Renishaw Case Study
Market: Automated Manufacturing
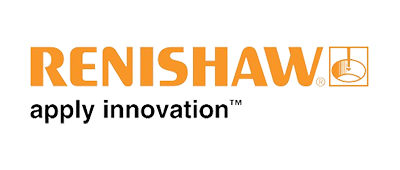
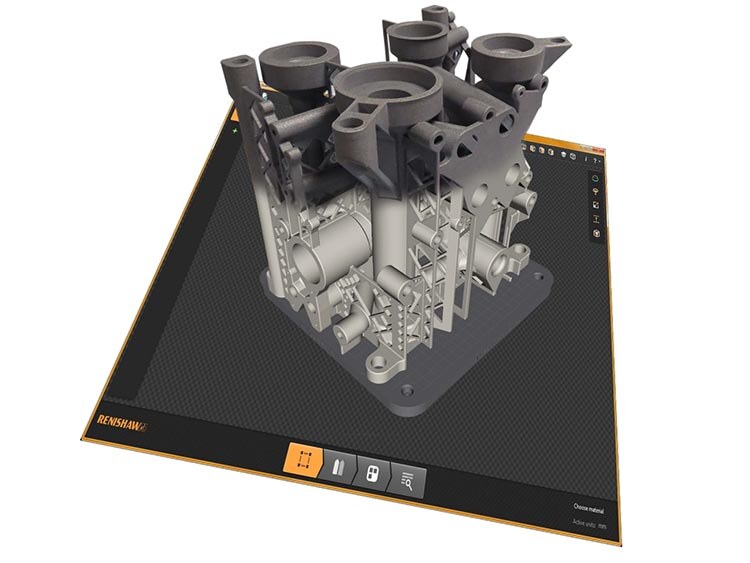
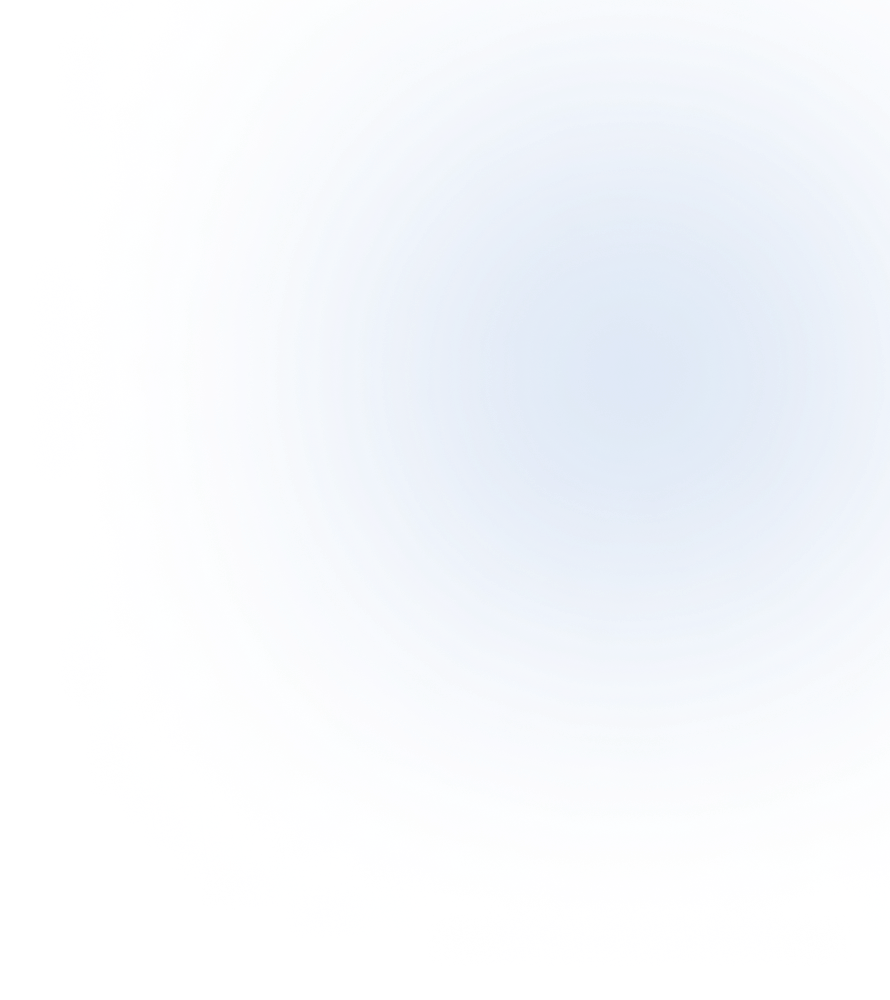
Summary
Renishaw, is a world leading engineering and scientific technology company supplying industrial automation and process control solutions and services . Renishaw wanted to move away from an STL-centric file import process and its limitations while minimizing engineering effort.
Renishaw’s move to Spatial’s 3D ACIS Modeler offered world-class healing, advanced modeling, and a quantum leap in editing capabilities. Spatial’s high quality SDKs allowed Renishaw to pave the way to future CAD functionality.
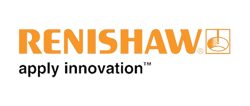
Our collaboration with Spatial now allows us to not only perform high-quality healing on STL files but, more importantly, to import various CAD formats directly.
The Company
Renishaw is an established world leader in engineering technologies, with a strong history of innovation in product development and manufacturing. Today, this history of innovation extends to the design, development and production of advanced metal additive manufacturing systems for direct manufacturing of 3D-printed metallic components.
Prior to 3D printing, it is necessary to generate the printer’s laser scan paths that fuse the powder layers to each other to additively form a part. Build preparation software is thus key to generating the high-quality part builds. To maximize build quality on its own printers and to provide its industrial customers with a simple UI in which to orient, support and set build parameters, Renishaw has developed its own build preparation tool – QuantAM.
QuantAM is designed specifically for Renishaw AM platforms, providing tight integration to the machine control software and the ability to accurately and rapidly review all build files prior to production.
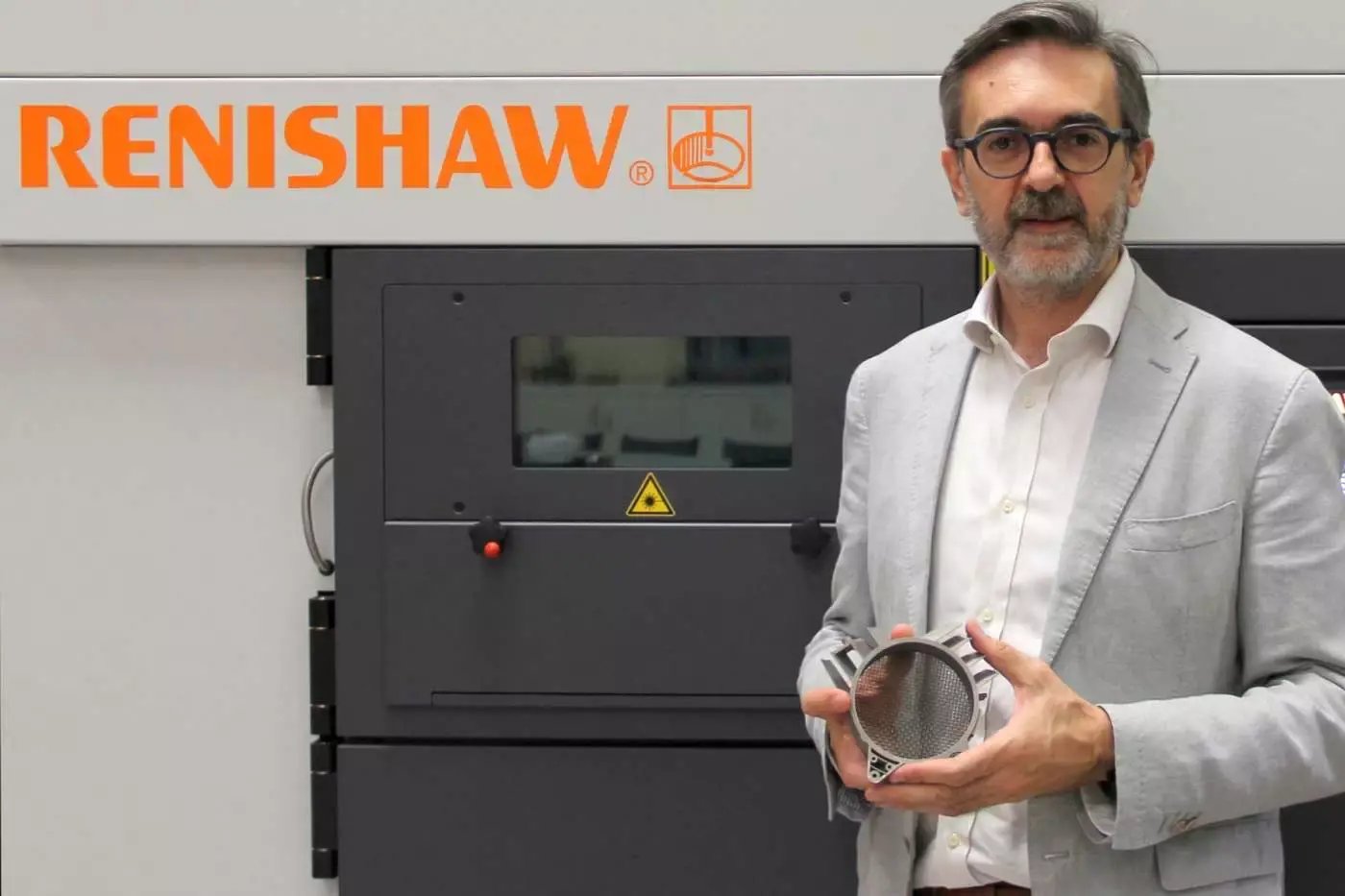
The Challenge
Move Away from STL-Centric File Import
Digitally driven additive manufacturing systems require a file preparation stage to take the original CAD geometry and format it into a machine-readable build file. The most common CAD export format is stereolithography (STL). The STL format describes a surface as a collection of connected triangles — the more complex a surface is, the larger number of triangles that are needed to define that surface.
