3D SDKs for Additive Manufacturing
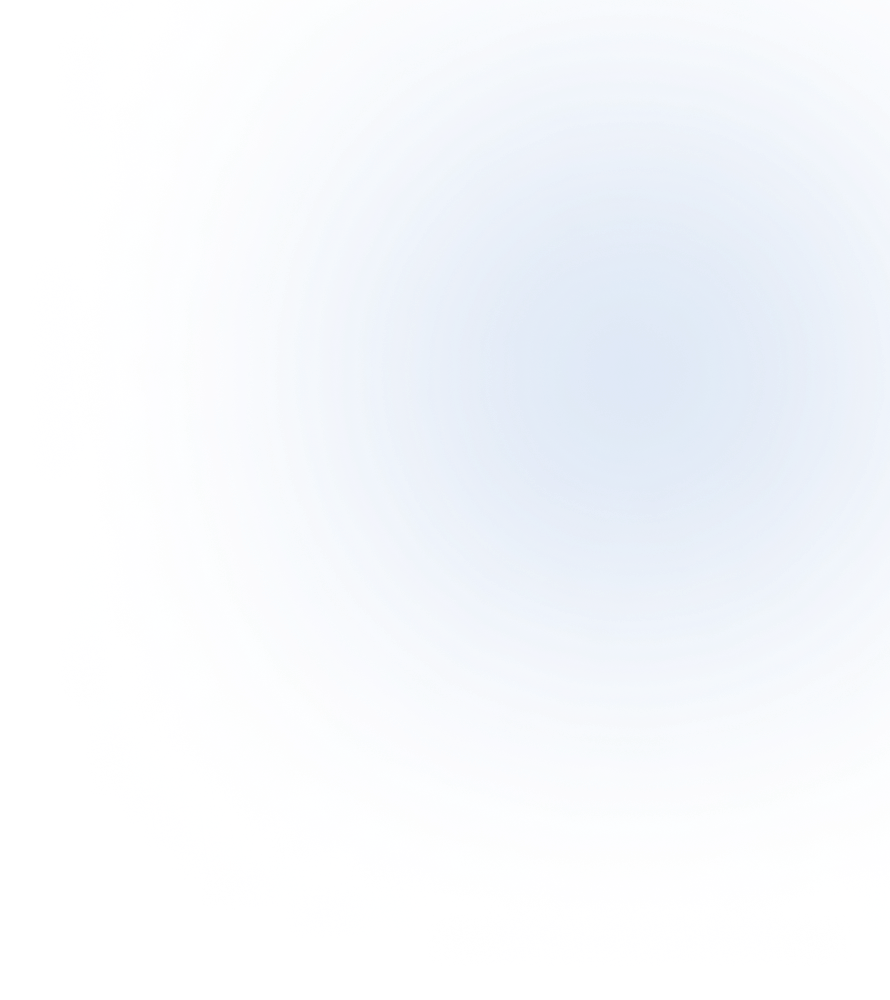
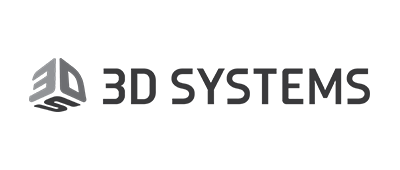
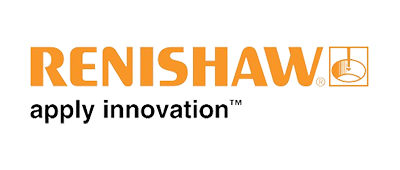
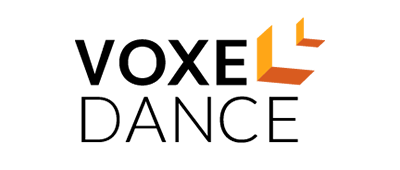
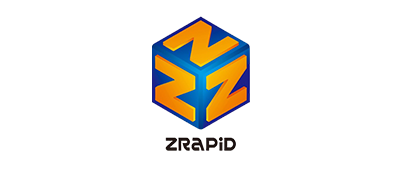
Key Challenges in Software Development
for Additive Manufacturing
Printability
Address common issues such as incorrect geometry, thin walls, missing faces, and orientation to ensure models are ready for 3D printing.Interoperability
Facilitate seamless integration between design software and additive manufacturing software for a smoother workflow.Data Integrity
Preserve the quality and accuracy of 3D models throughout their lifecycle, from design to manufacturing.Time to Market
Meet customer demands by streamlining development processes to deliver solutions. faster.
