FVA Case Study
Market: Drive Technology
/logo-FVA-full-color.png)
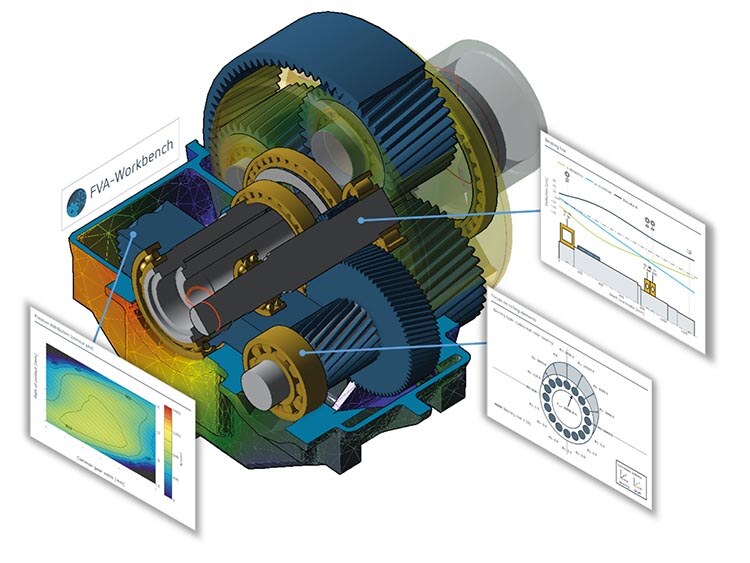
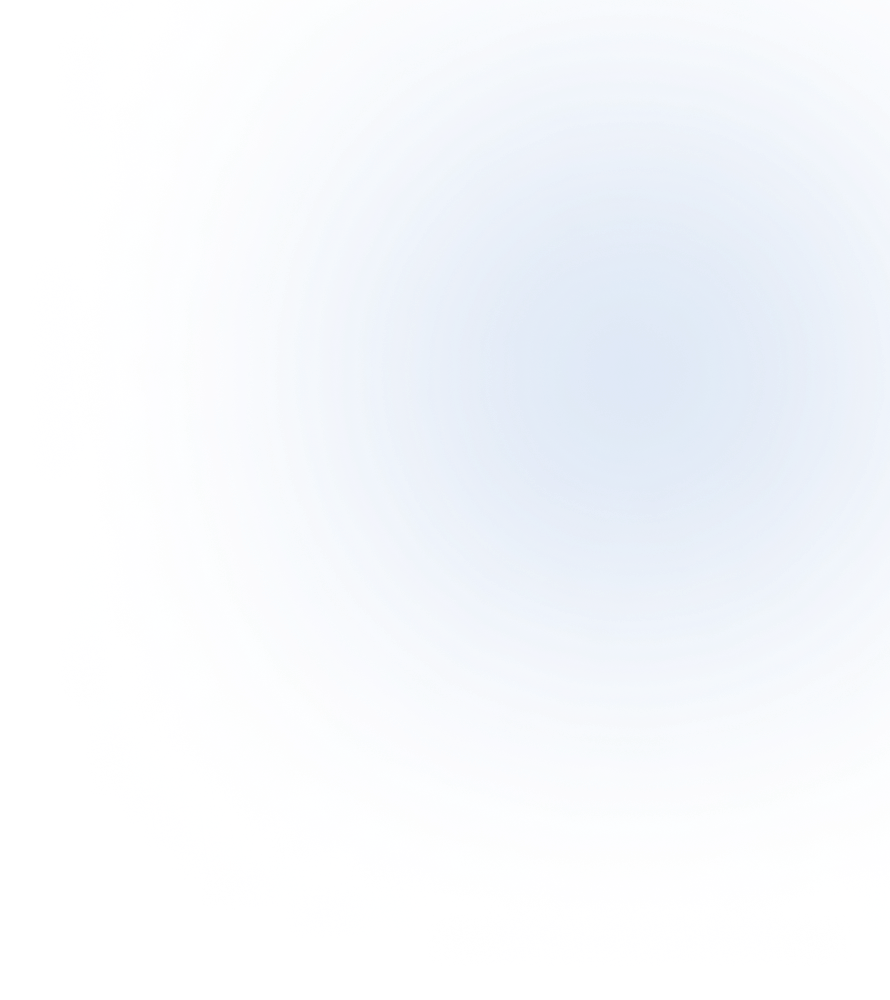
Summary
FVA GmbH develops analysis and simulation software for drive technology. They realized that to truly succeed in the marketplace, they needed to add more functionality to their solution, and this additional functionality depended on having accurate 3D modeling.
Spatial’s high quality 3D solutions allow FVA to model solid bodies with just a few lines of code, provide access to powerful Boolean operations, power fast meshing needed for FEA, and enable best-in-class CAD interoperability. By centering their solution around the ACIS 3D modeling kernel, FVA’s software solution gained access to a rich API to enable interaction with precise 3D models.
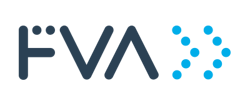
Working with Spatial enables our small and highly competent development team, staffed by the top experts from the industry, to focus on our core competenccy: numerical simulations. Thus, we are able to respond quickly to changes in the dynamic technology environment and new requirements from our customers.
The Company
Founded in 2010, FVA GmbH is a joint venture between FVA e.V. (Forschungsvereinigung Antriebstechnik, the Research Association for Drive Technology) and GzF (Gesellschaft zur Förderung des Maschinenbaues mbH, the Association for the Promotion of Mechanical Engineering) created to develop analysis and simulation software for drive technology, along with associated professional services and support.
FVA’s solutions serve the entire driveline industry (automotive, industrial, aviation, marine, rail, and wind) with software capable of highly sophisticated and detailed simulation of the system behavior of virtual gearboxes and detailed analysis of
individual driveline/gearbox components. Whether used in the early stages of design or to verify existing gearboxes, FVA’s software package enables customers to visualize complex gearboxes in 3D while modeling system behavior, such as deformations and kinematics.
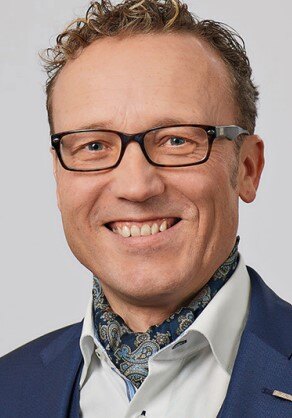
The Challenge
Adding More 3D Modeling Functionality for Analysis
An accurate representation of driveline system behavior is essential for detailed analysis of its performance, and the behavior of the system depends on accurate physical modeling of the components.
Initially, FVA chose the route of an in-house solution to generate a surface model of the individual components as opposed to modeling the solids geometrically. While this approach gave FVA total control over the modeling solution and proved initially successful, limitations to this approach soon became apparent:
- Inability to perform Boolean operations on driveline components — an essential function when modeling planetary gear systems and as a preparatory step prior to Meshing.
- Finite element analysis (FEA) was not possible as it requires generating a detailed mesh from a solid 3D model.
- Calculating mass or volume (for example, the volume of lubricant) of a driveline was difficult.
- Anytime a new routine was needed for working with the model, FVA needed to spend precious engineering time to create the new routine needed downstream for their analysis software.

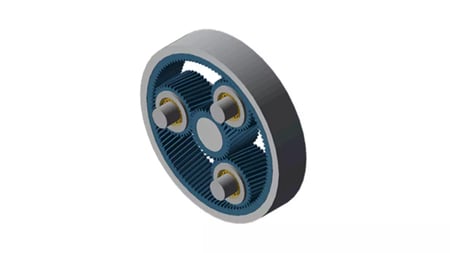
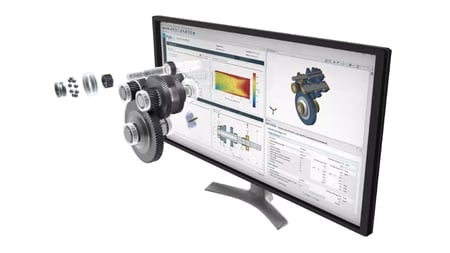
The Solution
As the limitations with the FVA’s in-house physical modeling solution became apparent, the company was faced with the classic make-versus-buy decision — should the company invest more time and resources into improving their own modeling solution, or look to an outside solution that would allow the company to focus on its core competencies.
