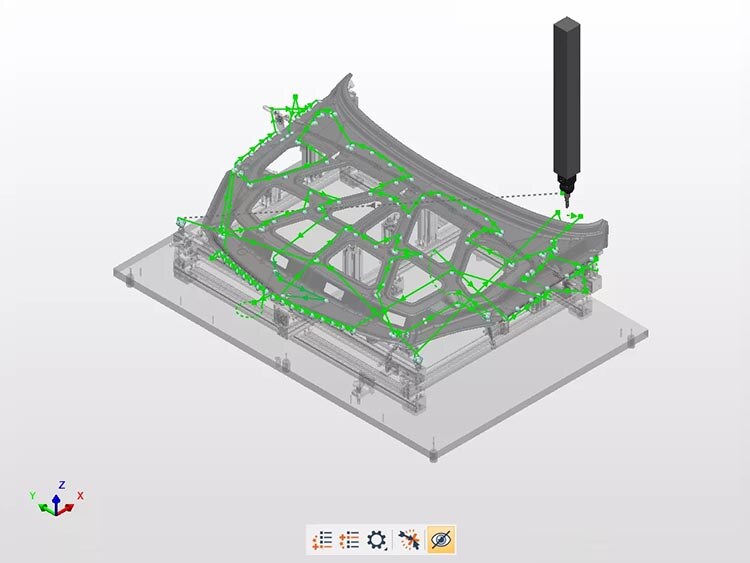
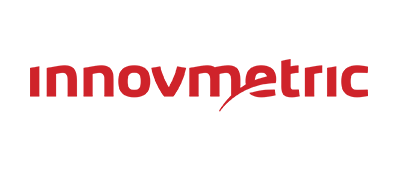
InnovMetric Eliminated Nearly 100% of Their Translation Errors
InnovMetric provided their automotive and aerospace customers with top CAD translators in PolyWorks® by selecting Spatial InterOp software.
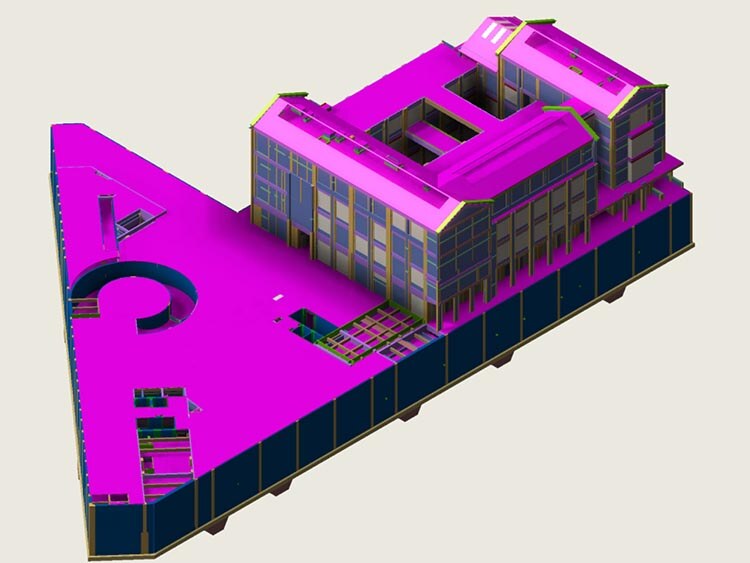
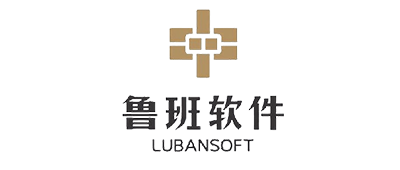
Lubansoft Boosted Design Quality and Reduced Costly Errors
Lubansoft boosted design quality and reduced errors in their BIM software by using 3D ACIS Modeler and HOOPS Visualize.
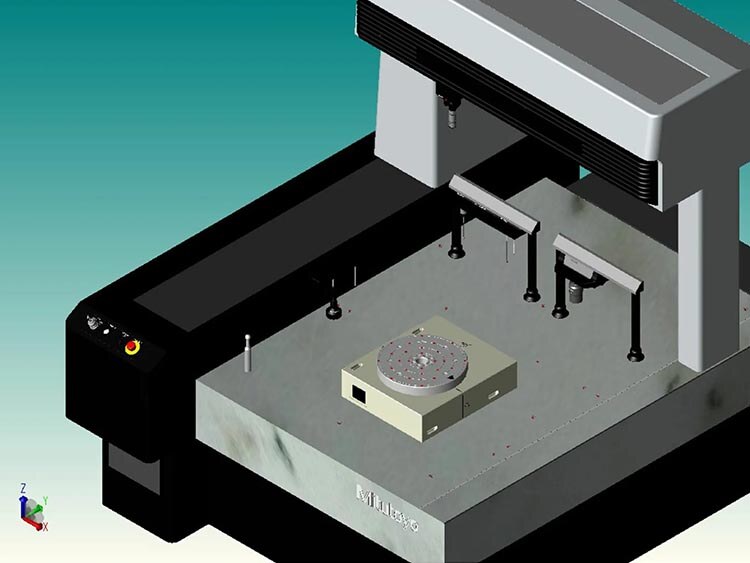
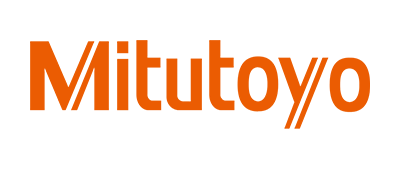
Mitutoyo Supercharged Their 3D Interop Translation
Mitutoyo broadened the use of Spatial technology to other parts of the organization, such as machine configuration.