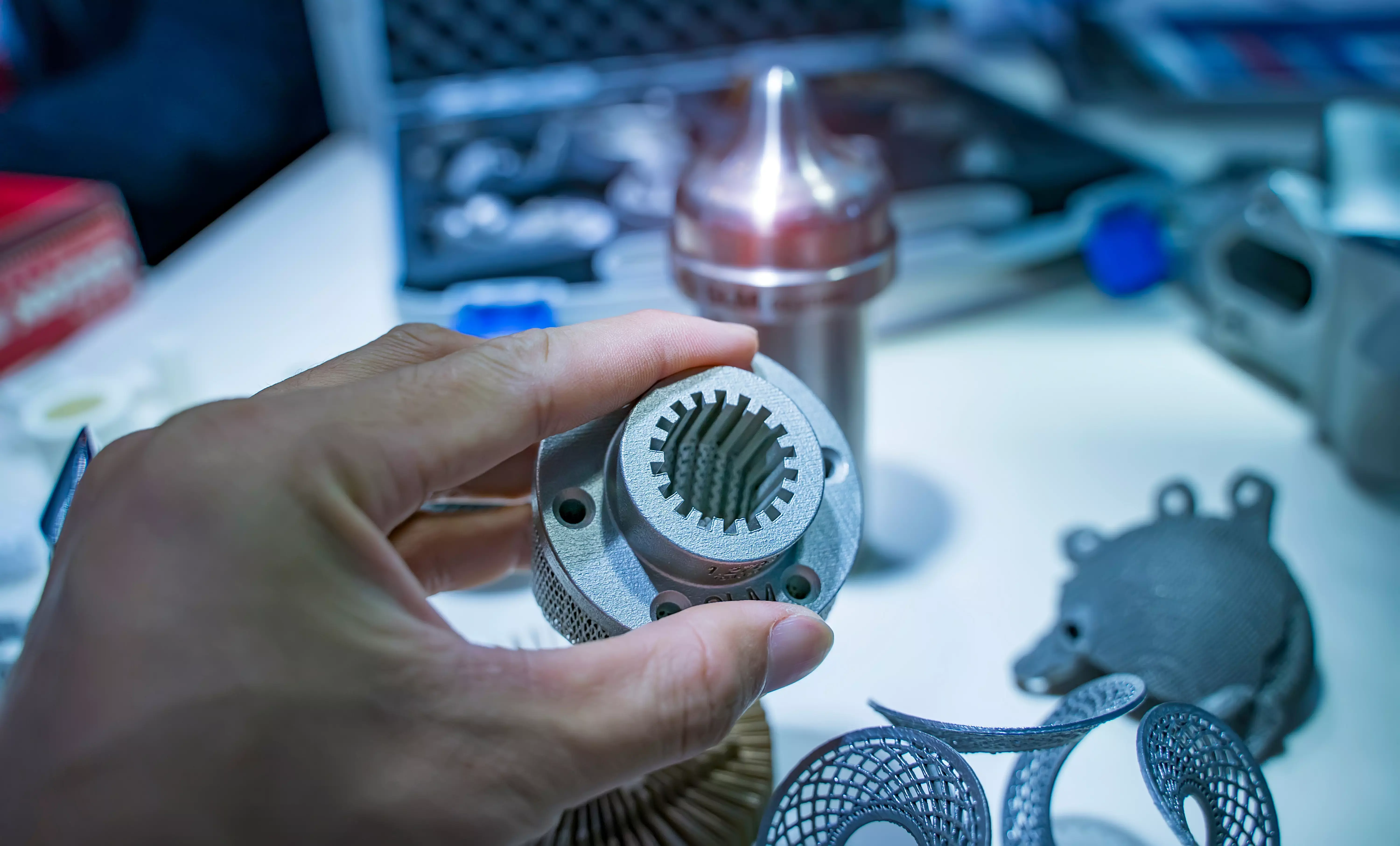
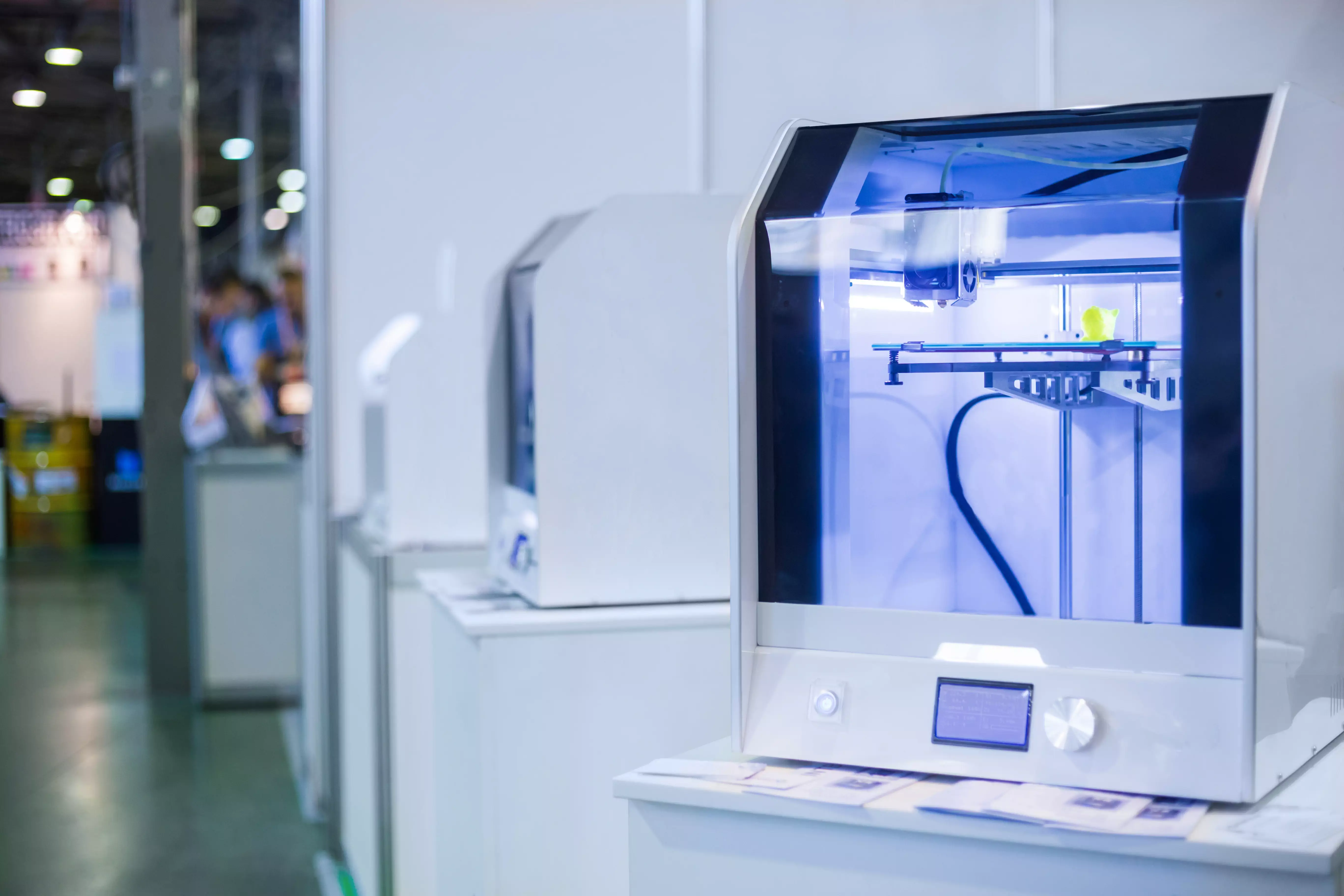
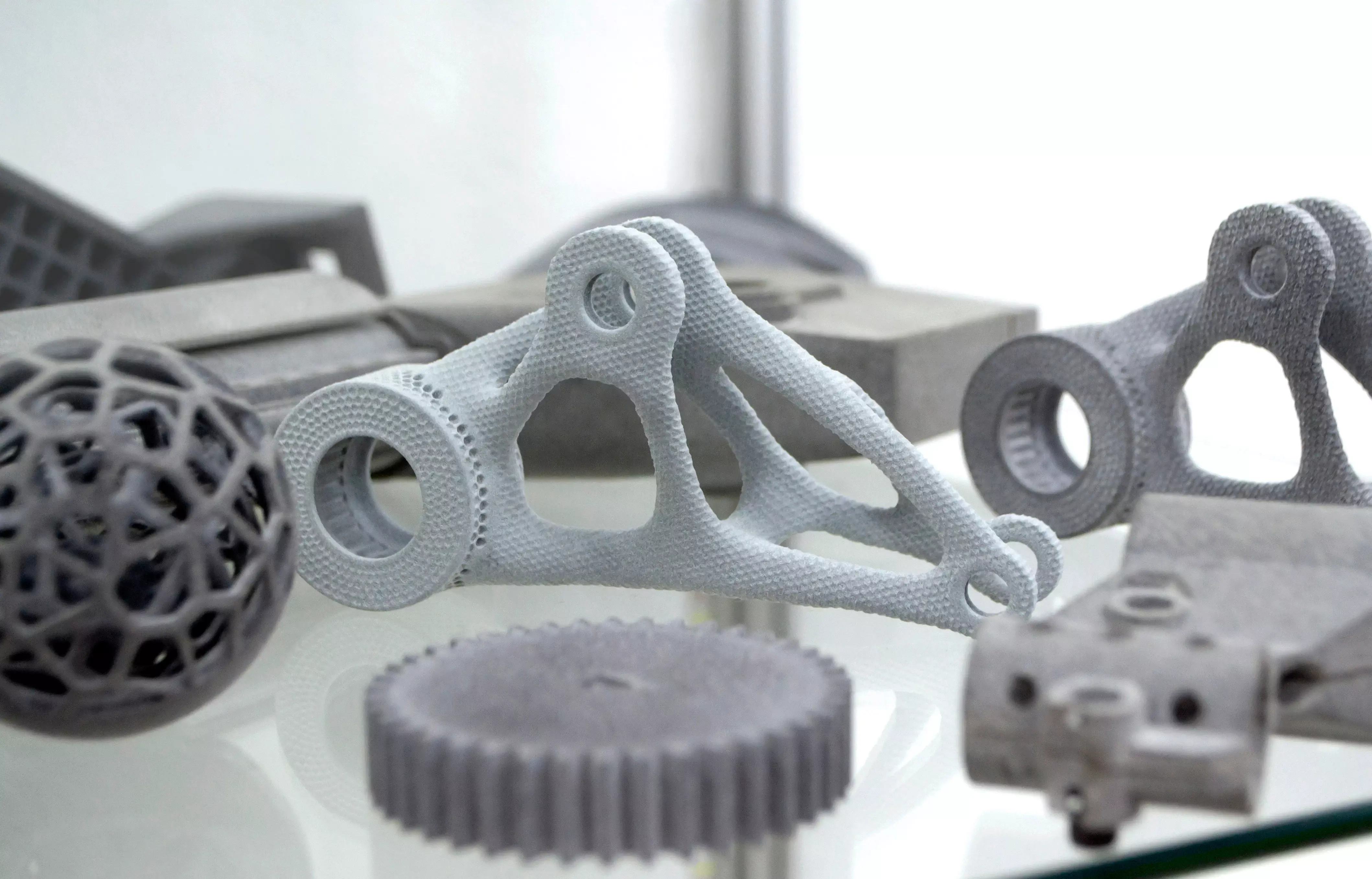
Discover Our Full Suite of Solutions for Additive Manufacturing
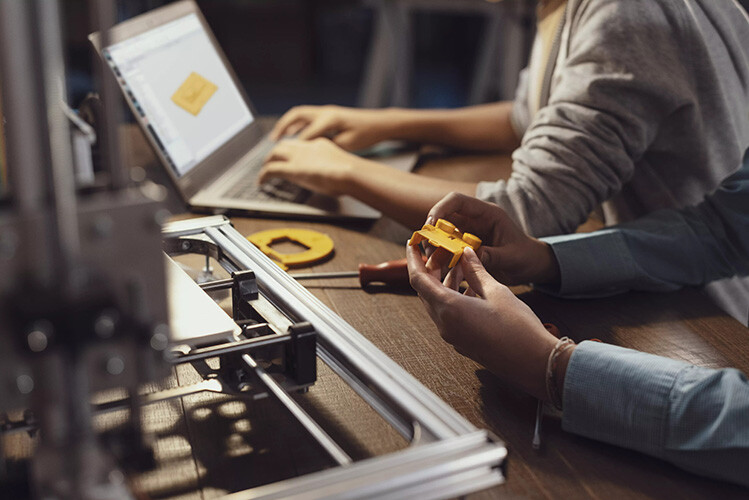
Seamless CAD Import with 3D InterOp
Spatial’s additive manufacturing toolkit includes 3D InterOp, which enables top-notch CAD import and expertly handles B-rep geometry and non-exact geometry. It enables your application to work with an extensive breadth of CAD formats in a seamless, unified way.
Advanced B-rep and Polyhedral Modeling capabilities
CGM, our robust Modeler, and its add-on, CGM Polyhedra, provide modeling capabilities like geometric feature recognition, defeaturing, direct editing of B-rep, healing and cleaning. Features smaller than printer resolution