While STL import has served the industry well, there are several limitations with this format:
- Regardless of the number of triangles used to describe a surface, it is still an approximation, for example, a sphere described as a collection of triangles can only approach the accuracy of a parameterized model of a sphere (and never achieve the simplicity of the description).
- If the wrong triangle density is chosen at the time of export, it can have an impact on the resulting print quality. An end user has to have a good understanding of what the print resolution of the equipment is.
- Because an STL representation is an approximation, it both limits and complicates the ability to edit the model.
- Errors in translating the intent of the model, with any fixes being manual and less than perfect.
- A fixed/repaired model diverges from the original, complicating keeping specifications in sync.
- No support for product and manufacturing information (PMI).
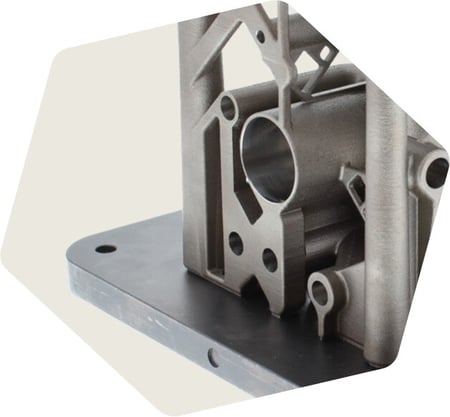
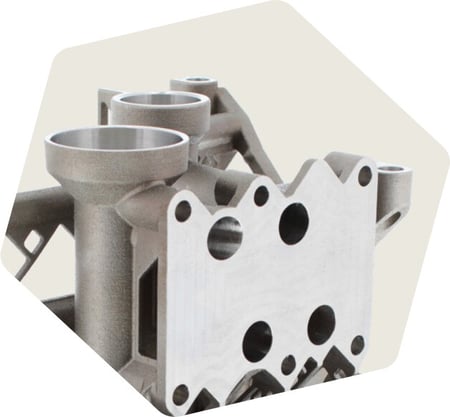
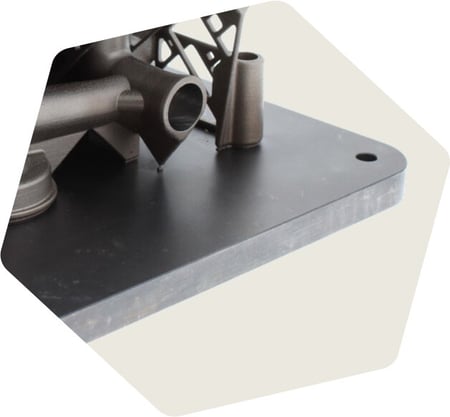
The Solution
Robust and Native Modeling Kernel
New for QuantAM 2017, Renishaw’s software engineering group architected a major overhaul to their current platform.
With the help of Spatial’s technical team, Renishaw have integrated two key components into
QuantAM: the 3D ACIS Modeler with CGM Polyhedra and 3D InterOp.
Moving to the ACIS Modeling Kernel
A major change to the QuantAM solution was to move to the ACIS modeling kernel and away from the reliance solely on an STL representation of the model. This move to a native modeling kernel delivers significant advantages to both Renishaw and their customers.
World-Class Healing
3D ACIS Modeler provides access to a powerful set of functions and routines that can handle these tough modeling problems of stitching, geometry simplification and gap tightening. The 3D ACIS Modeler add-on, CGM Polyhedra, provides QuantAM access to robust and powerful polygonal healing capabilities on tessellated data — an important capability because STL imported data is often imperfect, obscuring the intent of the model.
Advanced Modeling
By using CGM Polyhedra and the 3D ACIS Modeler, QuantAM now benefits from precise B-rep and polyhedral hybrid modeling capabilities. For example, CGM Polyhedra can recognize canonic surfaces, such as planes, cylinders, cones, toroids, and spheres in an STL model, converting these structures to precise representations, and thus preserving the intent of the original model.
Quantum Leap in Editing Capabilities
Because the imported data now exists as a true 3D hybrid model, geometric modifications, edits and corrections can be made to the hybrid model. This updated model can be fed back upstream to the original design team, enabling them to review any changes made to make the part manufacturable. This new flow made possible by the 3D ACIS Modeler enables model-based engineering, where the model is the specification, allowing for any changes made in manufacturing to be fed back to the entire system.
Integrating 3D InterOp
With 3D InterOp, QuantAM can now import many new modeling formats, enabling Renishaw to support additional customers and workflows, including all major CAD providers and associated formats. By adding support for the native formats of other CAD systems, QuantAM can import the original design intent, bringing in not only the geometry data, but also the product structure and assembly, graphical representation, and PMI.