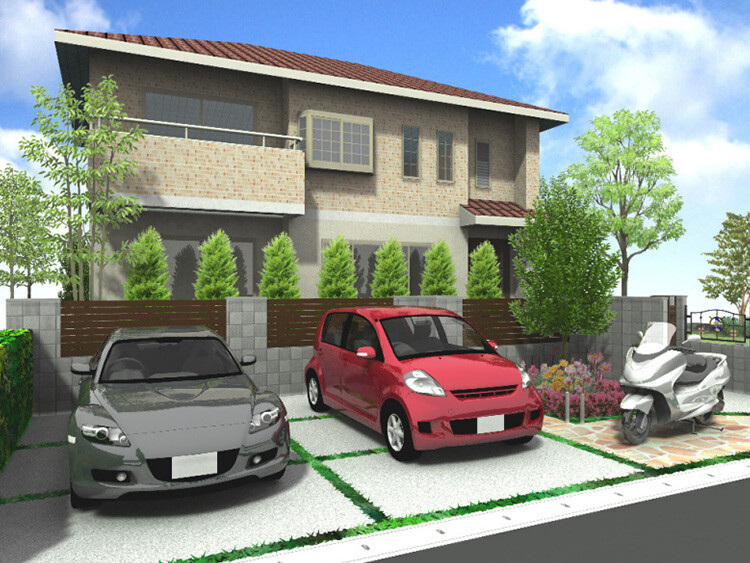
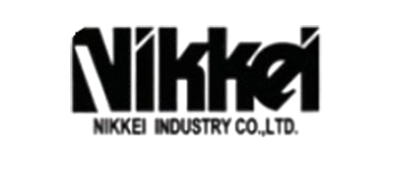
NIS Reduced File Size of Their CAD Design Software by 30%
NIS developed next-generation building exterior and garden design CAD software using 3D ACIS Modeler and HOOPS.
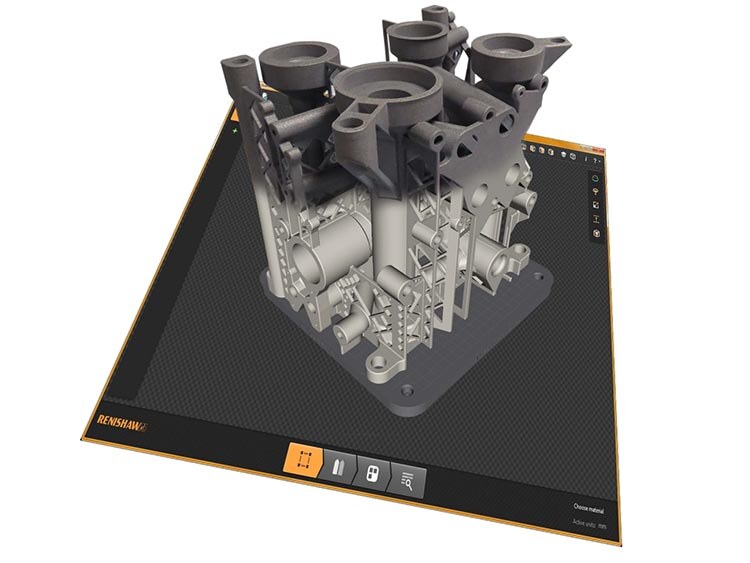
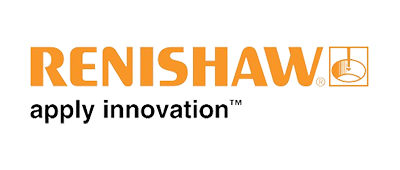
Renishaw Drastically Reduced the Need for STL File Healing
Renishaw integrated Spatial SDKs into QuantAM 2017, enabling users to build parts correctly the first time, preserving original design intent.