often have to be added to the part by machining after the print. Geometric functionality allows the software to automatically identify and remove features below printer resolution and drive secondary machining operations using information about small hole positions and sizes.
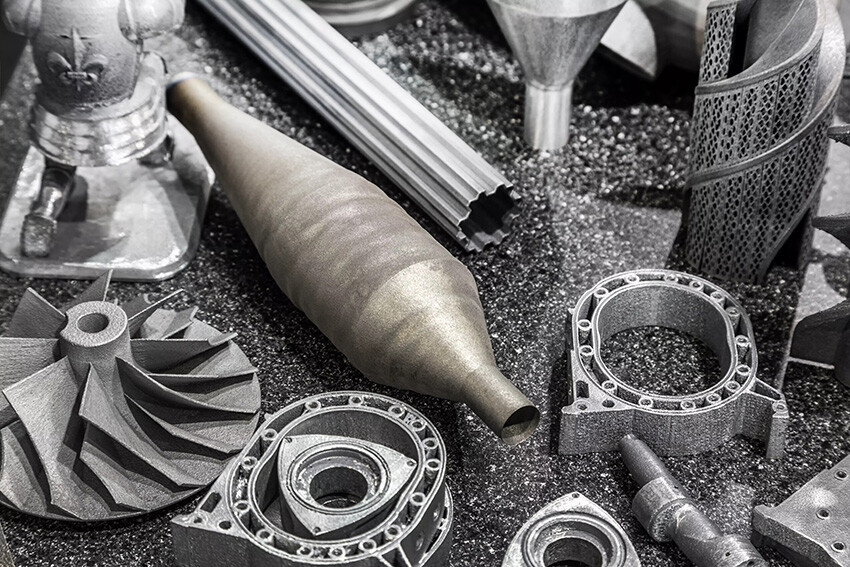
Efficient Printing with Thin-Walled Solids
Printing solid geometry often uses excess material and generates thermal distortion during cooling. Thin-walled solids allow printing of the same external shape using less material and generating less heat. Spatial’s industry-leading 3D modelers provide a full boundary representation of the 3D models, enabling you to shell solid bodies with controlled wall thickness before printing—and specify extra thicknesses in load-bearing regions.