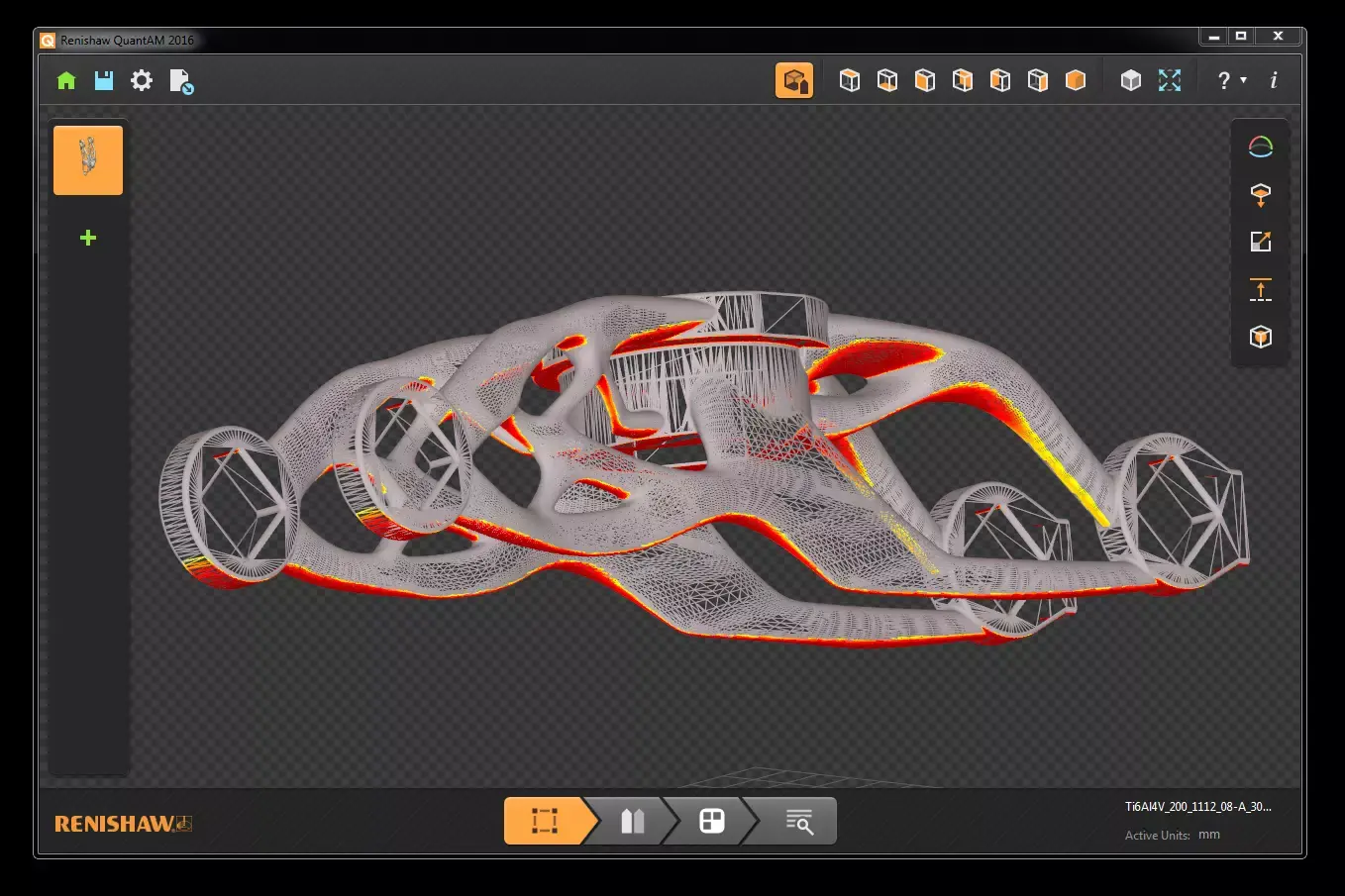
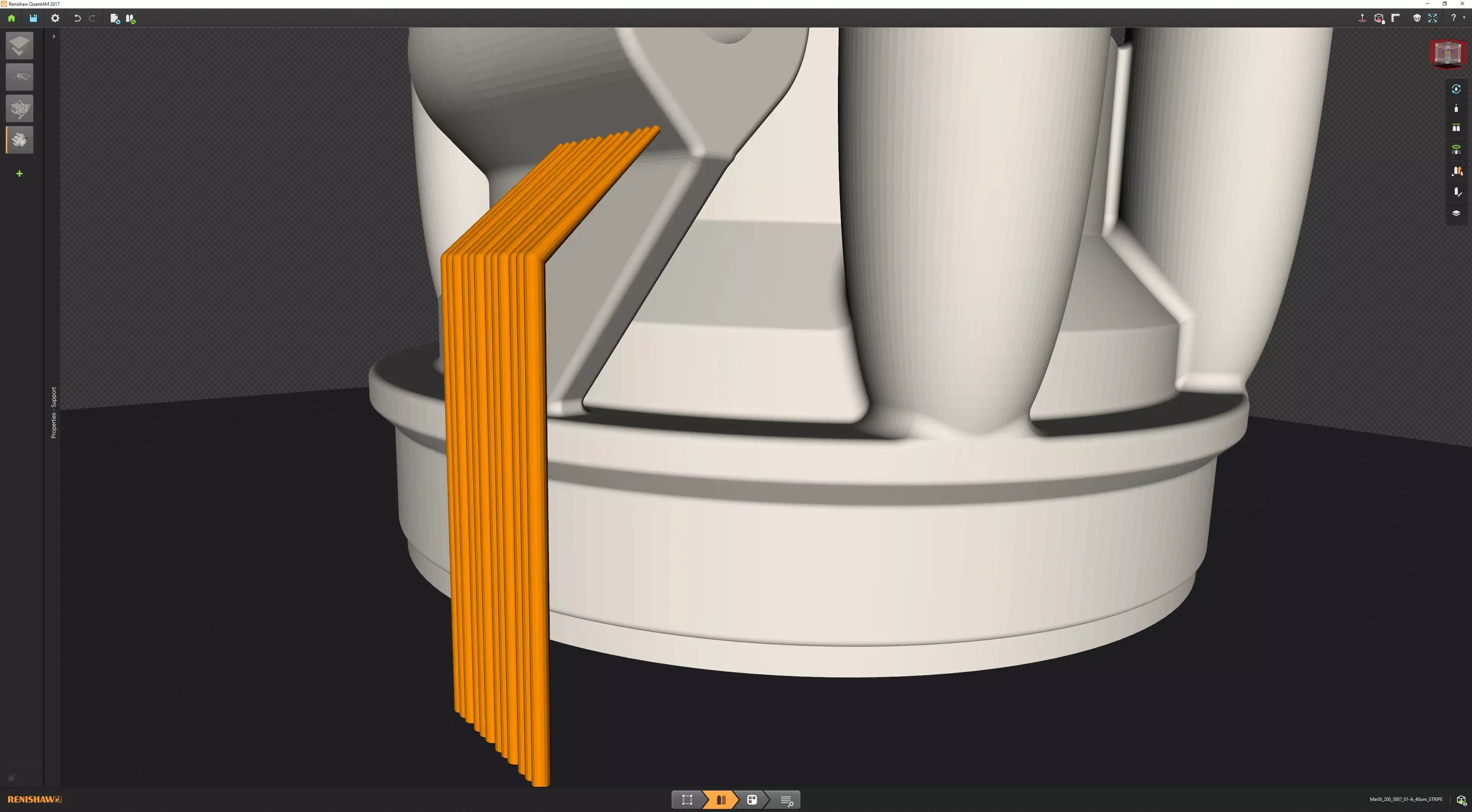

The Results
From a business perspective, collaborating with Spatial provides Renishaw with a complementary set of capabilities and highlights the benefits of this long standing, productive working relationship. From an engineering perspective, Renishaw gains a robust solution tested on thousands of datasets from hundreds of customers. The team benefits from the Spatial engineering team’s years of experience in dealing with 3D modeling as well as translating CAD databases from various vendors while preserving design intent.
As a result, the team does not have to deal with the usual issues when rolling out new code to customers. Moreover, due to the maturity and robustness of the solution set, the number of support issues is greatly reduced. Renishaw’s customers benefit from any code fixes and improvements needed by the Spatial community.
Key Insights
Solutions
As a result, the team does not have to deal with the usual issues when rolling out new code to customers. Moreover, due to the maturity and robustness of the solution set, the number of support issues is greatly reduced. Renishaw’s customers benefit from any code fixes and improvements needed by the Spatial community.
Download the Full Case Study
Want to see a more detailed breakdown of how Renishaw integrated Spatial’s SDKs into their application? Download the full case study by clicking below.
Read More Spatial Case Studies
See how our industry-leading SDKs have helped countless businesses across several verticals. Browse
some of our other case studies below.
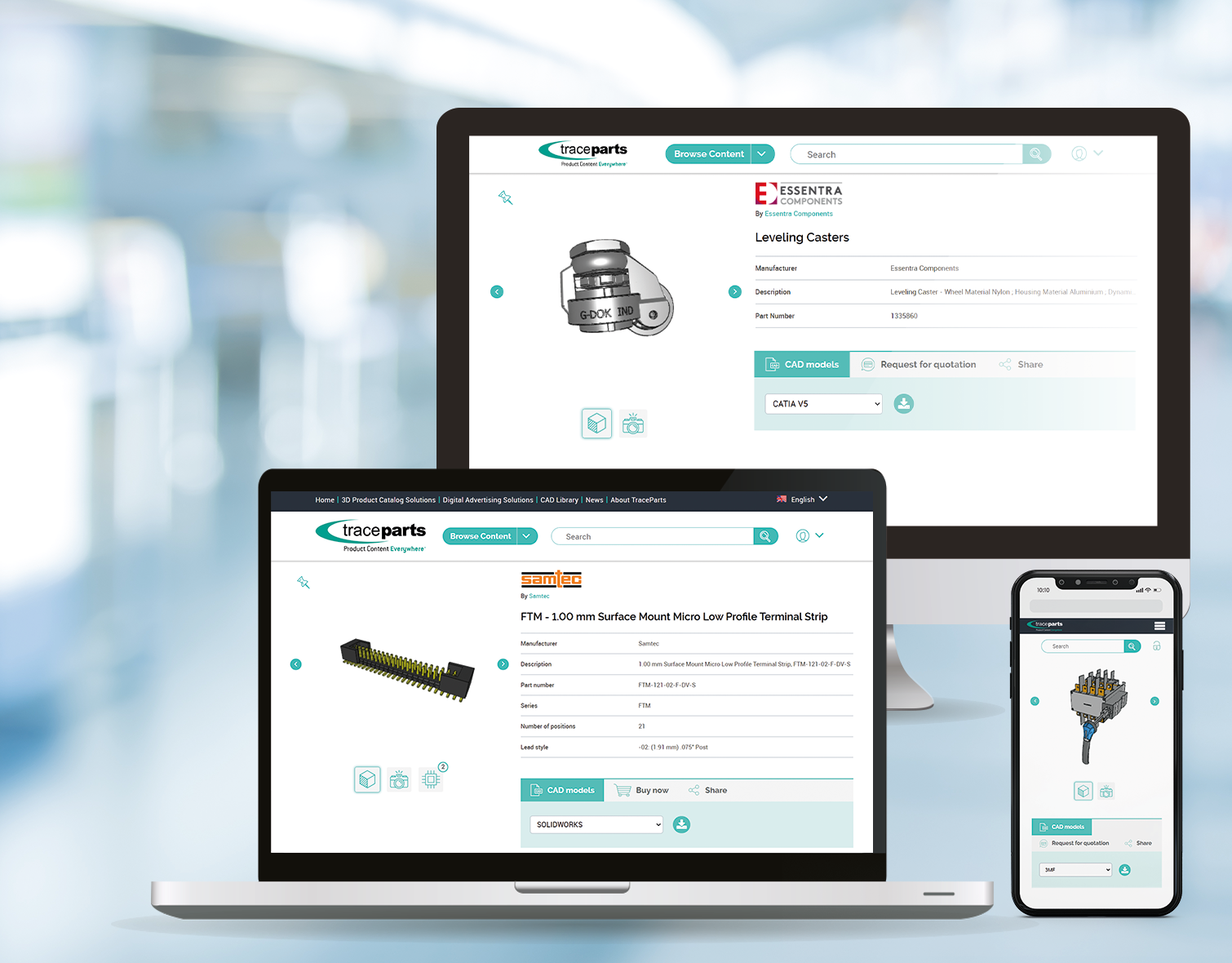
TraceParts enhances 3D Web Viewer Capabilities
TraceParts, a well-known CAD content supplier, integrates robust 3D visualization into their online 3D part viewer to enhance customer ordering experience.