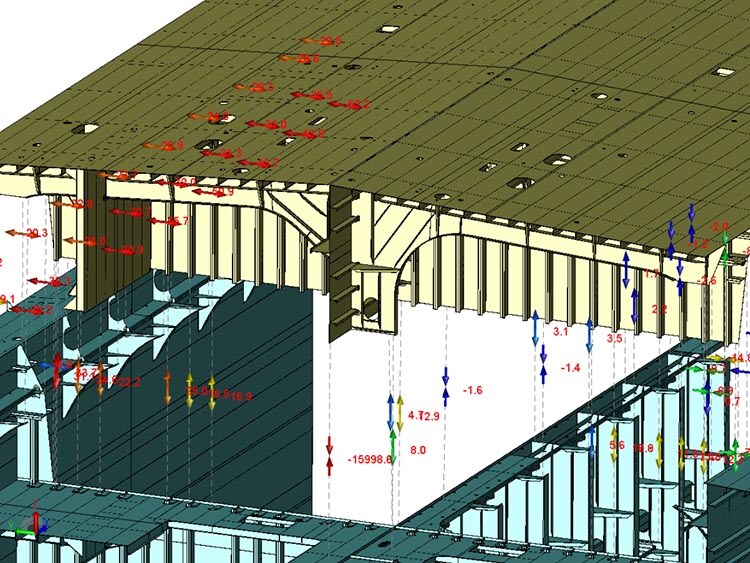
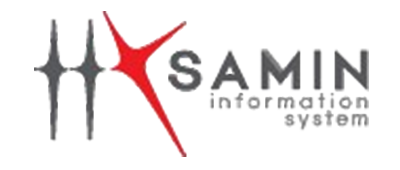
SAMIN Chose Spatial's ACIS 3D Kernel Instead of Parasolid
SAMIN became first to market in 2008 with a 3D accuracy control system that met the high standards of the Asian shipbuilding market using Spatial components.
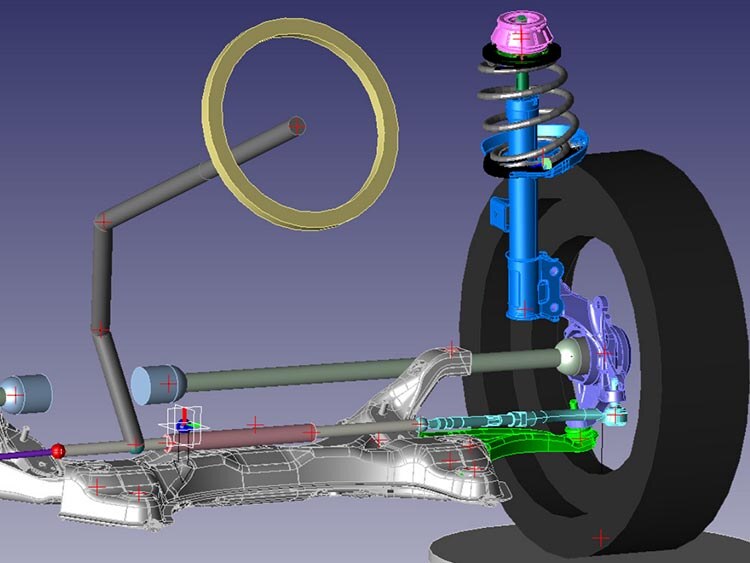
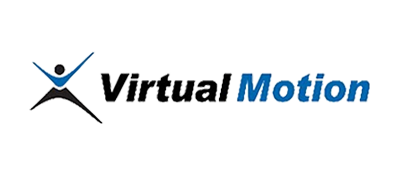
Virtual Motion Cut Development Time by 50%
Virtual Motion integrated the 3D ACIS modeling engine and leveraged AGM and HOOPS to accelerate DAFUL software development, bringing a new product to market quickly.
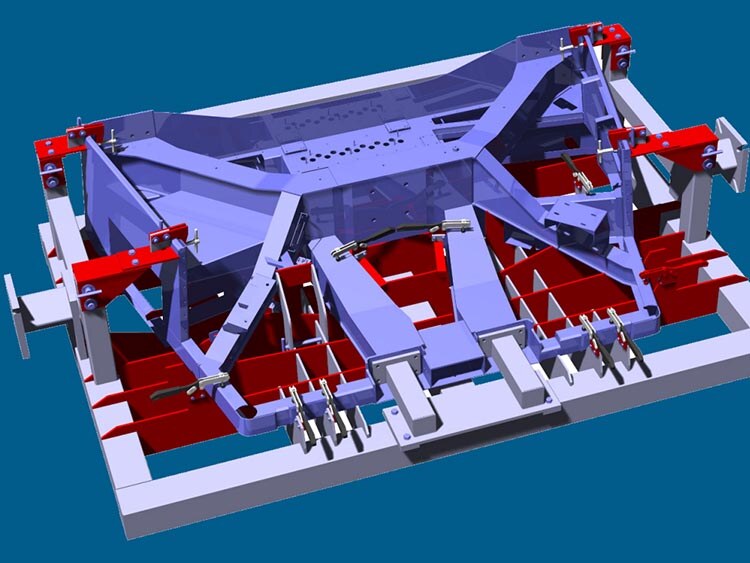
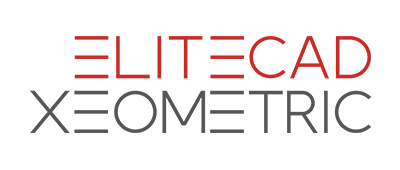
XEOMETRIC Accelerated Blending and Precise Hidden Line Removal
XEOMETRIC's 2D/3D construction planning and mechanical engineering software gained advanced functionality with 3D ACIS Modeler and 3D InterOp.