Enable Manufacturing at Scale
Enable manufacturing at scale by nesting multiple instances of a part in a pre-defined space. 2D and 3D nesting allows for orientation and nesting of parts in all three directions. Minimize material costs by automatically orienting the part to optimize support material volume. This is commonly used by 3D printing applications where support generation isn’t required.
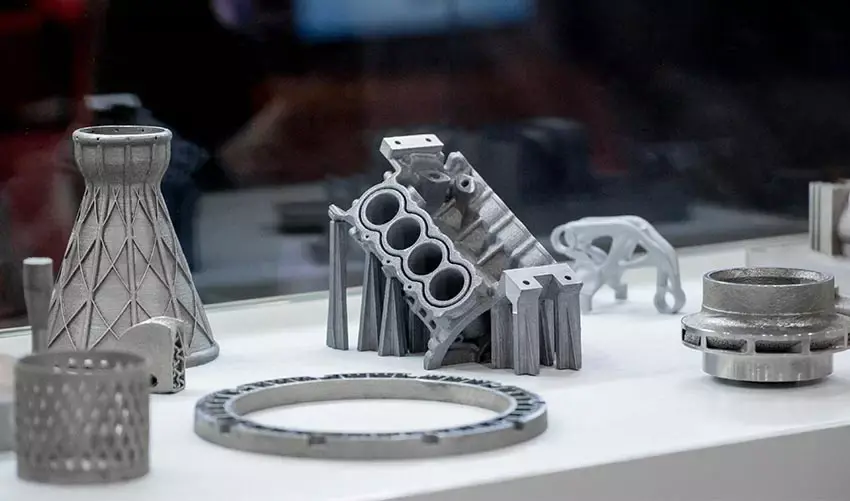
Support Generation for Metal Print Processes
Improve heat dissipation and automatically generate supports with automatic Support Zone Computation, wire (non-solid) supports, and cone and volume (solid) supports. This is highly suitable for metal print processes like PBF.
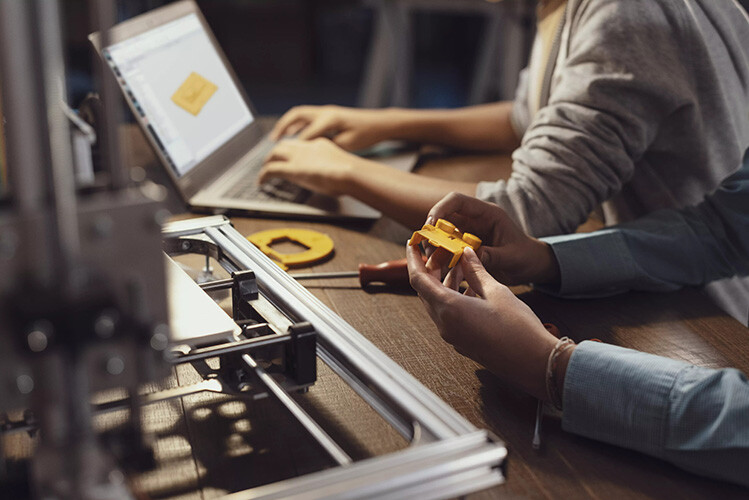
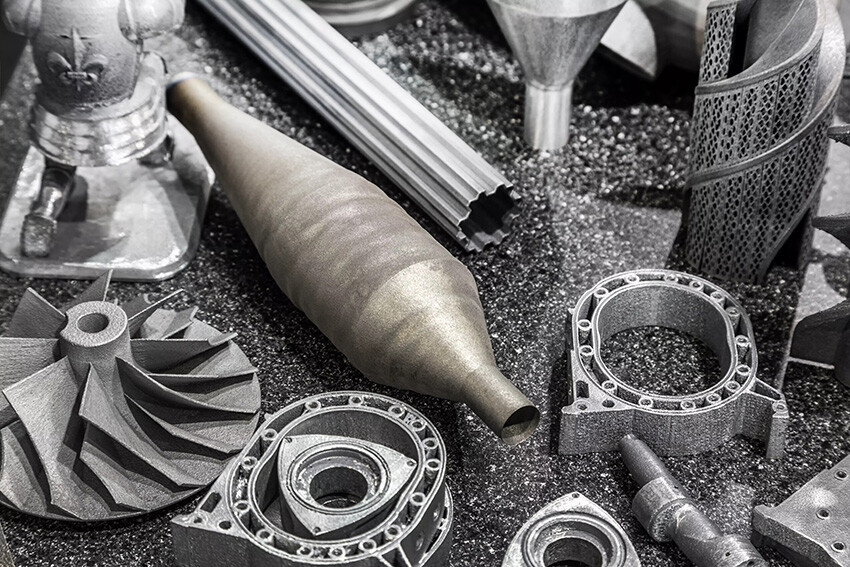
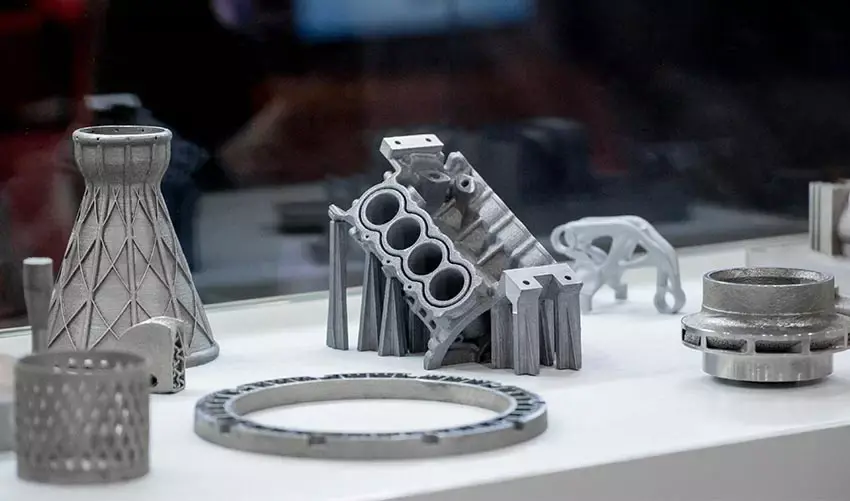
Specific Workflows for Additive
Manufacturing Software
Spatial SDKs optimize the additive manufacturing workflow, utilizing
innovative hybrid modeling capabilities to access and modify precise and polyhedral data.