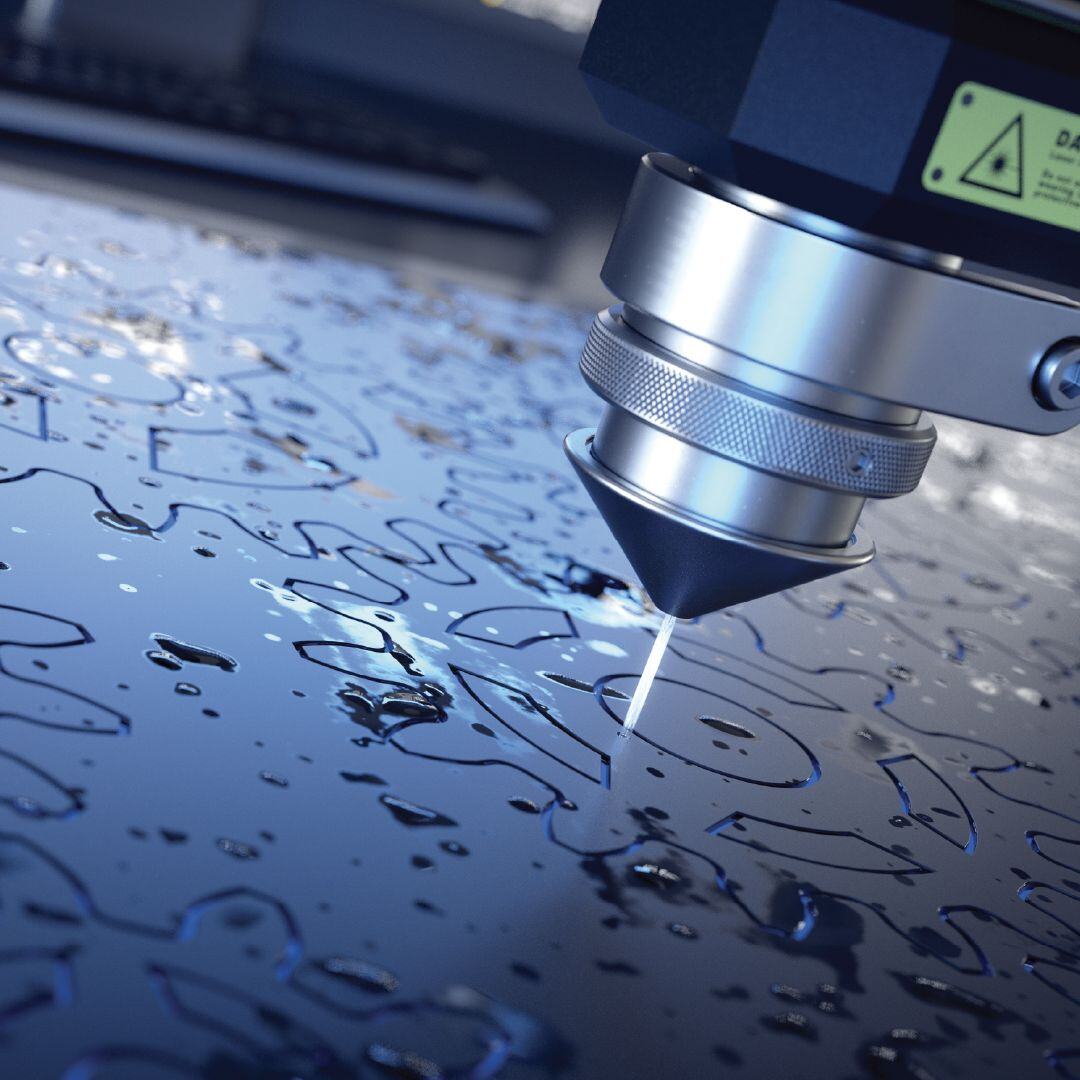

Prototek Released Advanced Digital Manufacturing Quoting
Prototek IQ, empowered by Spatial components allow instant quoting for 3D models. It saves customers’ time, alleviates administrative tasks, and opens new opportunities in digital manufacturing.
-1.png)
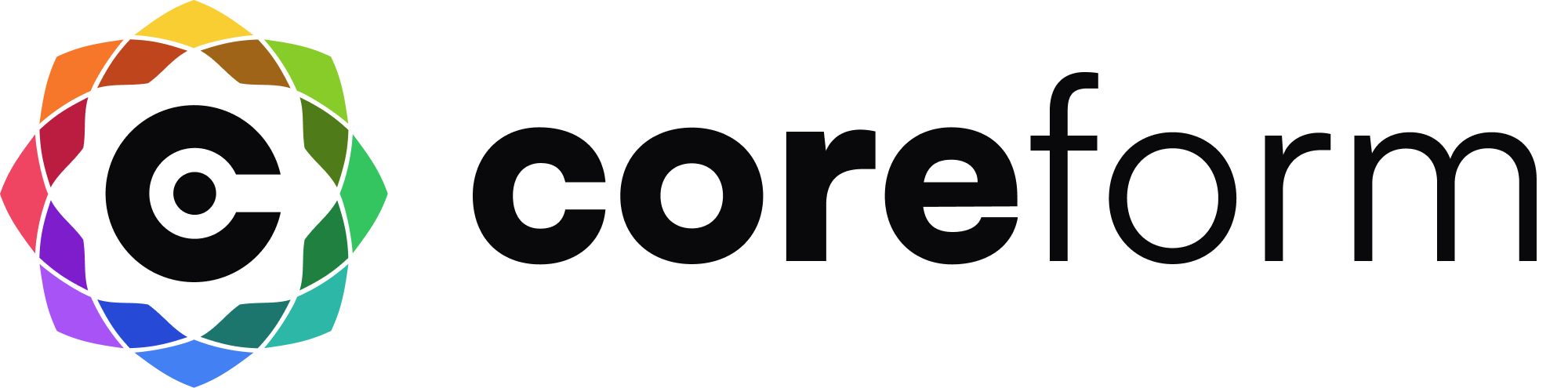
Coreform Brings Game-Changing Simulation Software To Life
Coreform was poised to make a real impact on the CAE world. By integrating specific Spatial SDKs customized to their needs, Coreform closed the circle on its revolutionary software.