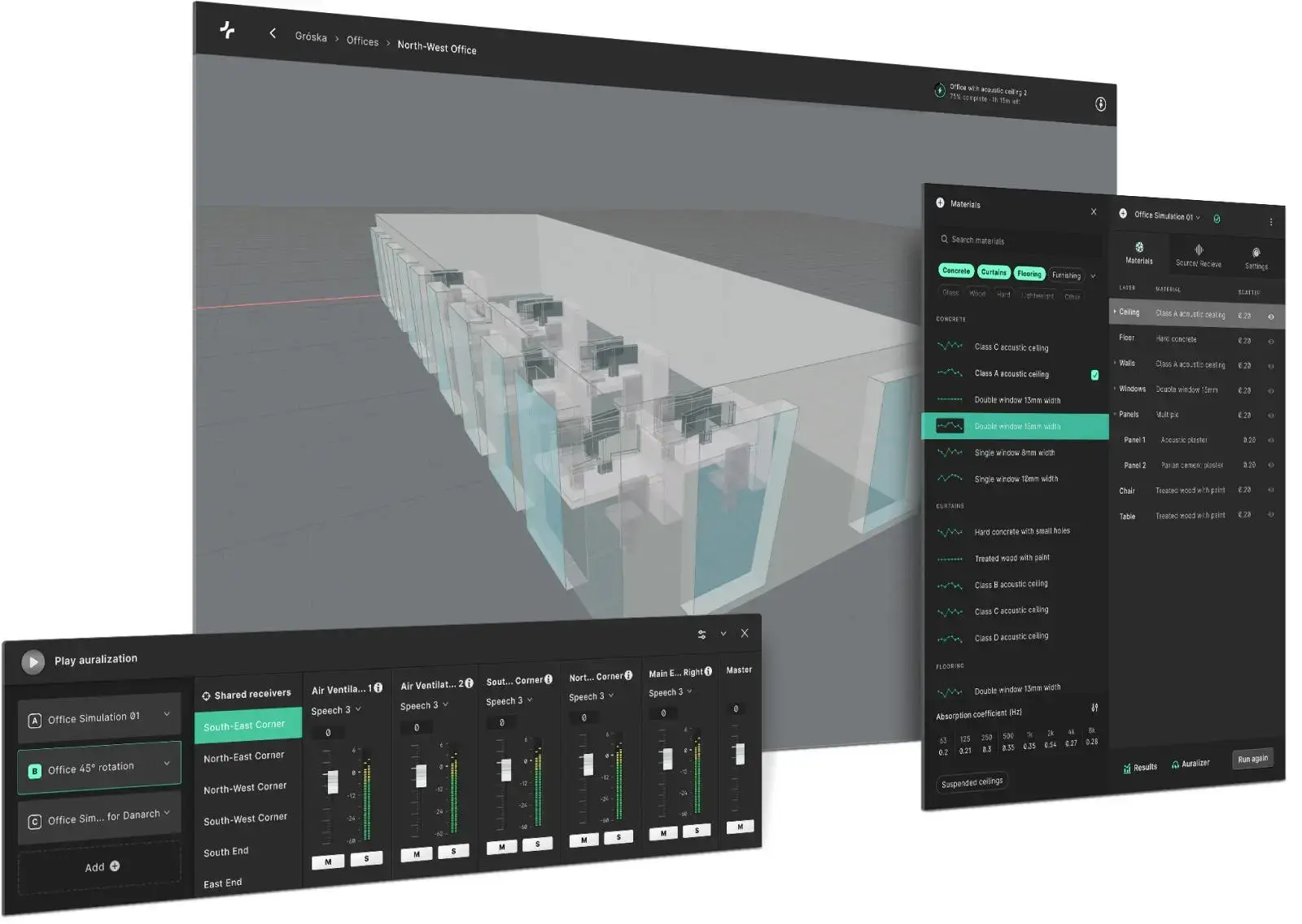
Treble Technologies Streamlines Simulation with Automatic 3D Meshing
Treble Technologies accelerated their simulation pipeline by integrating Spatial’s Meshing SDK, enabling faster, high-fidelity acoustic simulations at scale.