FVA realized that to truly succeed in the marketplace, they needed to add more functionality to their solution, and this additional functionality depended on having accurate 3D modeling. With time to market also being a key concern, FVA decided to partner with Spatial and gain access to proven 3D modeling solutions with a 30 plus year track record.
By centering their solution around the ACIS 3D modeling kernel, FVA’s software solution gained access to a rich API to enable interaction with precise 3D models. Now FVA’s solution could easily perform complex Boolean operations needed for
analyzing planetary gearing systems or to determine the volume of oil in a transmission.
For over 30 years, 3D ACIS Modeler has led the 3D modeling kernel market, delivering flexible solutions that enable manufacturing, engineering, and design application providers to meet the demand for high-quality 3D applications in less time and with lower development costs.
FVA’s partnership with Spatial gave the company access to 3D InterOp — the gold standard for 3D CAD data translation. By integrating 3D InterOp into FVA-Workbench, users could now perform imports and exports to/from various native CAD formats with a single click.
Rather than spend time developing 3D visualization routines, FVA turned to HOOPS Visualize to create interactive 3D renderings to be used within the FVA-Workbench GUI and animations for reporting.
The decision to employ 3D Precise Mesh came only after an extensive analysis of available meshing solution, where the Spatial mesher came out on top regarding the quality of the results.

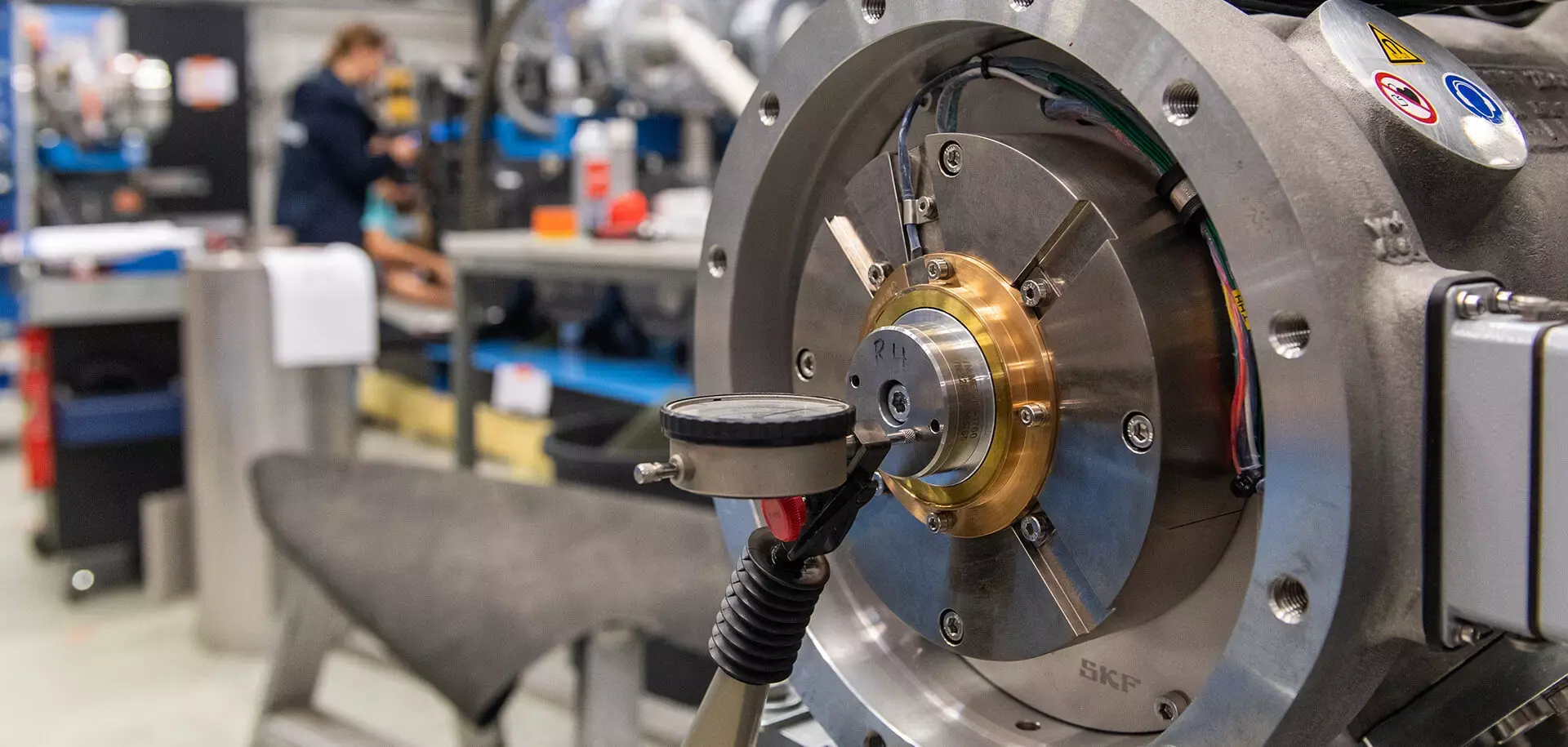
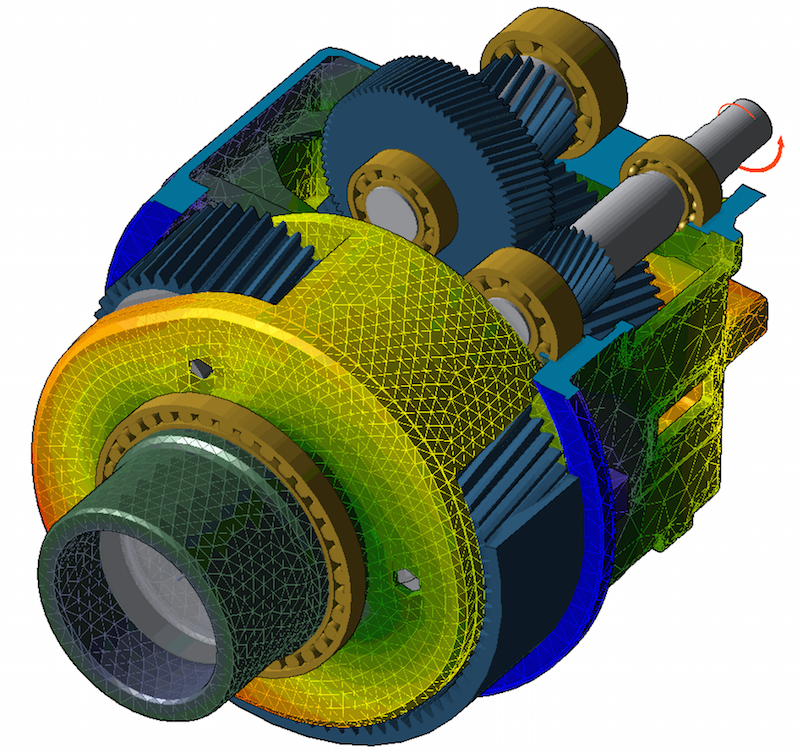
The Results
The result of this collaboration between the FVA and Spatial development teams has resulted in a feature-rich and robust driveline modeling and analysis package. With the move to Spatial SDKs, FVA has developed a user-friendly GUI for modeling even the most complex gearbox designs, supported by powerful 3D visualization capabilities:
-
The ACIS API allows FVA to model solid bodies with just a few lines of code, plus provide access to powerful Boolean operations.