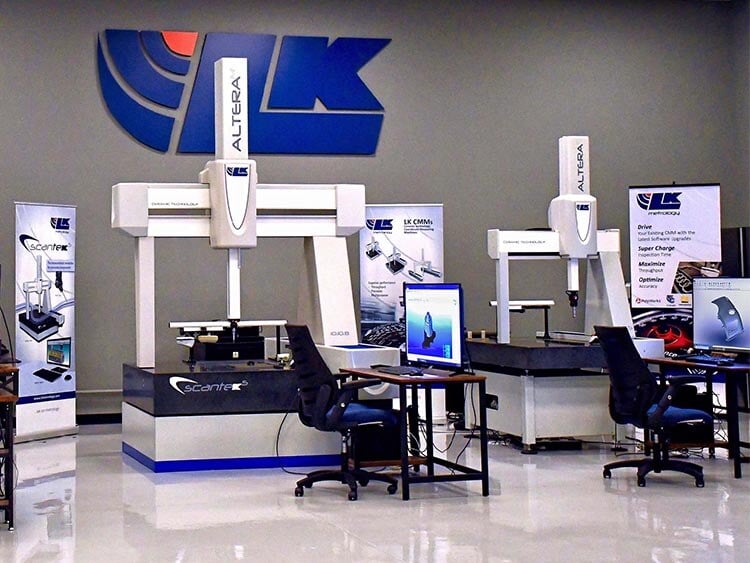
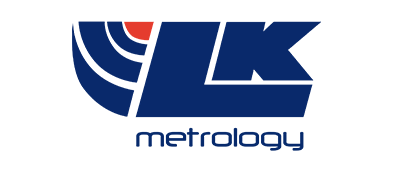
LK Metrology Future Proofed their Application
LK Metrology was on a quest to maintain precision for their Coordinate Measuring Machines. They improved core application functionality through a development partnership with Spatial.
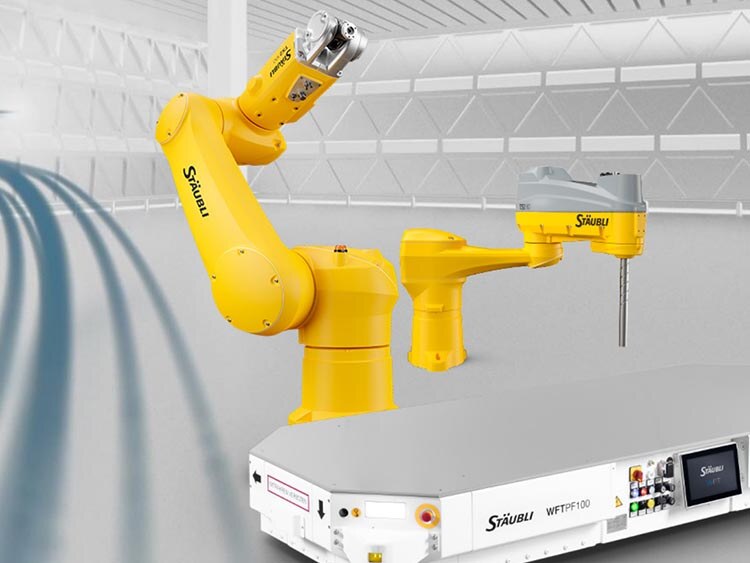
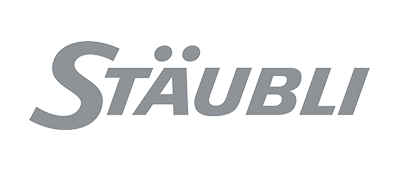
Stäubli Elevated Their Offerings and Capabilities with Spatial's SDKs
Stäubli Robotics Suite 2022 offered optimized features for complex automation scenarios, enabled by Spatial’s CGM Modeler.
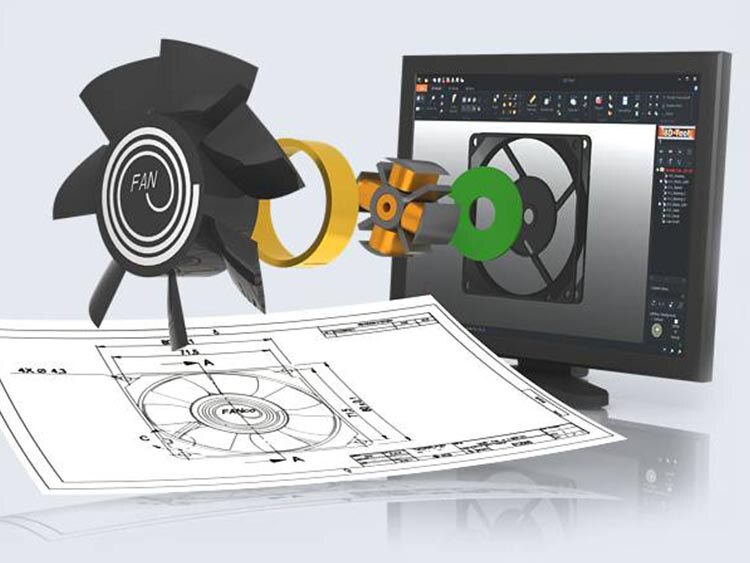
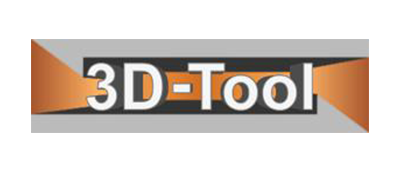
3D-Tool Maximized Customer License Upgrades
3D-Tool expanded Viewer functionality to native CAD formats like CATIA V5 and Pro/E, enabling users to view and translate native CAD files without costly conversion.
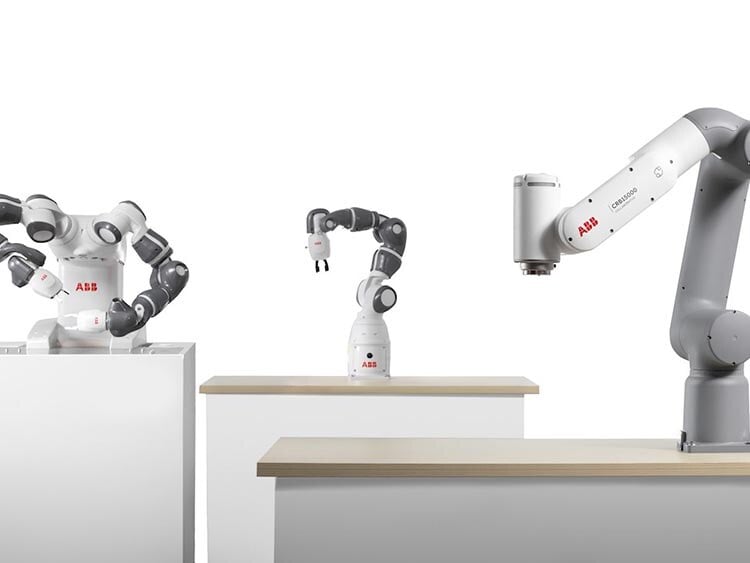
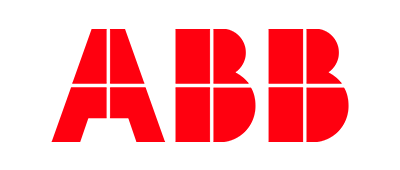
ABB's Programming Without Shutting Down Production
ABB’s Robotics Division used RobotStudio software for PC-based robot programming, boosting productivity without production shutdowns.
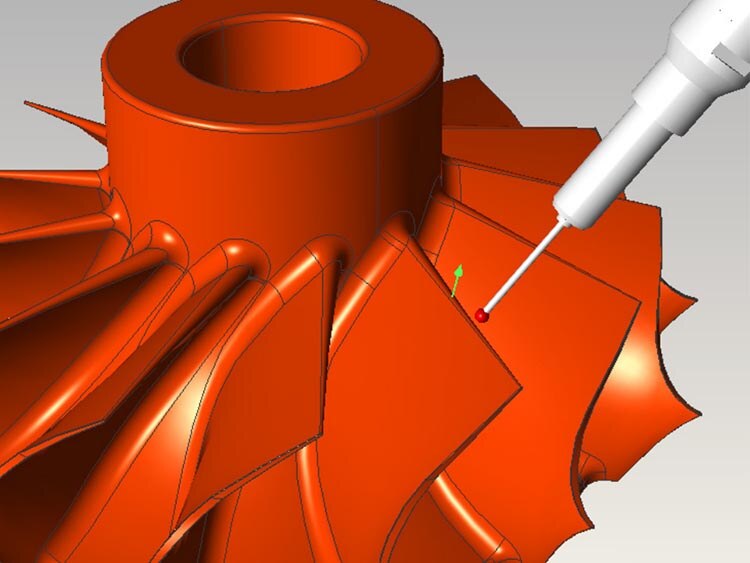
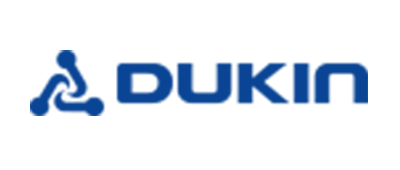
Dukin Co Slashed Development Costs by 50%
Dukin used 3D ACIS Modeler to focus on core technology, reducing time spent on solid modeling and accelerating new product development.