Spatial supports your AM workflow from beginning to end.
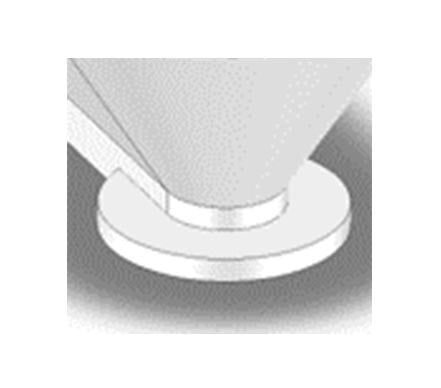
3. Prepare for Print
- Geometry edit or creation
- Offsetting & Hollowing
- Lattice Generation
- Simplification
- Defeaturing
Features Made for Additive
Manufacturing Workflows
software companies. Whether you’re an OEM of 3D printers or an ISV in the AM industry, our
SDKs will help you meet your development goals.
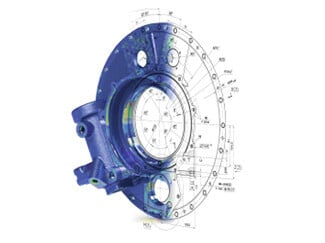
Comprehensive Data Import and Automatic Healing
3D InterOp supports the import of various CAD data formats. It ensures the accurate import of B-Rep or Polyhedral CAD data and allows for efficient data extraction, including geometry and metadata.
Some supported CAD formats are STL, 3MF, OBJ, AMF, CATIA, SolidWorks, NX, STEP and IGES. See the full list here (Link the 3D interop page)
ACIS and CGM Polyhedra offer automatic healing capabilities to ensure dirty STL data can be easily repaired and made ready for printing.
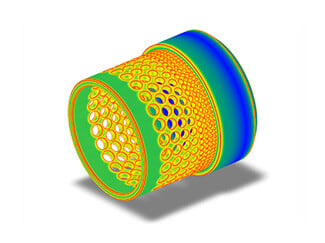
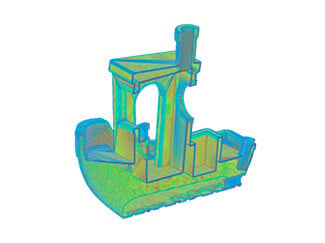
Wall Thickness Analysis
The wall thickness analysis tool reduces the need for multiple print iterations. Build a pre-processor in your application that helps verify the structure of the final print beforehand, ensuring strength and stability in the printed parts.
Identify and correct regions that are thick and causing heat build-up, regions that are thin and structurally unsound, and sharp edges and corners that the process may not support.
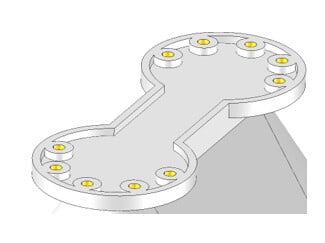
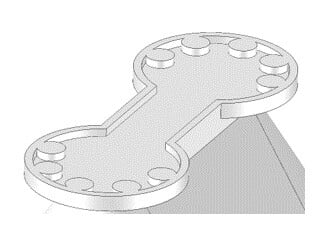
Feature Recognition and Automatic Defeaturing
This feature allows for easy editing of models in the preprocessing phase. It includes feature recognition and automatic defeaturing, simplifying necessary design modifications.
Allow detection of geometric features like holes, fillets and pockets.
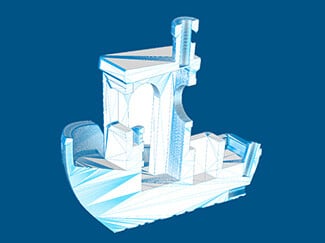
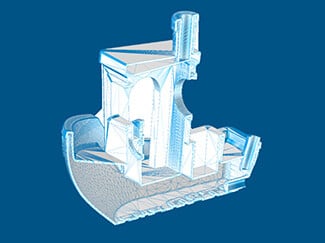
Hollowing Operations
By using our Hollowing feature, you can reduce the amount of material used to print an object, lowering material costs, especially for large parts. Less material means also less printing time, speeding up the overall manufacturing process.
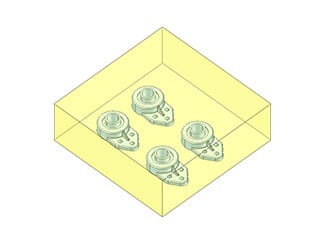
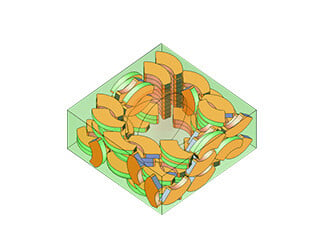
Advanced Automatic 2D, 2.5D and 3D Nesting for Efficient Manufacturing
Our automatic 2D, 2.5D and 3D Nesting feature significantly enhances manufacturing efficiency by enabling the precise placement of multiple part instances within a predefined space.
This feature achieves a tighter fit than traditional bounding box methods, reducing the need for support material and optimizing material use.
Parts are automatically oriented to prevent interlocking and facilitate easier post-processing. Additionally, you can customize nesting zones and designate exclusion areas, tailoring the layout to specific production needs.
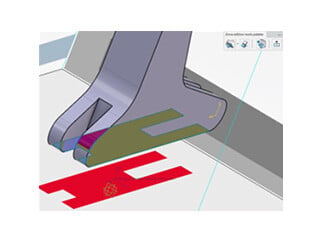
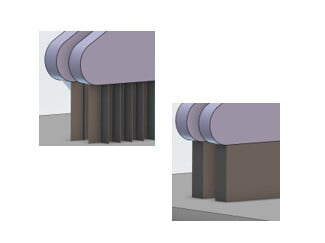
Automatic Support Generation
This technology computes support zones and offers multiple support shapes, ensuring that each print is adequately supported for quality results. This process is highly suitable for metal print processes like PBF.
Support zone shapes: Wire (non-solid) Supports, Cone and Volume (solid) Supports.