-
3D Precise Mesh powers the fast meshing needed for FEA.
-
3D InterOp enables best-in-class CAD interoperability.
The result of this integration is that FVA’s customers can focus on gear analysis while the FVA-Workbench, enhanced with Spatial SDKs, takes care of the cumbersome and time-consuming geometry details. Analysis is now extended by the ability to generate FEM bodies, with all the necessary steps needed for detailed driveline analysis being performed from within the FVA-Workbench:
- Import of CAD geometries in various native formats
- Assembling of CAD bodies relative to the gearbox
- Modifications to CAD bodies
- Automatic geometry simplification and meshing of CAD bodies
- Semi-automatic setting of boundary conditions
- Enabling of fast and reliable combinations of analytical models with FEM
Key Insights
Solutions
In working with Spatial, FVA can now deliver high-performance software with powerful 3D visualization ahead of its competition. In turn, FVA’s customers are able to develop prototypes faster and more efficiently, while easily integrating FVA-Workbench into their workflow.Download the Full Case Study
Want to see a more detailed breakdown of how FVA put Spatial’s 3D solutions to work for their application? Download the full case study by clicking below.
Read More Spatial Case Studies
See how our industry-leading SDKs have helped countless businesses across several verticals. Browse
some of our other case studies below.
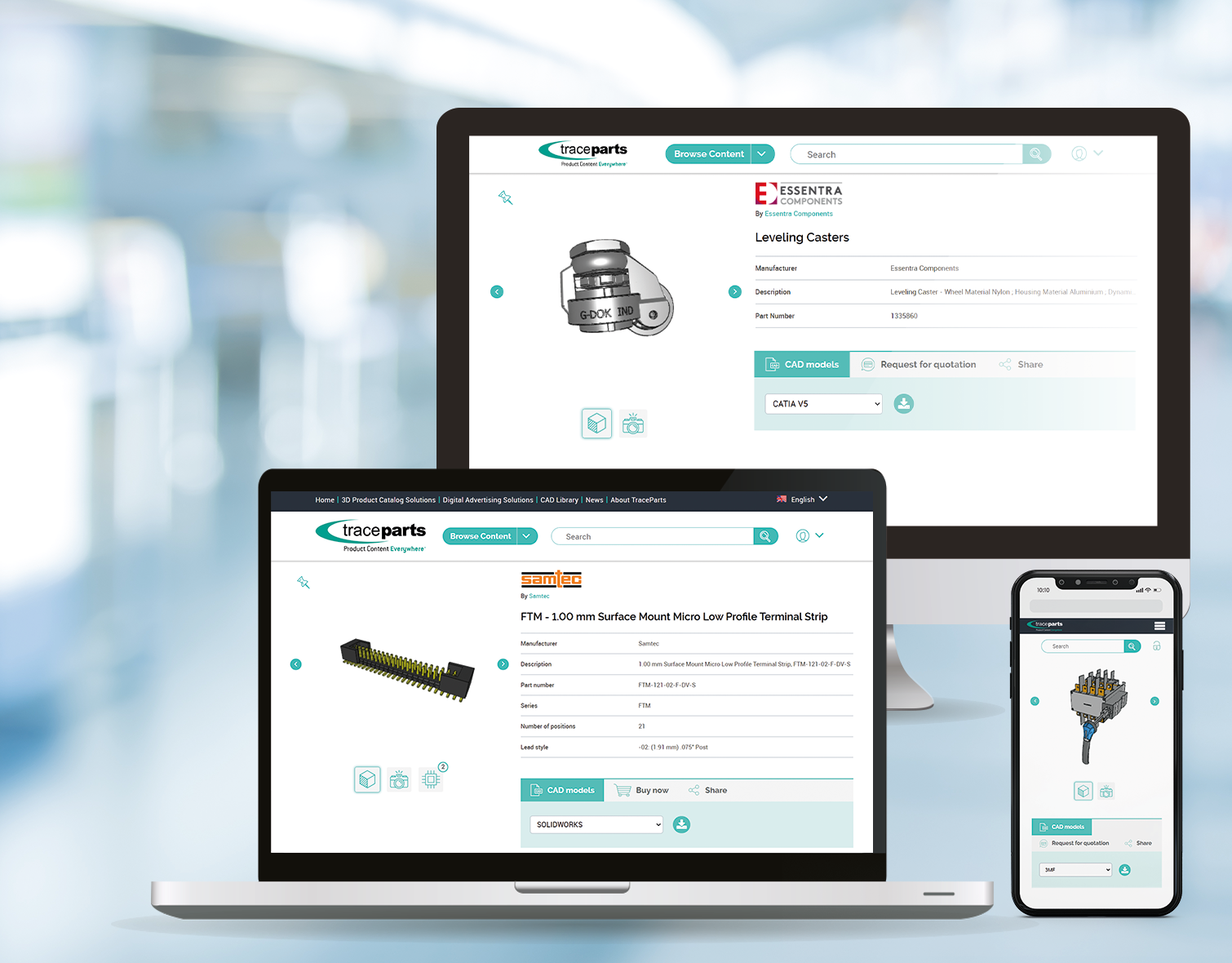
TraceParts enhances 3D Web Viewer Capabilities
TraceParts, a well-known CAD content supplier, integrates robust 3D visualization into their online 3D part viewer to enhance customer ordering experience.
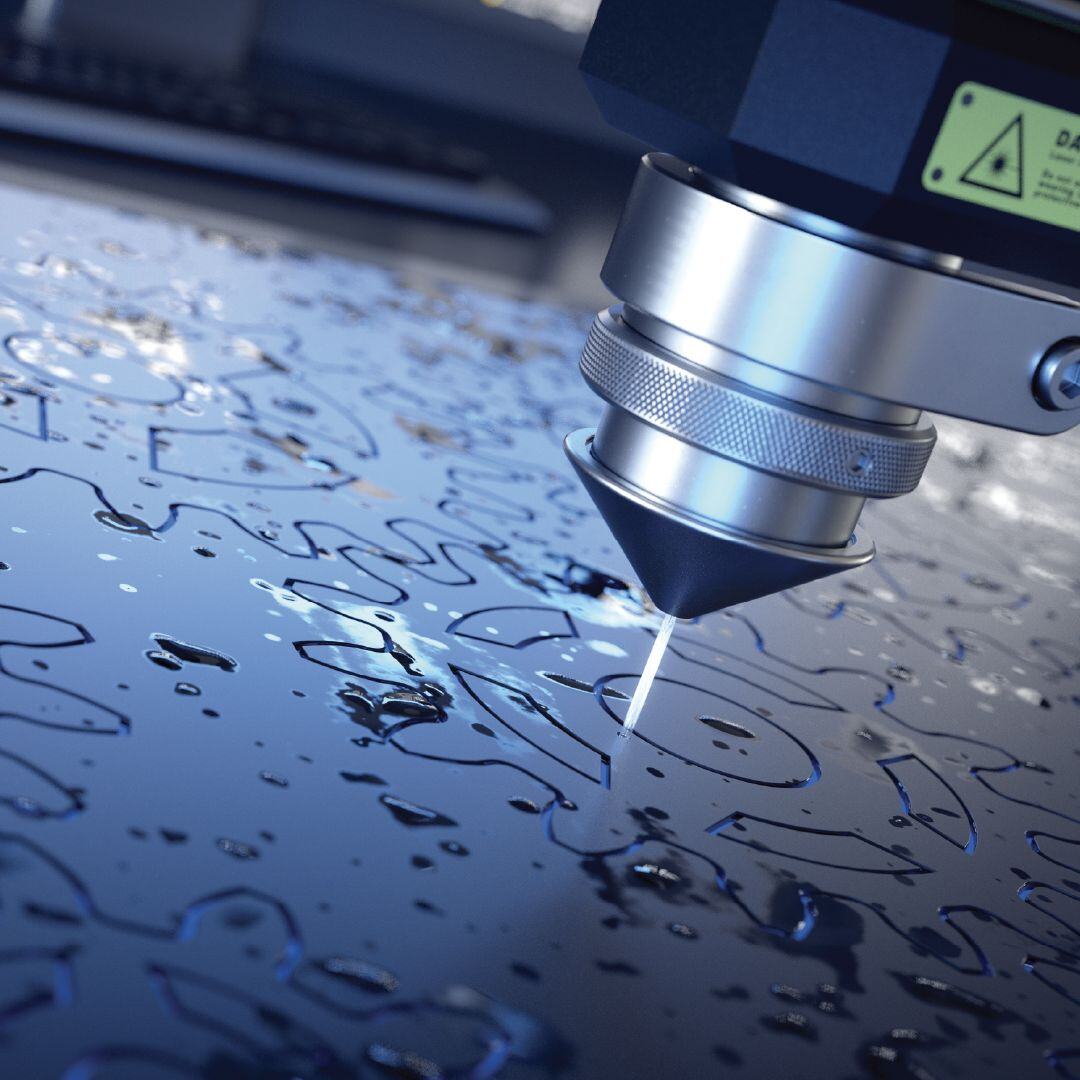

Prototek Released Advanced Digital Manufacturing Quoting
Prototek IQ, empowered by Spatial components allow instant quoting for 3D models. It saves customers’ time, alleviates administrative tasks, and opens new opportunities in digital manufacturing.