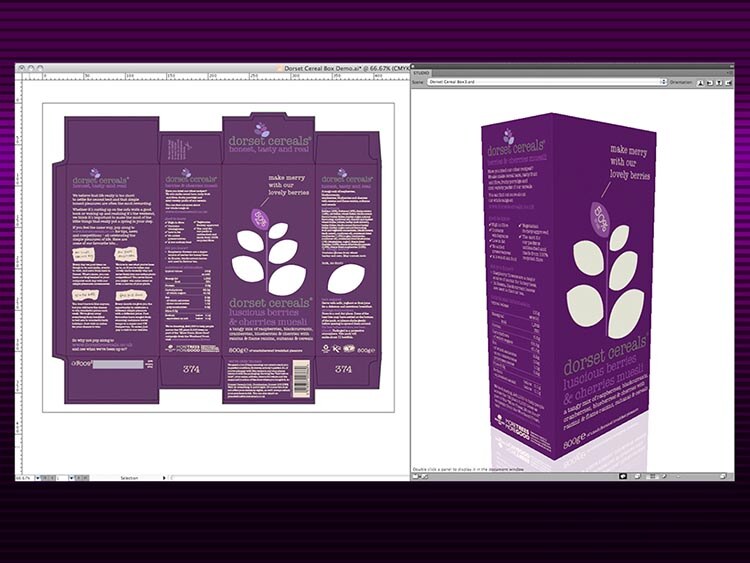
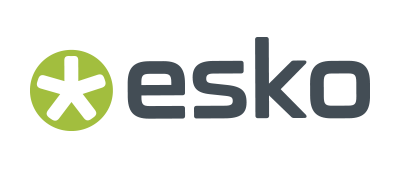
EskoArtwork Drastically Reduced Preparation of CAD Models for Downstream Use
EskoArtwork's ArtiosCAD gained 3D CAD model import functionality, maintaining competitive edge without straining in-house resources.
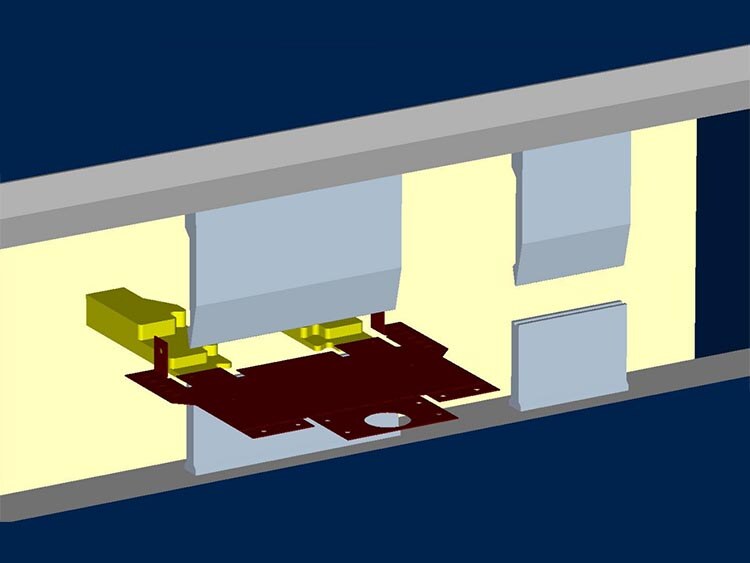
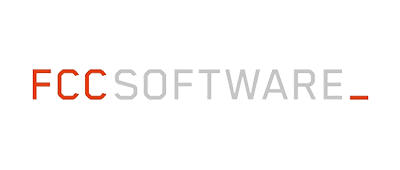
FCC Increased Production Time by 20x
A leading CAM software provider for sheet metal manufacturing used 3D ACIS Modeler for robust 3D modeling and simulation.
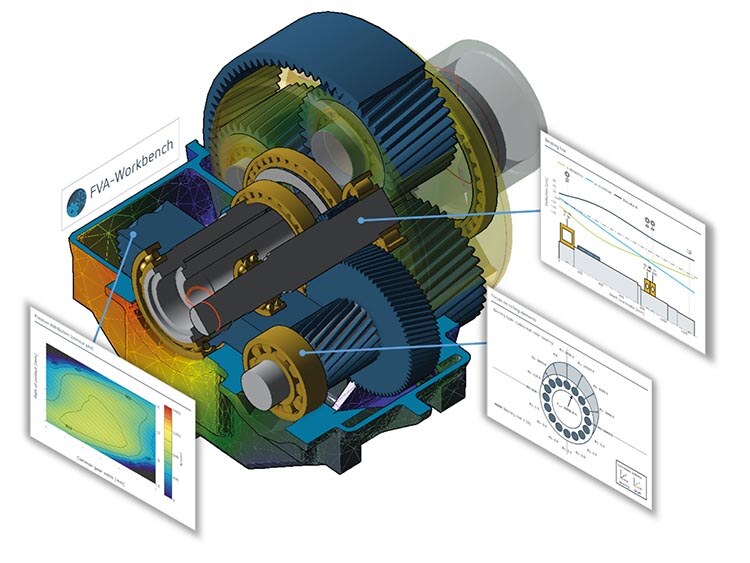
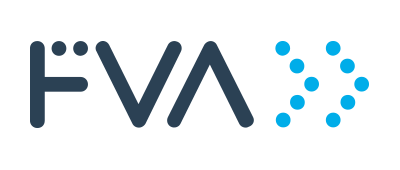
FVA Accelerated Support for New and Updated CAD Formats
FVA's solutions served the driveline industry with software capable of sophisticated simulations and detailed analyses of gearbox components.
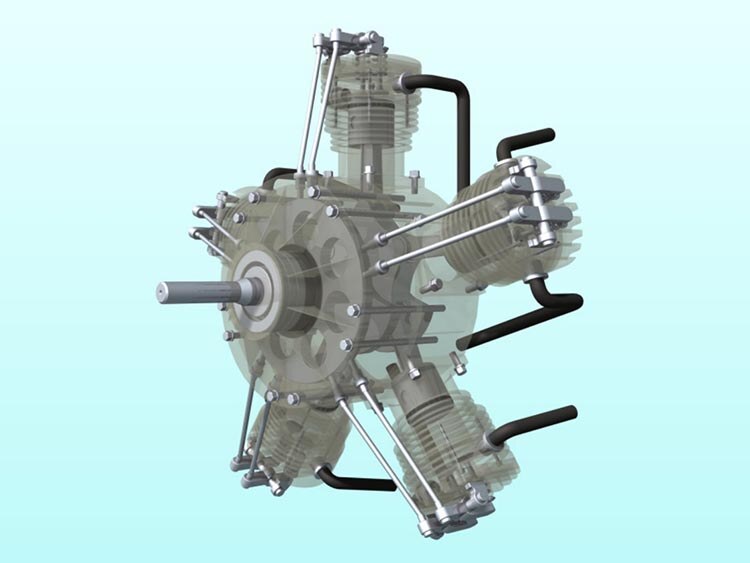
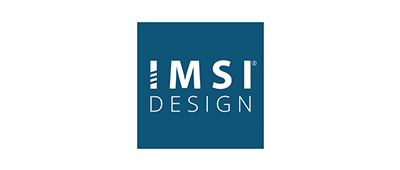
IMSI Accelerated Time-to-Market for New Features
IMSI/Design integrated new versions of ACIS quickly, bringing a new version of TurboCAD to market every 12-15 months.
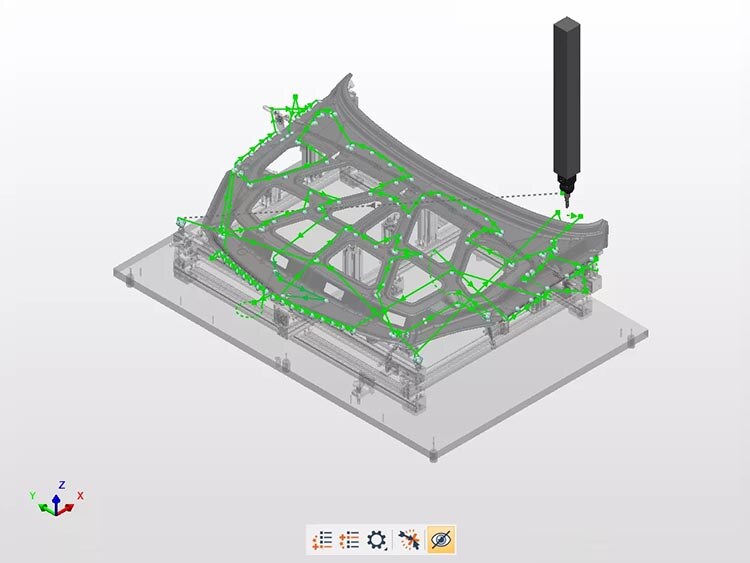
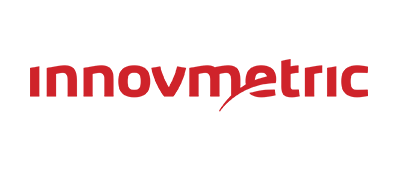
InnovMetric Eliminated Nearly 100% of Their Translation Errors
InnovMetric provided their automotive and aerospace customers with top CAD translators in PolyWorks® by selecting Spatial InterOp software.