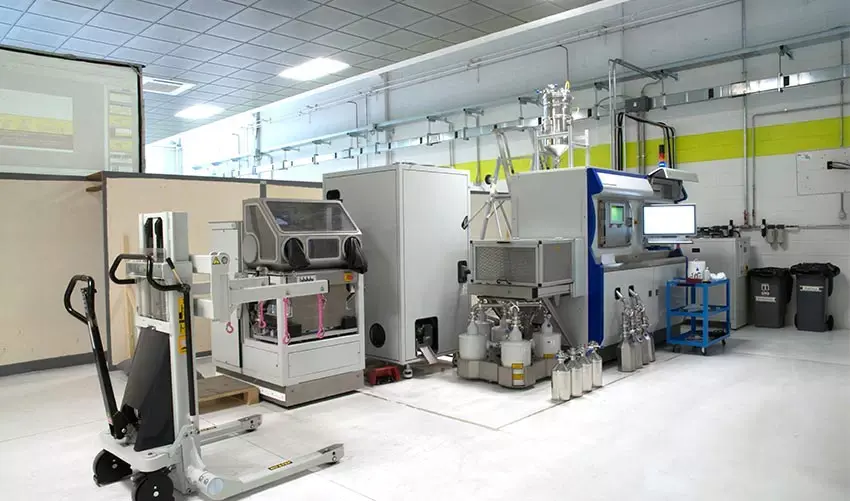
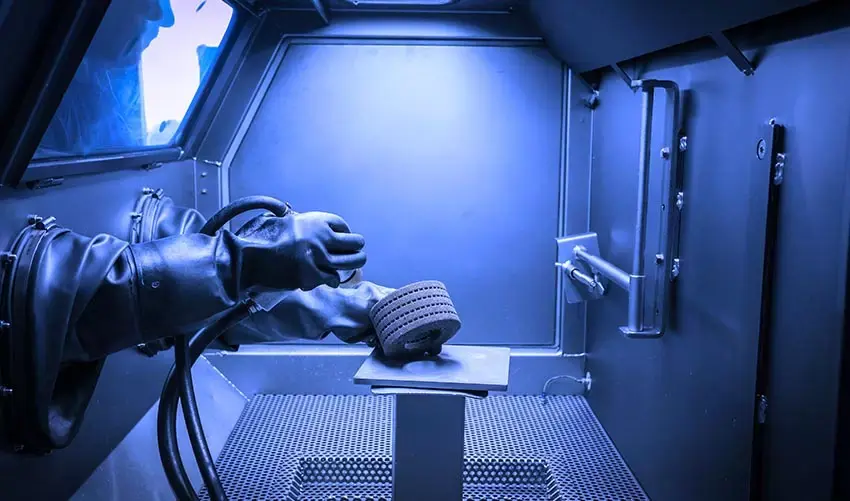
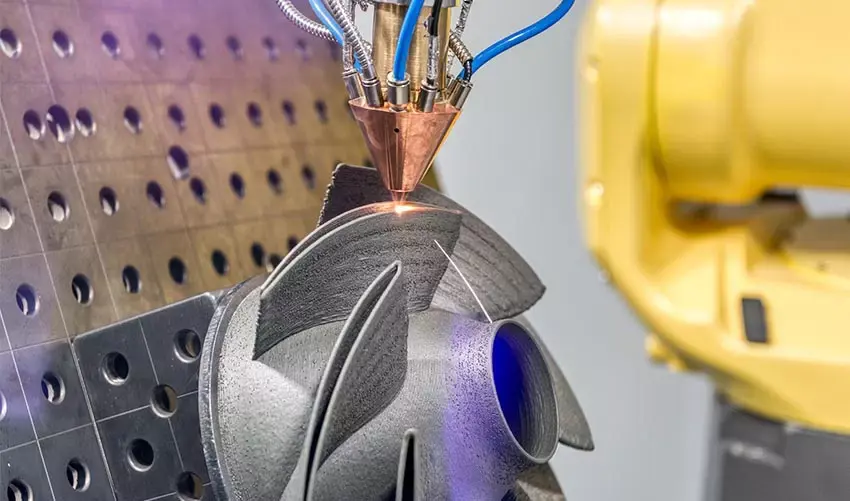
Why Work With Spatial SDKs?
software. Combined with our expert guidance, you’ll benefit from unique perks
that carry through to your bottom line.
Exclusive Access to Multiple Core Technologies
Work With a Solution Advisor
Access to Industry-Specific APIs
Accelerate Your Innovation
Get Started With Spatial
Do we have the technology to take your 3D application workflows to the next level? Find out by speaking with a Spatial expert.

Our collaboration with Spatial now allows us to not only perform high-quality healing on STL files but, more importantly, to import various CAD formats directly.
Stephen Anderson, Director of Group Software, Renishaw
Read the Case Study
All Our Additive
Manufacturing Resources
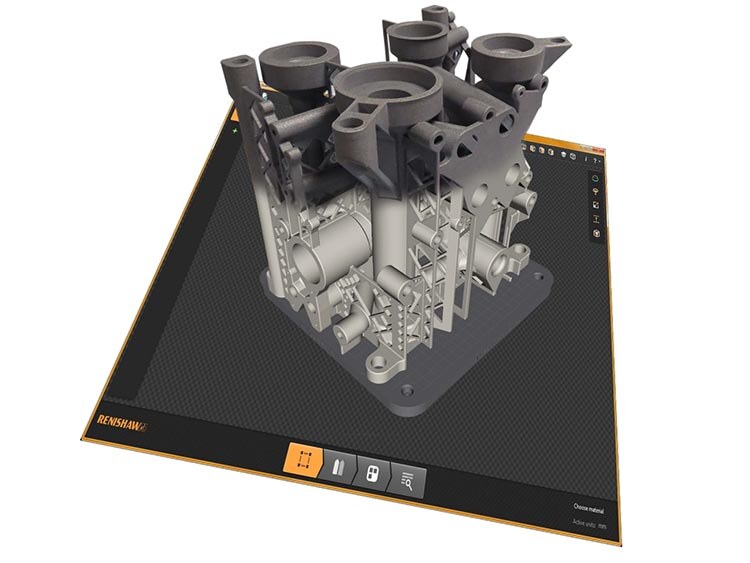
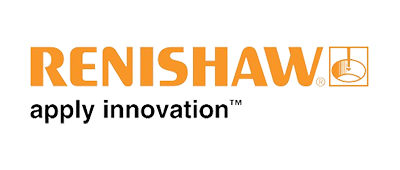
Renishaw Drastically Reduced the Need for STL File Healing
Renishaw integrated Spatial SDKs into QuantAM 2017, enabling users to build parts correctly the first time, preserving original design intent.
Additive Manufacturing - Top 5 Ways to Increase Revenue and Margins
Explore scenarios for Additive Manufacturing OEMs to offer complete solutions, impacting revenue and margins.
A 3 Part Guide for Machine Tool Manufacturers
A 3-part guide for Machine Tool Suppliers on boosting hardware sales through software differentiation and choosing the right development toolkit.