-1.png)
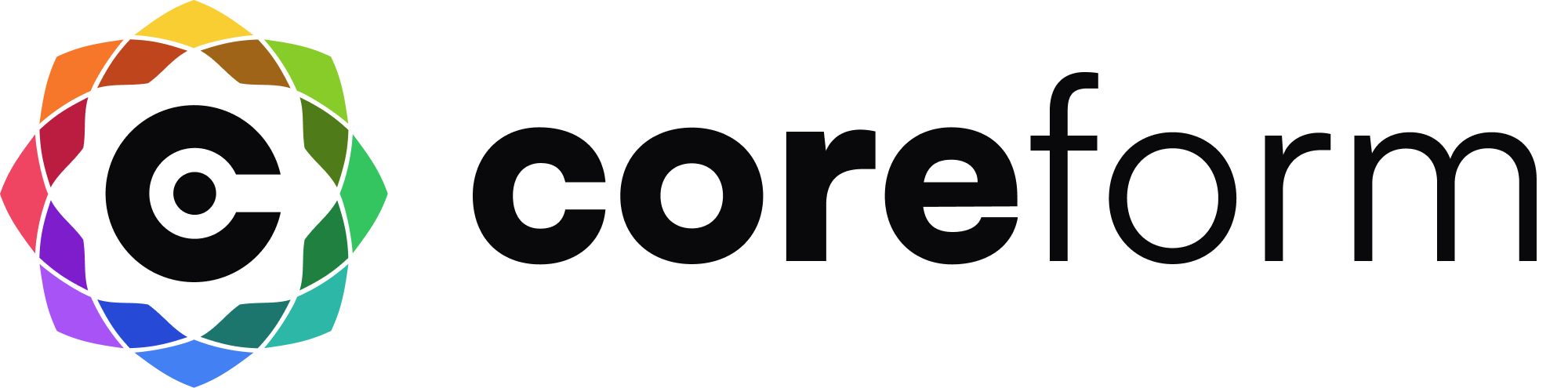
Coreform Brings Game-Changing Simulation Software To Life
Coreform was poised to make a real impact on the CAE world. By integrating specific Spatial SDKs customized to their needs, Coreform closed the circle on its revolutionary software.
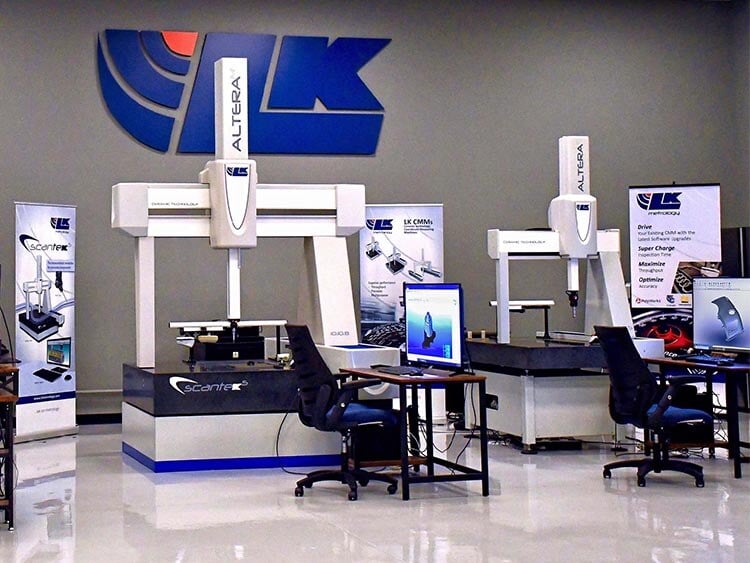
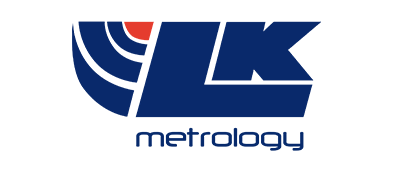
LK Metrology Future Proofed their Application
LK Metrology was on a quest to maintain precision for their Coordinate Measuring Machines. They improved core application functionality through a development partnership with Spatial.
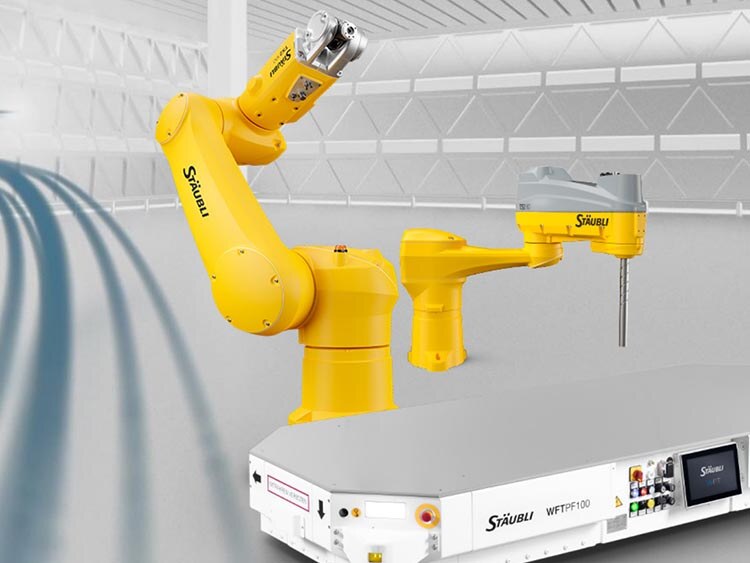
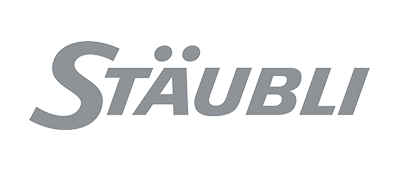
Stäubli Elevated Their Offerings and Capabilities with Spatial's SDKs
Stäubli Robotics Suite 2022 offered optimized features for complex automation scenarios, enabled by Spatial’s CGM Modeler.