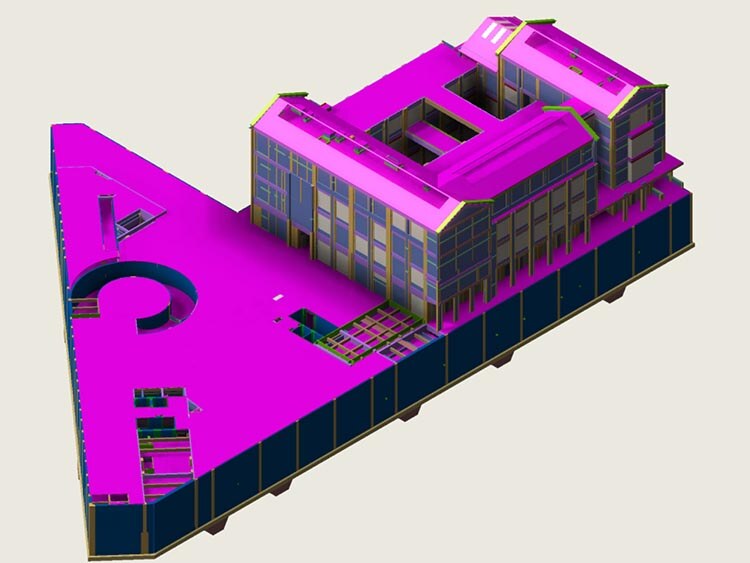
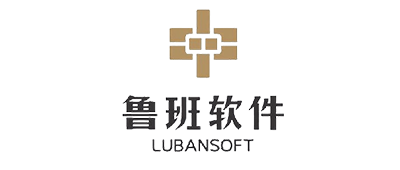
Lubansoft Boosted Design Quality and Reduced Costly Errors
Lubansoft boosted design quality and reduced errors in their BIM software by using 3D ACIS Modeler and HOOPS Visualize.
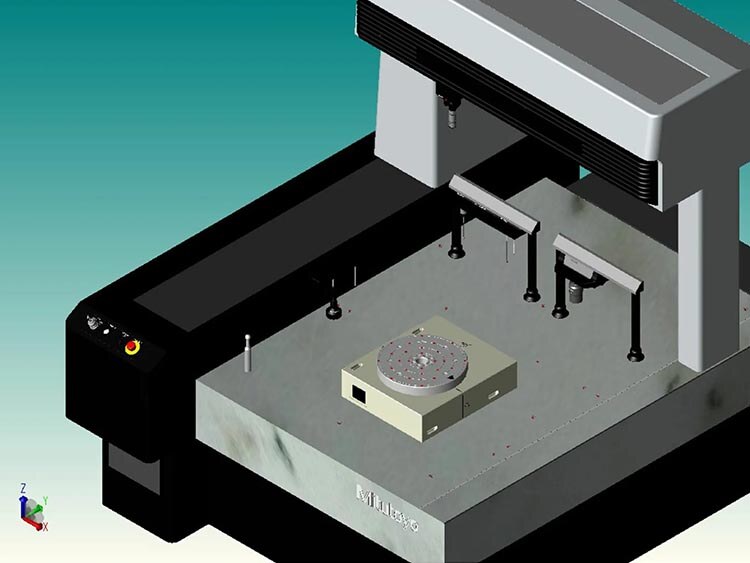
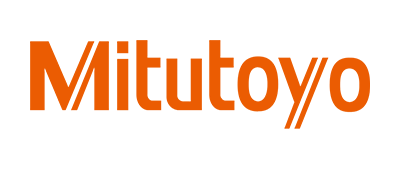
Mitutoyo Supercharged Their 3D Interop Translation
Mitutoyo broadened the use of Spatial technology to other parts of the organization, such as machine configuration.
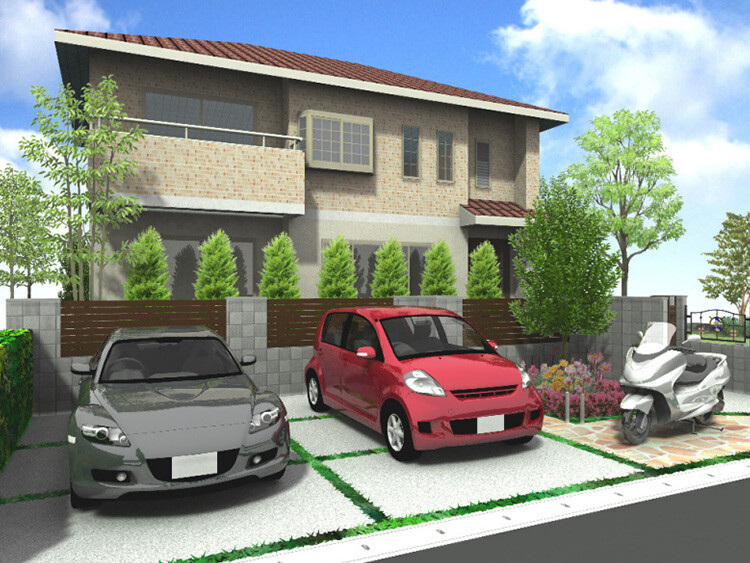
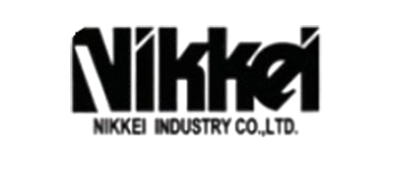
NIS Reduced File Size of Their CAD Design Software by 30%
NIS developed next-generation building exterior and garden design CAD software using 3D ACIS Modeler and HOOPS.
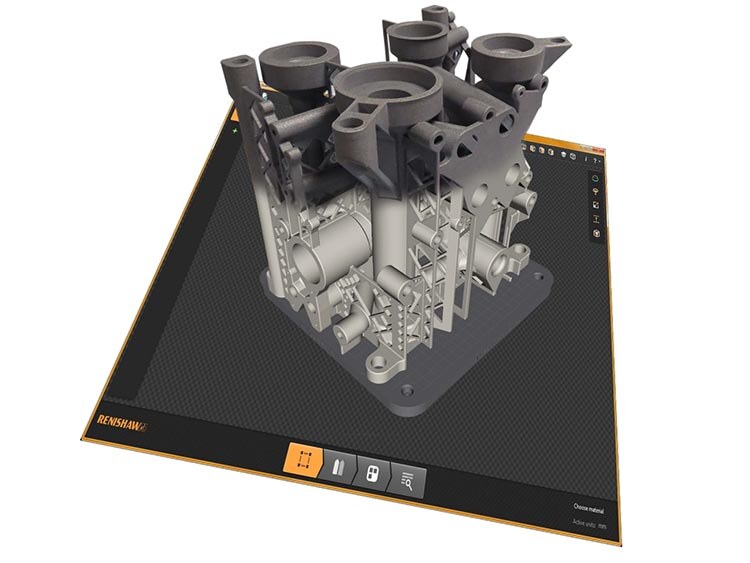
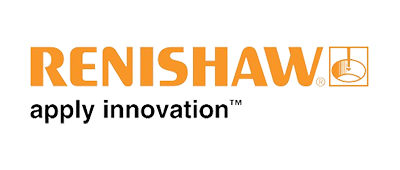
Renishaw Drastically Reduced the Need for STL File Healing
Renishaw integrated Spatial SDKs into QuantAM 2017, enabling users to build parts correctly the first time, preserving original design intent.
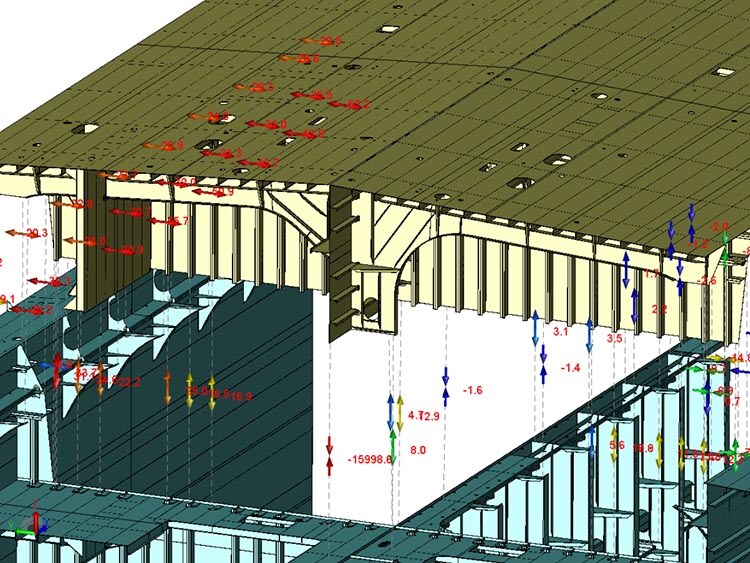
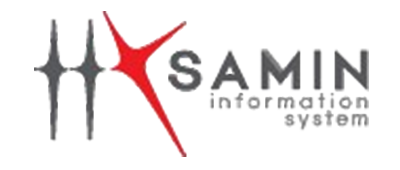
SAMIN Chose Spatial's ACIS 3D Kernel Instead of Parasolid
SAMIN became first to market in 2008 with a 3D accuracy control system that met the high standards of the Asian shipbuilding market using Spatial components.