Automatic CAM (ACAM) in Subtractive CNC Machining
Discover Automatic CAM, the enabling processes, and its application benefits.
Enable Automatic Supports Creation in your 3D Printing Application
Explore our new additive manufacturing capabilities within CGM Modeler in this webinar.
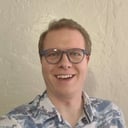
Additive Manufacturing - Top 5 Ways to Increase Revenue and Margins
Explore scenarios for Additive Manufacturing OEMs to offer complete solutions, impacting revenue and margins.
A 3 Part Guide for Machine Tool Manufacturers
A 3-part guide for Machine Tool Suppliers on boosting hardware sales through software differentiation and choosing the right development toolkit.
Automatic CAM (ACAM) in Subtractive CNC Machining
Discover Automatic CAM, the enabling processes, and its application benefits.
Enable Automatic Supports Creation in your 3D Printing Application
Explore our new additive manufacturing capabilities within CGM Modeler in this webinar.
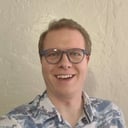
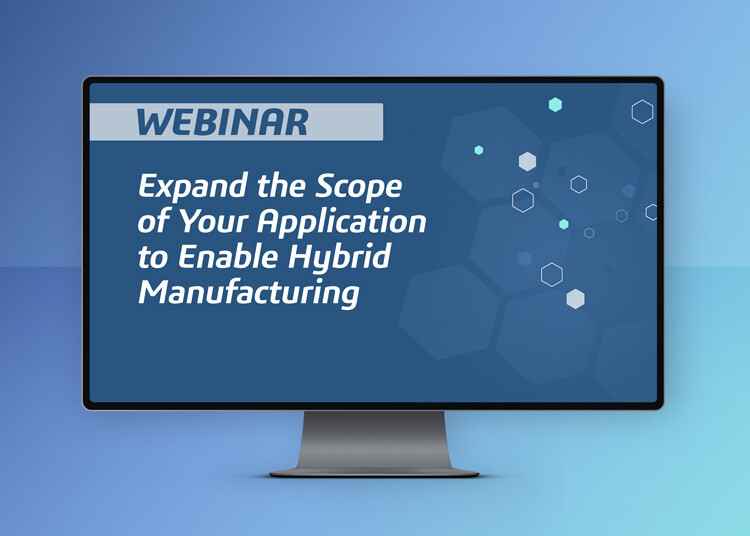
Expand the Scope of Your Application to Enable Hybrid Manufacturing
Discover how to handle both CAD and scanned data for hybrid manufacturing.
Technical Series: Enable Automated Lightweighting of Parts and Creation of Supports for Additive Manufacturing
Discover how your 3D application can leverage CGM Modeler’s Automated Lightweighting and Support Creation capabilities.
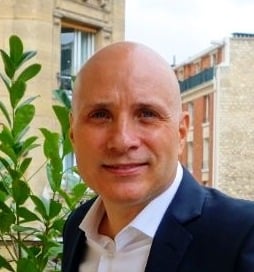
Bring Your Assembly Modeling to Life with Parametric Constraint Management
Learn how you can enable constraint management and assembly modeling in your 3D application with Spatial’s Constraint Design Solver SDK.
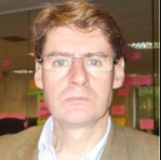
ACIS Polyhedra - Mesh Handling for ACIS Customers
Convert ACIS B-Rep bodies into meshes or import meshes directly into 3D ACIS Modeler for advanced model manipulation and preparation.
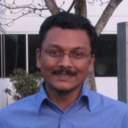
Accelerate your 3D Application’s Development with AGM
Learn how you can significantly speed up your application’s development with AGM’s extensive, out-of-the-box, advanced code base.
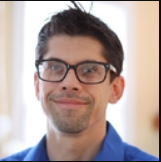
Technical Series: Enable Automated Lightweighting of Parts and Creation of Supports for Additive Manufacturing
Discover how your 3D application can leverage CGM Modeler’s Automated Lightweighting and Support Creation capabilities.
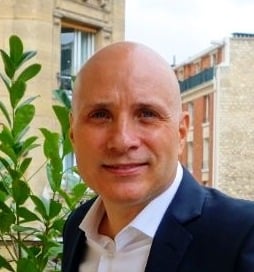
Bring Your Assembly Modeling to Life with Parametric Constraint Management
Learn how you can enable constraint management and assembly modeling in your 3D application with Spatial’s Constraint Design Solver SDK.
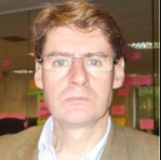
ACIS Polyhedra - Mesh Handling for ACIS Customers
Convert ACIS B-Rep bodies into meshes or import meshes directly into 3D ACIS Modeler for advanced model manipulation and preparation.
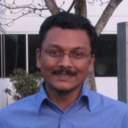
Accelerate your 3D Application’s Development with AGM
Learn how you can significantly speed up your application’s development with AGM’s extensive, out-of-the-box, advanced code base.
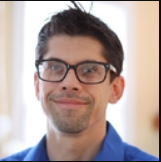
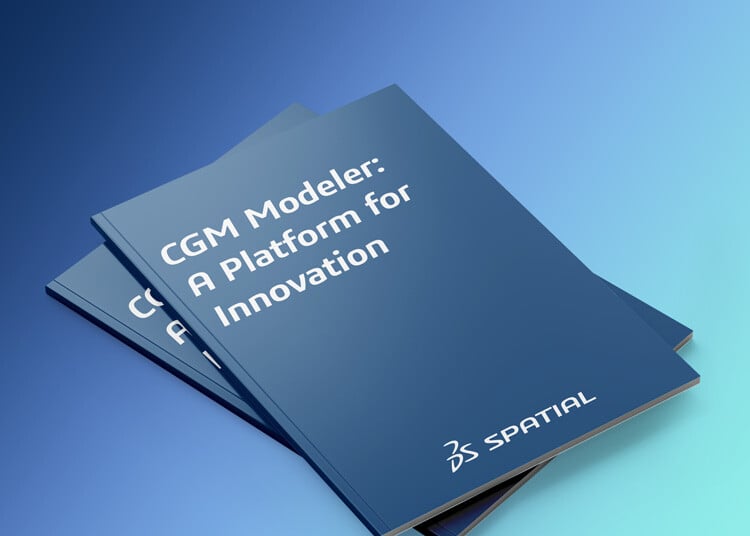
CGM Modeler: A Platform for Innovation
Learn how CGM Modeler enables application development for creating, modifying, querying, and visualizing 3D data across industries.