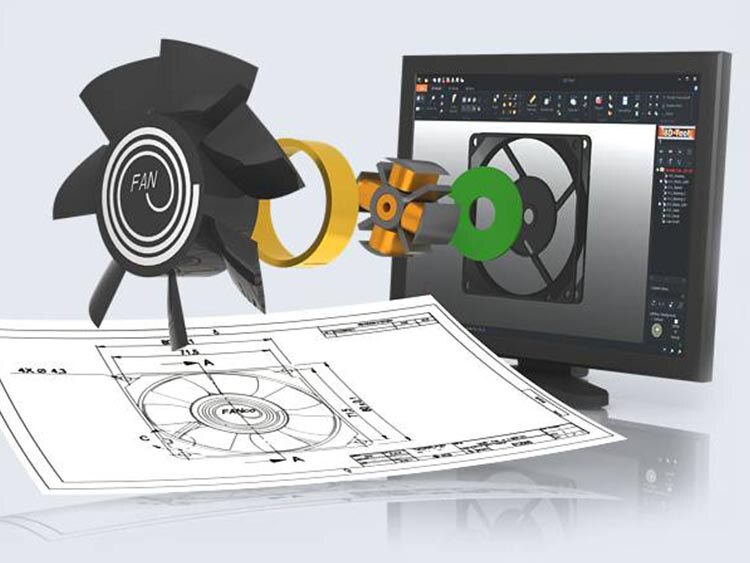
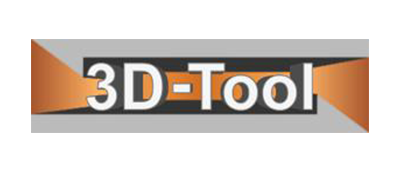
3D-Tool Maximized Customer License Upgrades
3D-Tool expanded Viewer functionality to native CAD formats like CATIA V5 and Pro/E, enabling users to view and translate native CAD files without costly conversion.
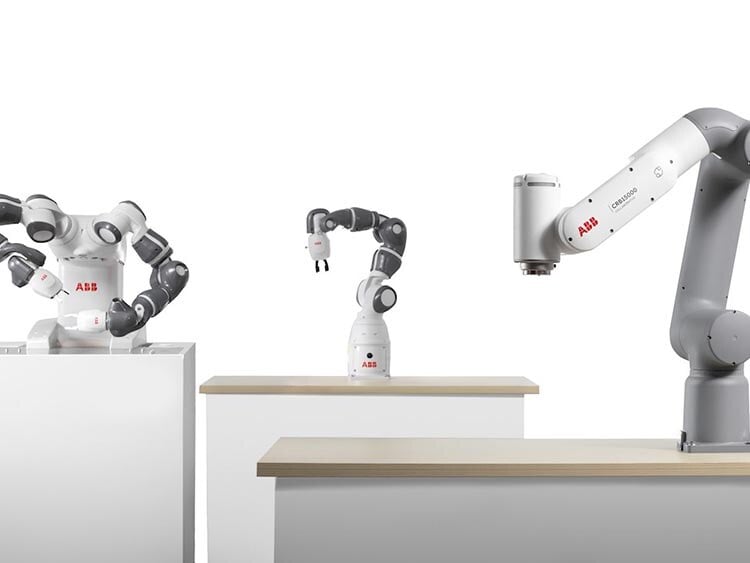
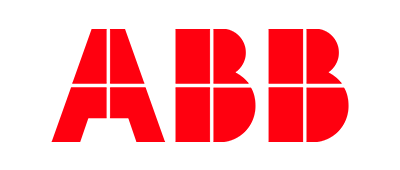
ABB's Programming Without Shutting Down Production
ABB’s Robotics Division used RobotStudio software for PC-based robot programming, boosting productivity without production shutdowns.
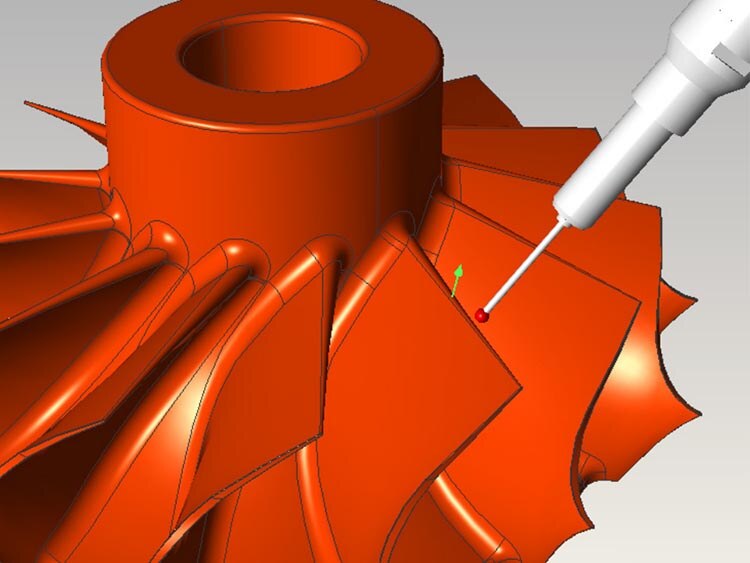
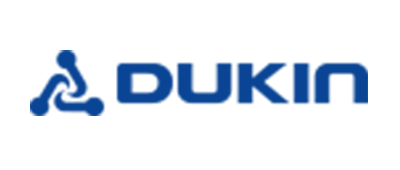
Dukin Co Slashed Development Costs by 50%
Dukin used 3D ACIS Modeler to focus on core technology, reducing time spent on solid modeling and accelerating new product development.
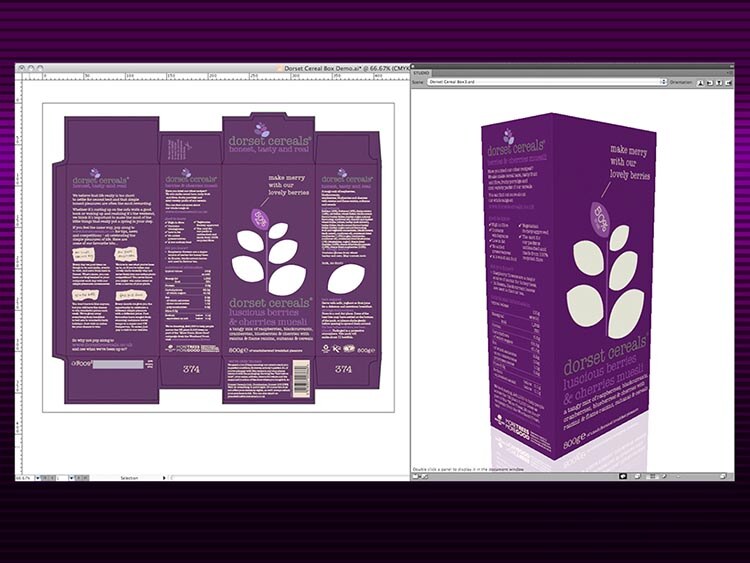
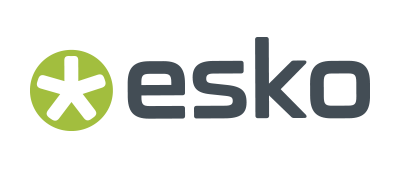
EskoArtwork Drastically Reduced Preparation of CAD Models for Downstream Use
EskoArtwork's ArtiosCAD gained 3D CAD model import functionality, maintaining competitive edge without straining in-house resources.
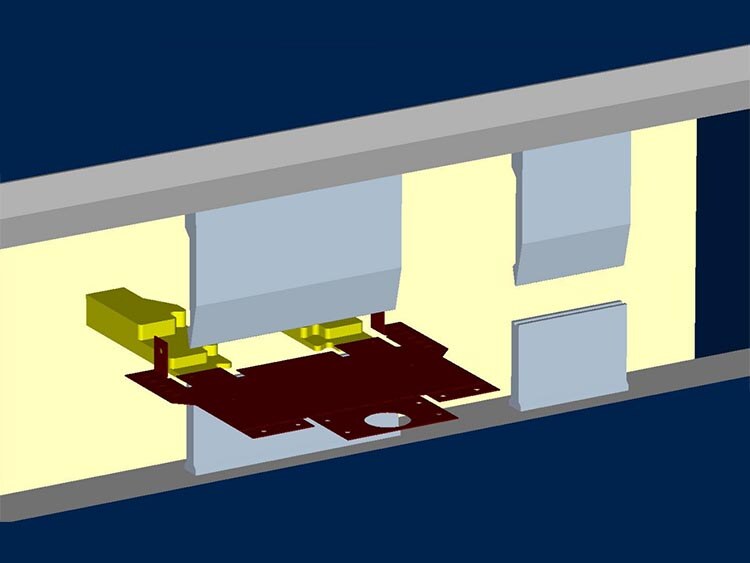
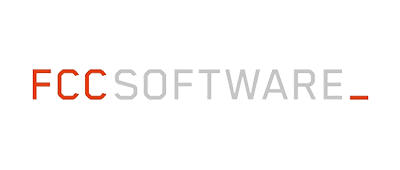
FCC Increased Production Time by 20x
A leading CAM software provider for sheet metal manufacturing used 3D ACIS Modeler for robust 3D modeling and simulation.