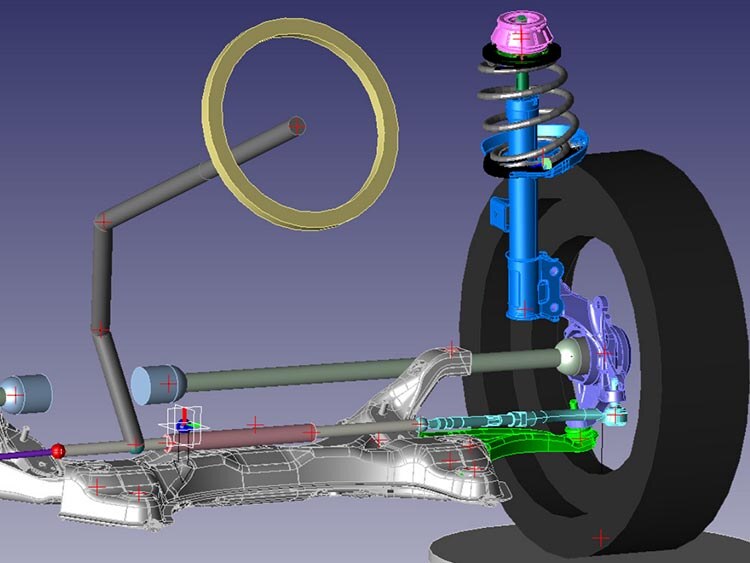
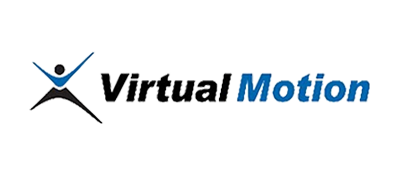
Virtual Motion Cut Development Time by 50%
Virtual Motion integrated the 3D ACIS modeling engine and leveraged AGM and HOOPS to accelerate DAFUL software development, bringing a new product to market quickly.
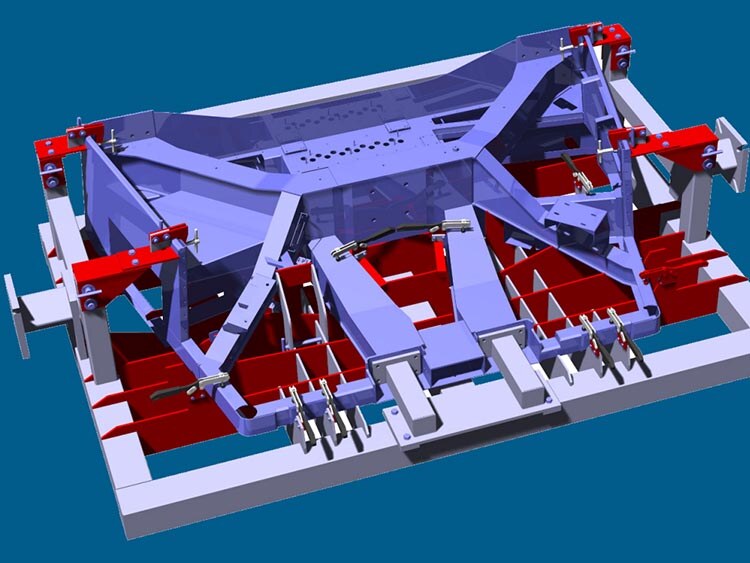
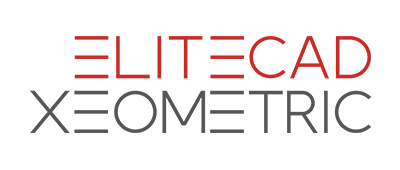
XEOMETRIC Accelerated Blending and Precise Hidden Line Removal
XEOMETRIC's 2D/3D construction planning and mechanical engineering software gained advanced functionality with 3D ACIS Modeler and 3D InterOp.
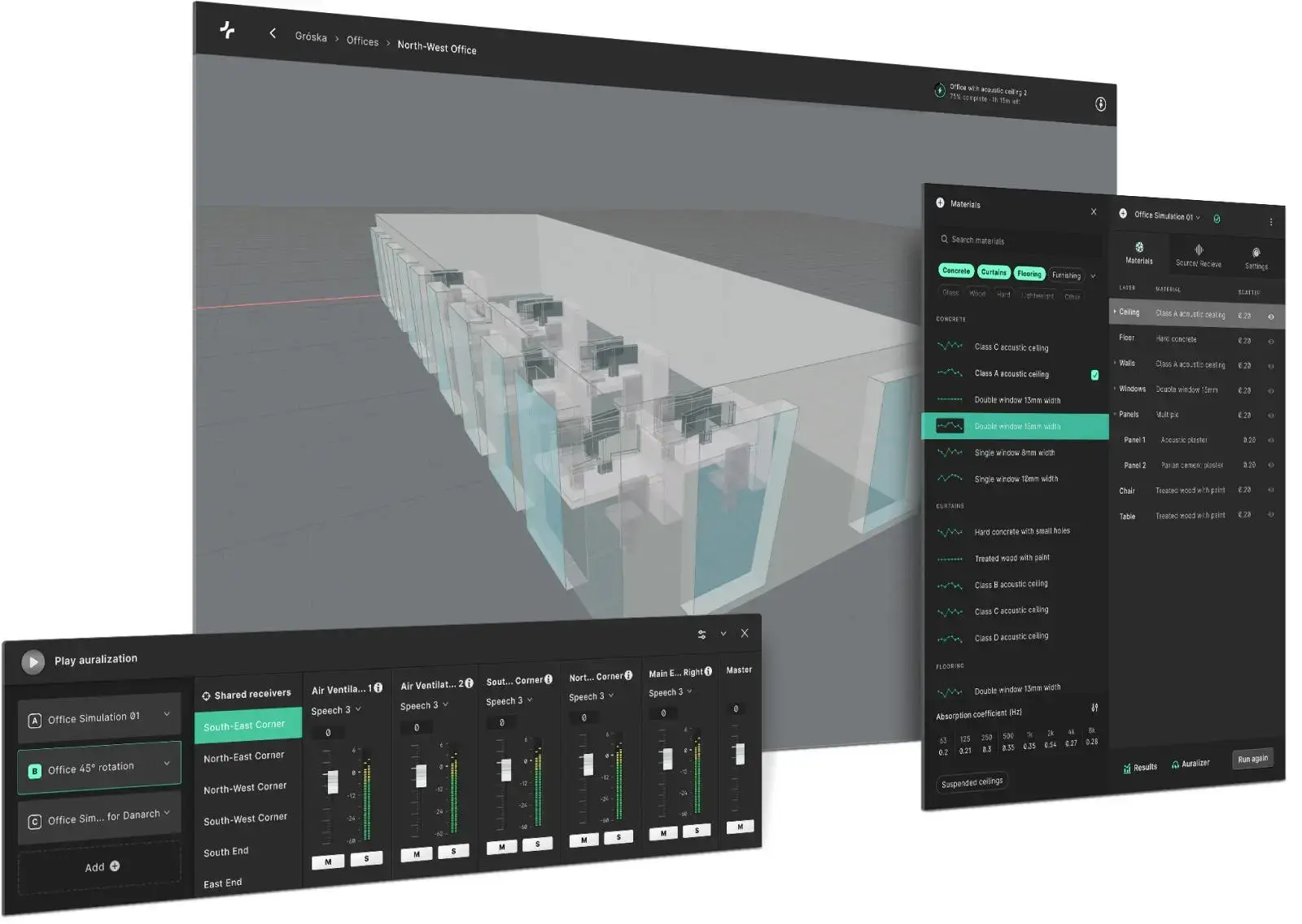
Treble Technologies Streamlines Simulation with Automatic 3D Meshing
Treble Technologies accelerated their simulation pipeline by integrating Spatial’s Meshing SDK, enabling faster, high-fidelity acoustic simulations at scale.