Automatic CAM (ACAM) in Subtractive CNC Machining
Discover Automatic CAM, the enabling processes, and its application benefits.
8 Reasons Why Developers Switch to HOOPS Visualize
Learn why companies transition from homegrown graphics solutions to HOOPS Visualize and what the switch entails.
5 Essential Functions of 3D ACIS Modeler
Explore the core functions of 3D ACIS Modeler: creating, modifying, querying, managing, verifying, and healing.
The Future of CAM Workflows
Explore current and future Computer-Aided Manufacturing workflows and ways to enhance CAM.
Automatic CAM (ACAM) in Subtractive CNC Machining
Discover Automatic CAM, the enabling processes, and its application benefits.
8 Reasons Why Developers Switch to HOOPS Visualize
Learn why companies transition from homegrown graphics solutions to HOOPS Visualize and what the switch entails.
5 Essential Functions of 3D ACIS Modeler
Explore the core functions of 3D ACIS Modeler: creating, modifying, querying, managing, verifying, and healing.
The Future of CAM Workflows
Explore current and future Computer-Aided Manufacturing workflows and ways to enhance CAM.
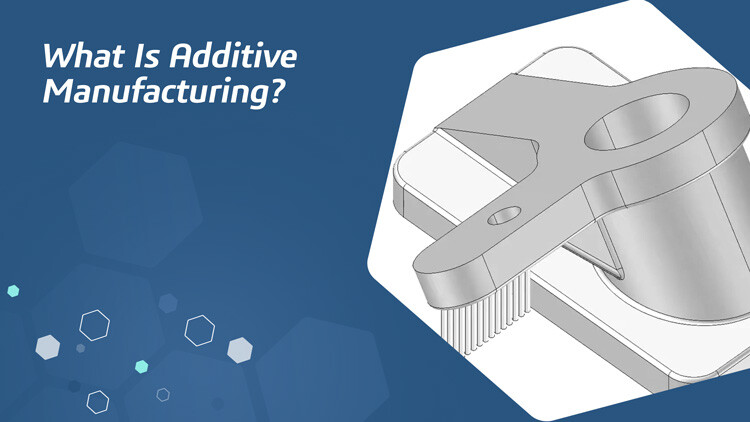
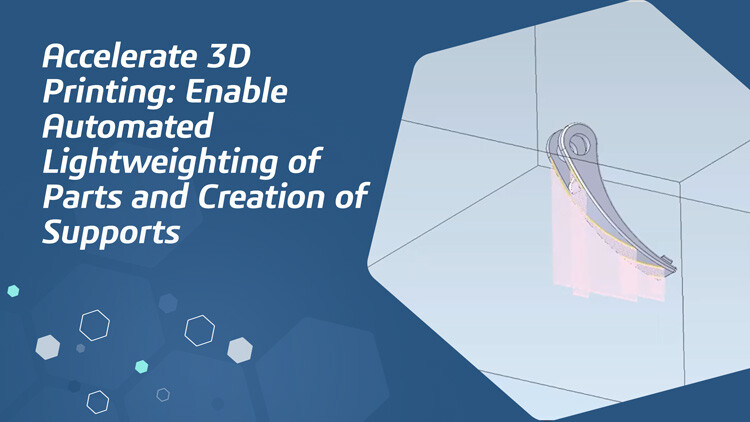
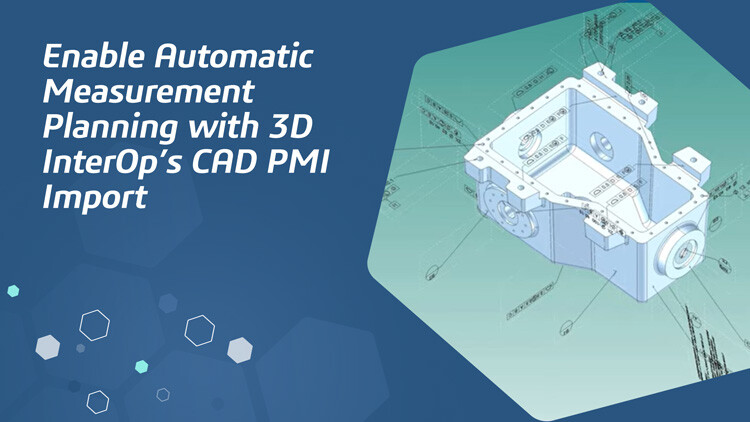
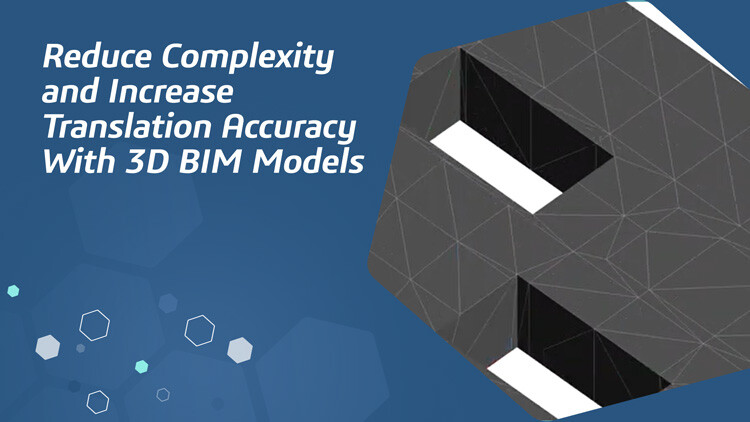
.jpg?width=1440&name=Sketcher-Feature-in-the-Application-Graphics-Manager-(AGM).jpg)
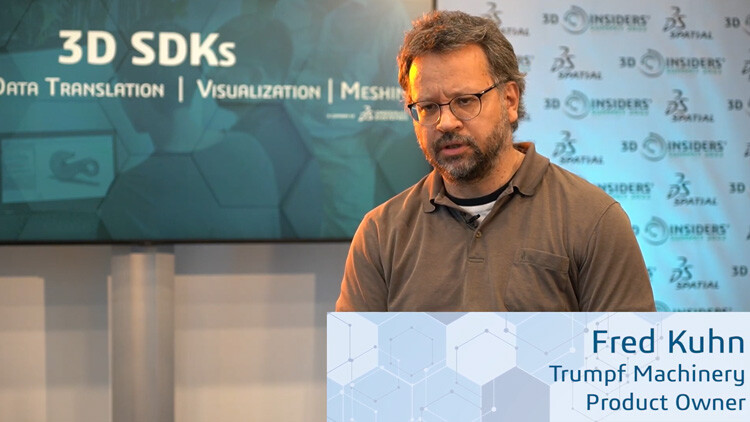