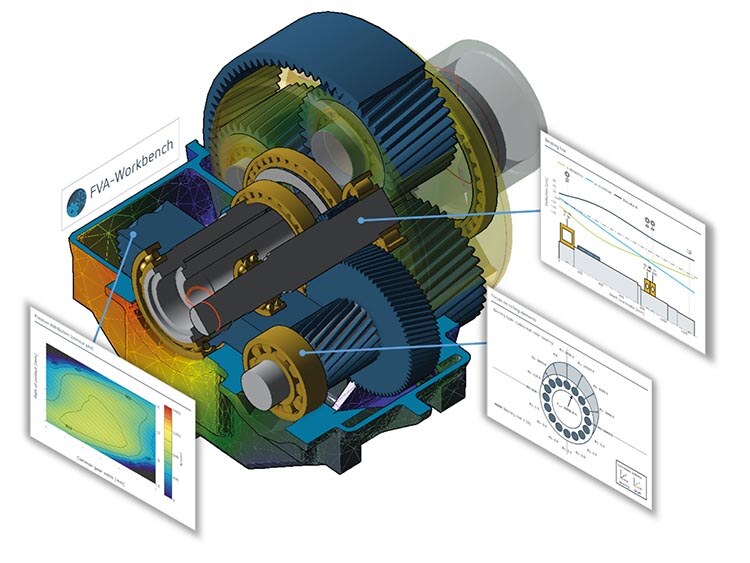
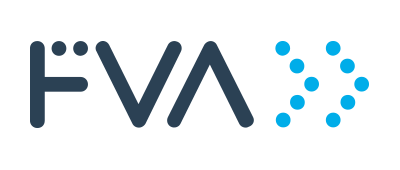
FVA Accelerated Support for New and Updated CAD Formats
FVA's solutions served the driveline industry with software capable of sophisticated simulations and detailed analyses of gearbox components.
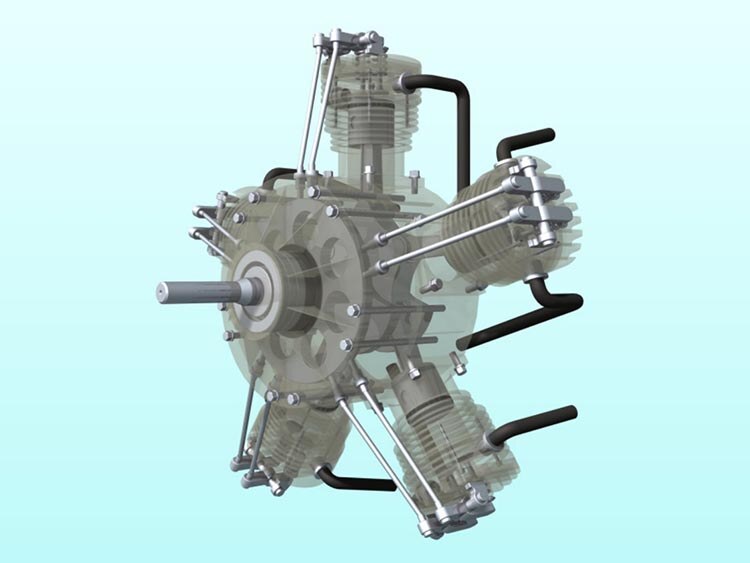
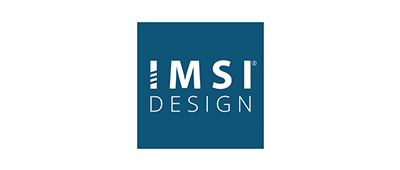
IMSI Accelerated Time-to-Market for New Features
IMSI/Design integrated new versions of ACIS quickly, bringing a new version of TurboCAD to market every 12-15 months.
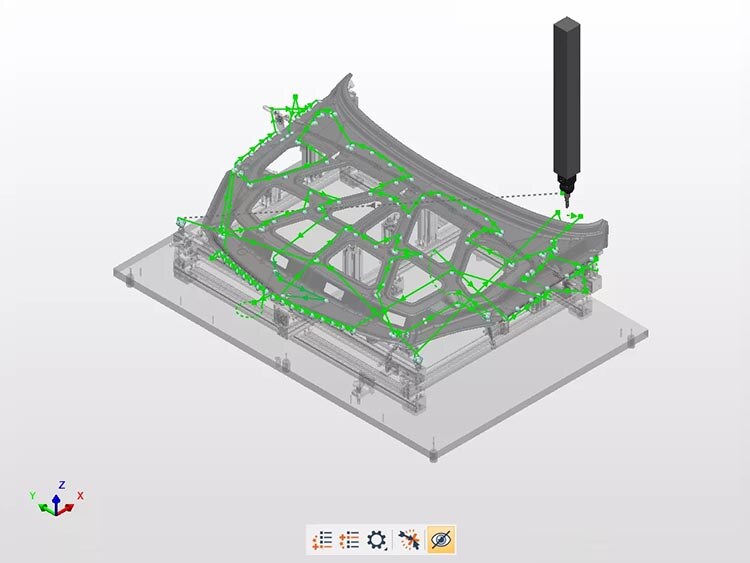
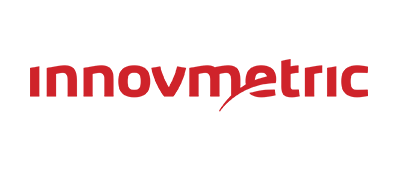
InnovMetric Eliminated Nearly 100% of Their Translation Errors
InnovMetric provided their automotive and aerospace customers with top CAD translators in PolyWorks® by selecting Spatial InterOp software.
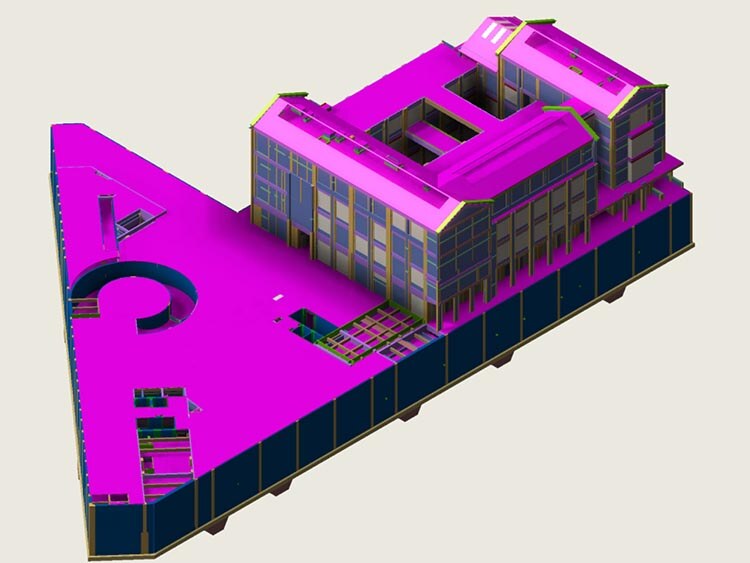
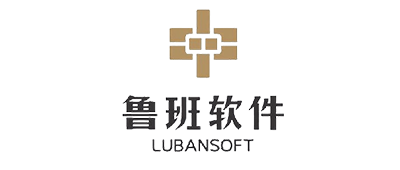
Lubansoft Boosted Design Quality and Reduced Costly Errors
Lubansoft boosted design quality and reduced errors in their BIM software by using 3D ACIS Modeler and HOOPS Visualize.
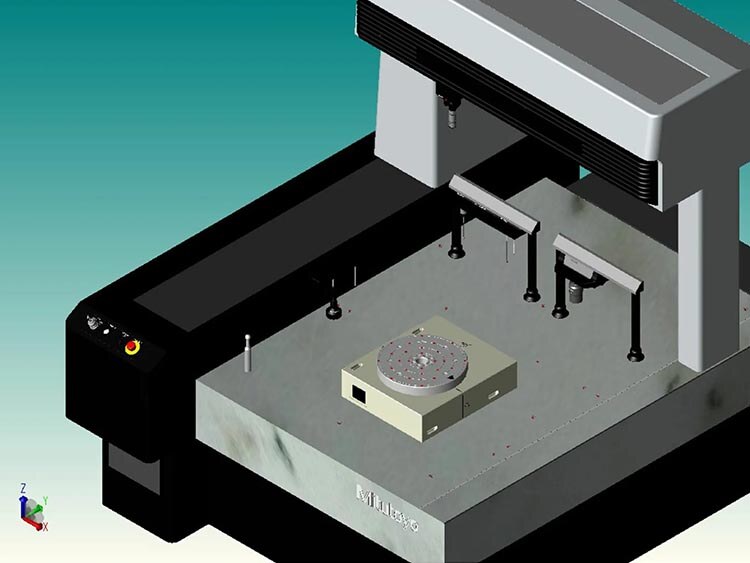
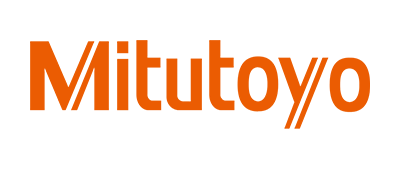
Mitutoyo Supercharged Their 3D Interop Translation
Mitutoyo broadened the use of Spatial technology to other parts of the organization, such as machine configuration.
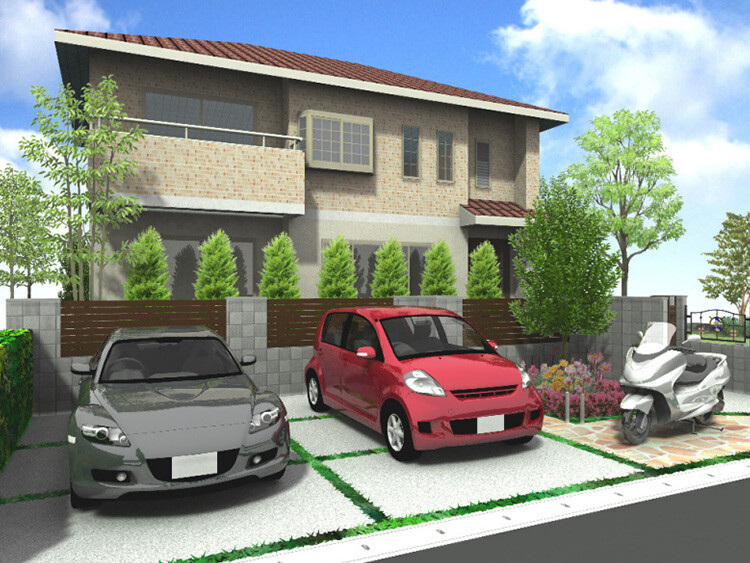
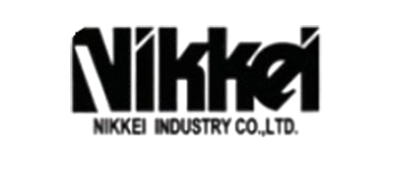
NIS Reduced File Size of Their CAD Design Software by 30%
NIS developed next-generation building exterior and garden design CAD software using 3D ACIS Modeler and HOOPS.
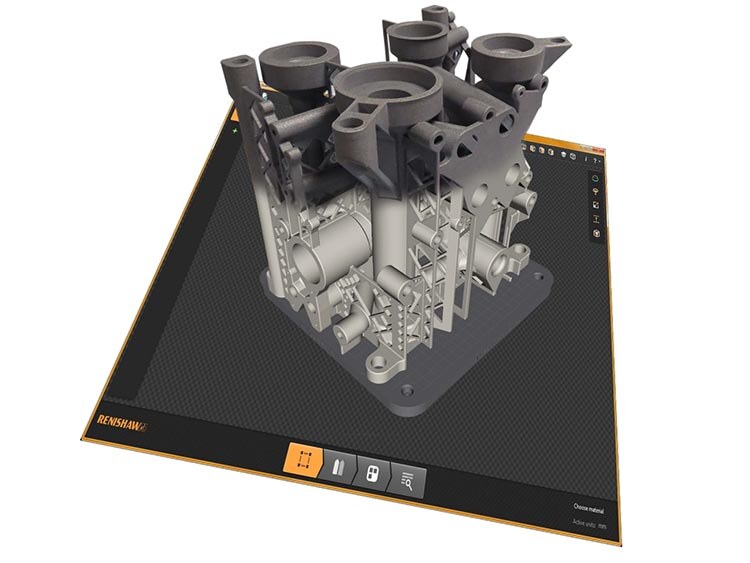
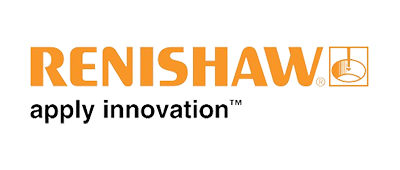
Renishaw Drastically Reduced the Need for STL File Healing
Renishaw integrated Spatial SDKs into QuantAM 2017, enabling users to build parts correctly the first time, preserving original design intent.
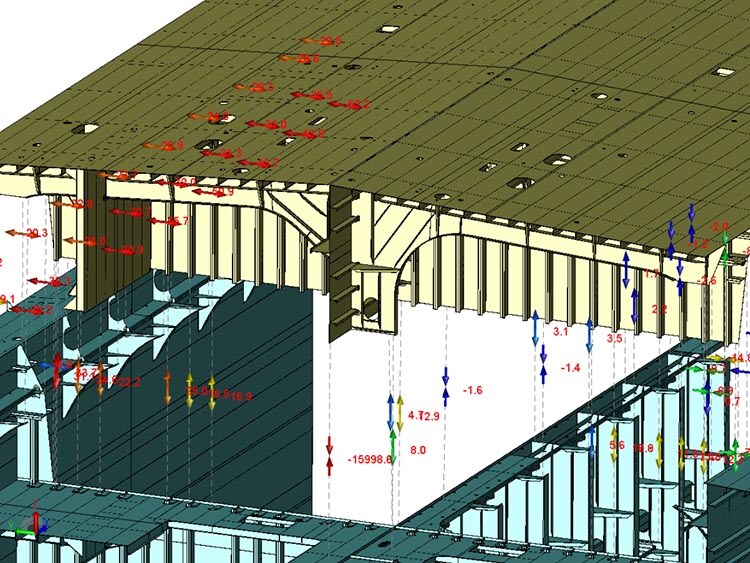
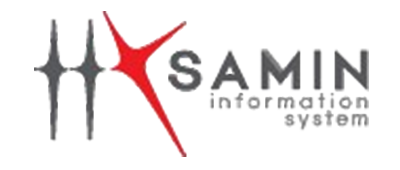
SAMIN Chose Spatial's ACIS 3D Kernel Instead of Parasolid
SAMIN became first to market in 2008 with a 3D accuracy control system that met the high standards of the Asian shipbuilding market using Spatial components.
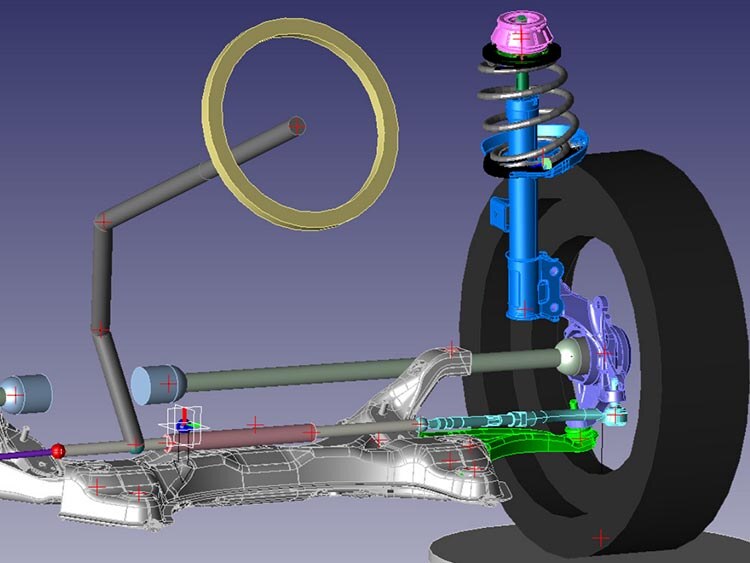
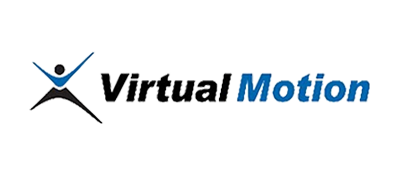
Virtual Motion Cut Development Time by 50%
Virtual Motion integrated the 3D ACIS modeling engine and leveraged AGM and HOOPS to accelerate DAFUL software development, bringing a new product to market quickly.
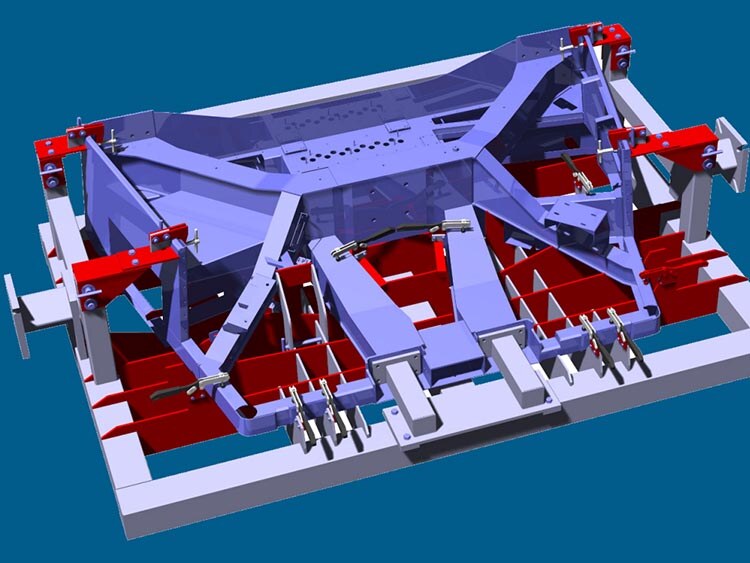
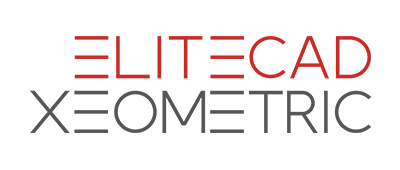
XEOMETRIC Accelerated Blending and Precise Hidden Line Removal
XEOMETRIC's 2D/3D construction planning and mechanical engineering software gained advanced functionality with 3D ACIS Modeler and 3D InterOp.
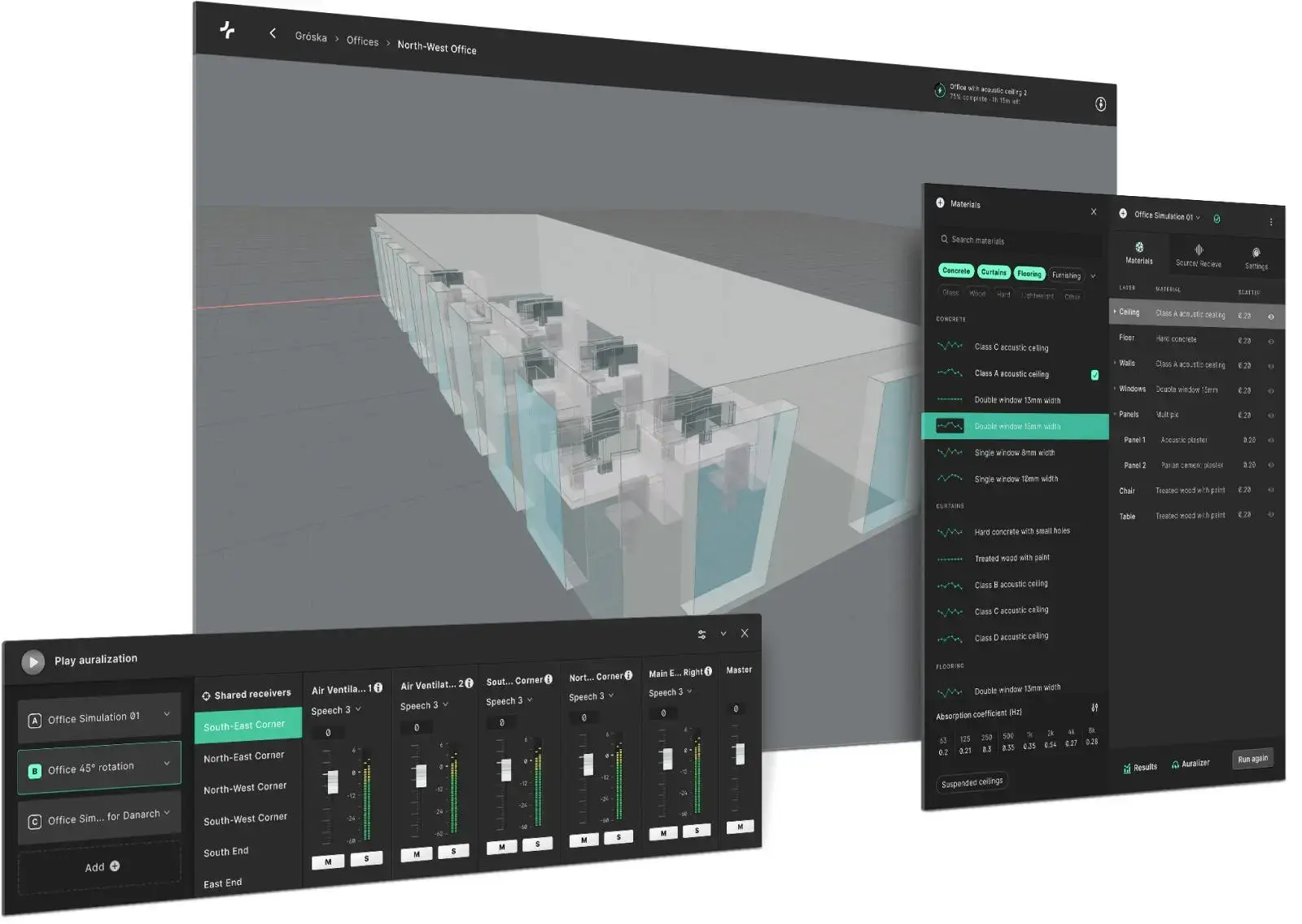
Treble Technologies Streamlines Simulation with Automatic 3D Meshing
Treble Technologies accelerated their simulation pipeline by integrating Spatial’s Meshing SDK, enabling faster, high-fidelity acoustic simulations at scale.